Gemeinsam mit der Distributed Design Plattform fördert das Happylab kreative Talente, die an der Schnittstelle von Design und Maker-Bewegung tätig sind. Von September 2022 bis Februar 2023 fand bei uns im Happylab die Distributed Design Residency statt, bei der wir Maker*innen und Designer*innen bei der Realisierung ihrer Projekte unterstützen konnten. Herausgekommen sind eindrucksvolle Projekte, die im März 2023 bei uns im Makerspace ausgestellt werden!
Sechs Monate Distributed Design Residency sind wie im Flug vergangen! Wir gratulieren unseren 8 Residents zu ihren großartigen Projekten und stellen sie euch hier im Detail vor. Wer die Projekte live bestaunen will, hat noch bis 31. März 2023 Zeit, bei uns im Lab vorbeizuschauen!
Die Distributed Design Residency geht ab September 2023 in die nächste Runde! Der Open Call ist bereits geöffnet und läuft bis 10. Juni 2023, wir freuen uns auf eure Anmeldungen!
Feel Refill (MAria Levitsky & Daniil Chechin)
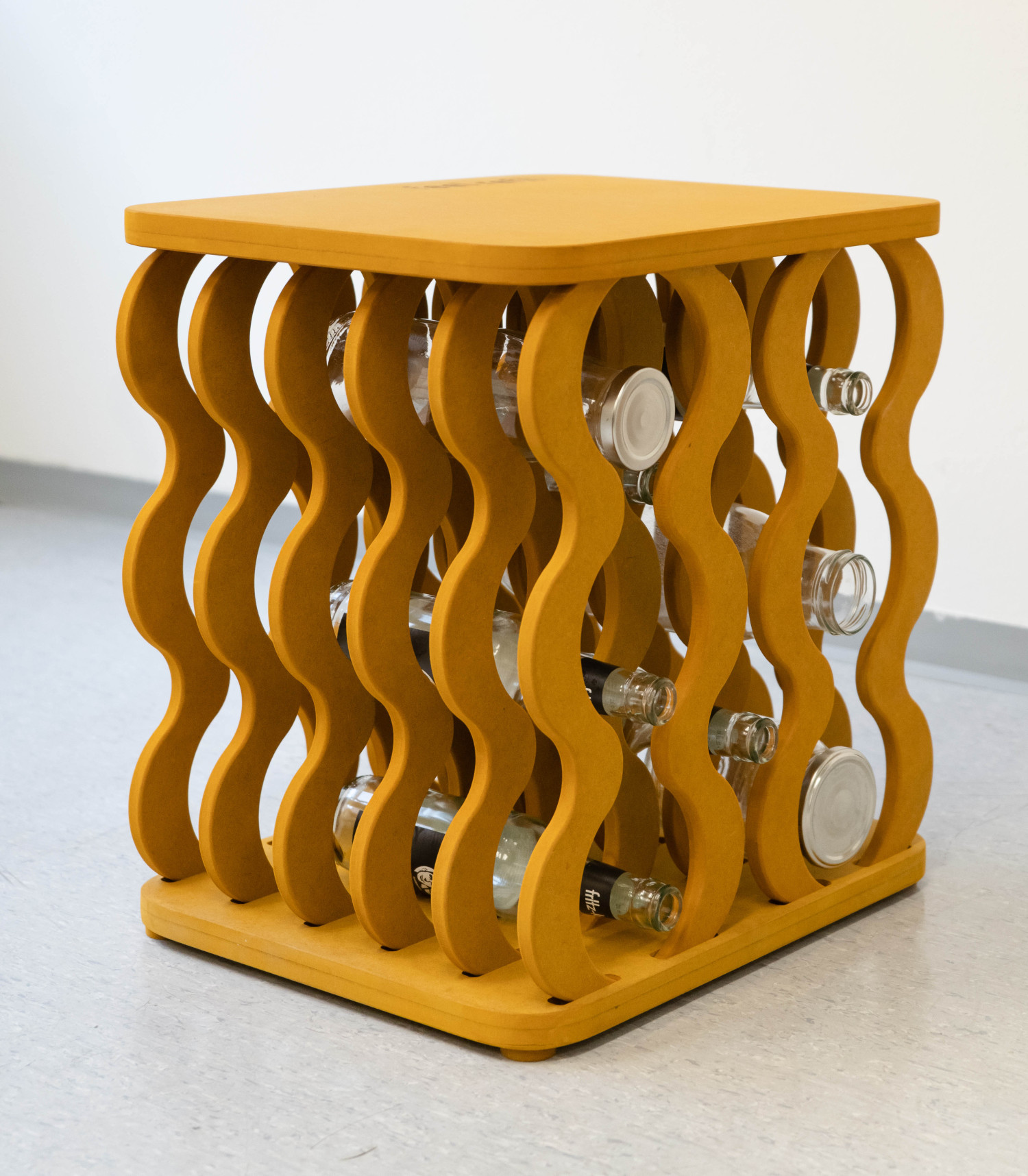
Feel Refill ist ein nachhaltiges Möbelprojekt von PROSTOR Studio (Maria Levitskaya & Daniil Chechin). Es bietet eine Designlösung, die Mülltrennung attraktiver machen und Menschen zum Handeln im Alltag motivieren soll.
Fell Refill wurde als Hocker mit der zusätzlichen Funktion der Flaschenablage unter der Sitzfläche entworfen. Acht 1-Liter-Flaschen passen zwischen die Öffnungen, die durch die wellenförmigen Elemente entstehen. Der Hocker ist kompakt und kann überall in der Wohnung als Sitzgelegenheit genutzt werden. Man könnte ihn zum Beispiel im Vorzimmer aufstellen, um daran erinnert zu werden, Pfandglas oder Recyclingbehälter zur Sammelstelle zu bringen. Als Material wurde MDF wegen seiner Vielseitigkeit gewählt. Das Material lässt sich einfach mit verschiedenen digitalen Fertigungswerkzeugen (z.B. CNC-Fräse) oder mit Handwerkzeugen bearbeiten. Es hat eine homogene Struktur und kann daher mit einer breiten Palette von Veredelungstechniken bearbeitet werden.
"Während der Distributed Design Residency im Happylab haben wir erfolgreich drei Prototypen hergestellt, wobei wir jede Variante im Hinblick auf die Effizienz des Materialeinsatzes, die Minimierung des Arbeitsaufwands und die Verbesserung der Designqualität verbessert haben. In unserer Vision ist Feel Refill ein vorgefertigtes Möbelstück in verschiedenen Farbvariationen, das von jeder Person leicht und ohne Werkzeug zusammengebaut werden kann. Aber für diejenigen, die daran interessiert sind, es selbst zu bauen, stellen wir das Projekt mit Open-Source-Tools zur Verfügung."
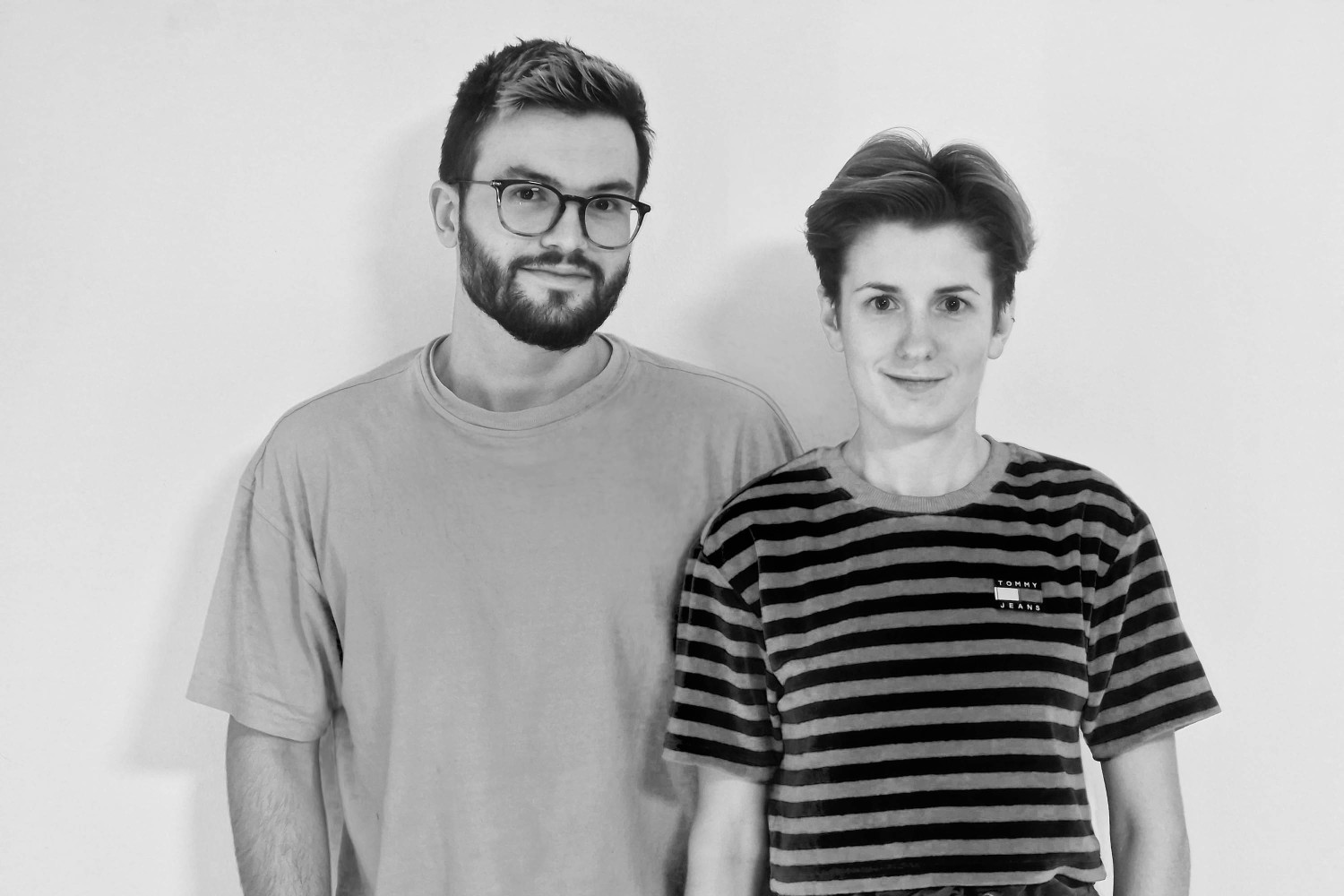
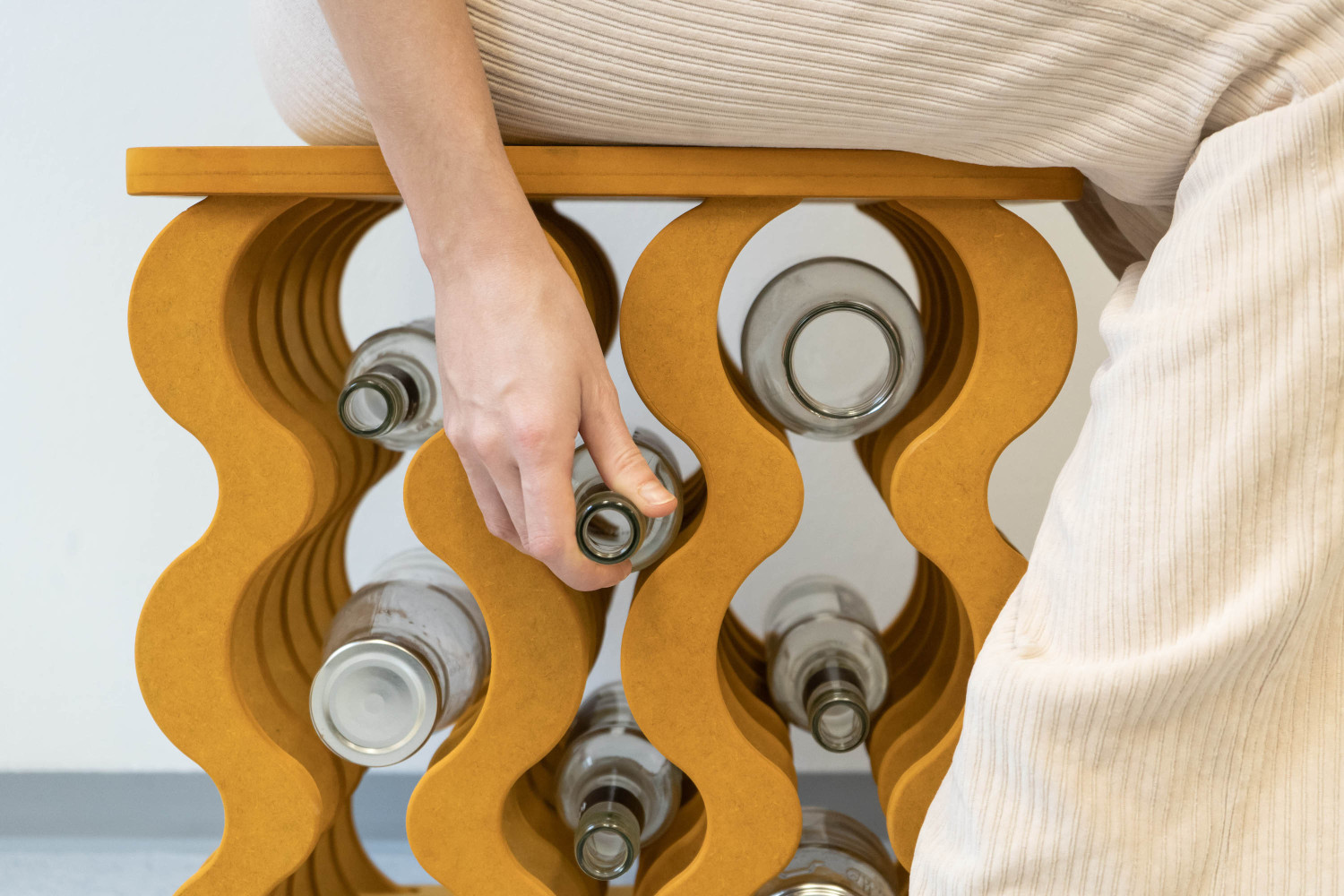
TMBR Scooter (Katrin Batko)
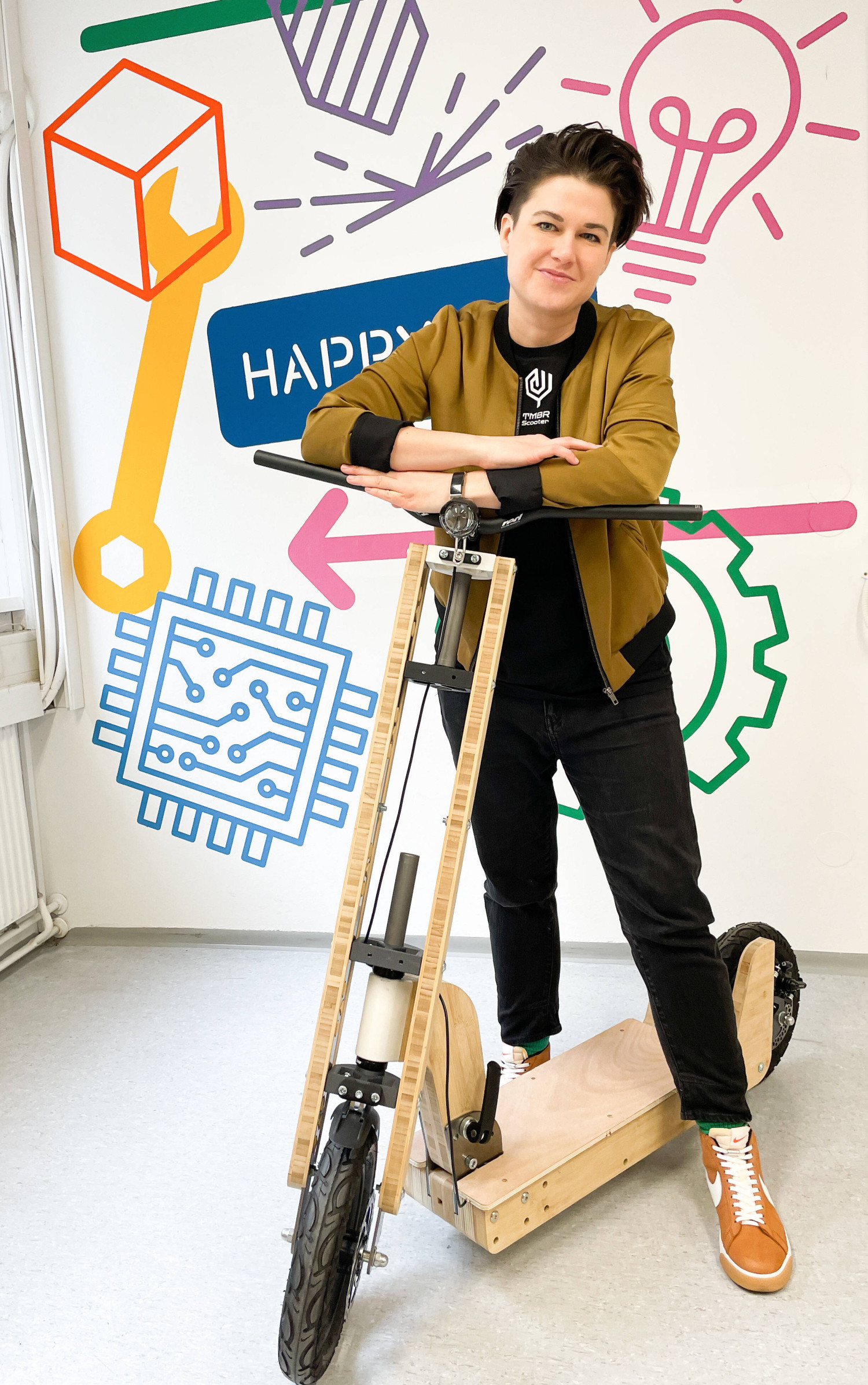
Katrin Batko beschäftigt sich mit Mikromobilität-Konzepten in der Stadt. 2015 kam die Idee, einen Scooter zu bauen. Damals ist bereits ein erster Prototyp in Zusammenarbeit mit einen Fahrradrahmenbauer entstanden, doch leider fehlte es Katrin an Zeit, um an den Prototypen weiter zubauen. E-Scooter waren damals auch noch nicht wirklich am Markt und es war sehr schwer elektronische Teile wie Motor und Räder zu bekommen. 2021 ist die Idee wieder entflammt, seitdem arbeitet Katrin an TMBR Scooter - einem nachhaltigen E-Scooter mit einem Rahmen aus modularen Elementen, der regional hergestellt werden kann.
Verwendet werden dafür Holz und Bambus von regionalen Fachhändlern. Ein zentraler Punkt ist das Design, das sich grundlegend von am Markt erhältlichen Scootern unterscheidet und dem E-Scooter eine neue Wertigkeit gibt - da diese oft wie Wegwerfprodukte behandelt werden. Um diesen Aspekt noch weiter auszubauen, verwendet Katrin am Markt erhältliche Fahrradteile wie Lenker, Vorbau und Steuersätze, damit eine Reparatur bzw. Adaptierung der Teile einfach möglich ist. Die meisten E-Scooter Hersteller verwenden fast ausschließlich auf das eigene Produkt zugeschnittene Teile, was einen Tausch und Reparatur teilweise unmöglich macht. Ein erster Prototyp von TMBR Scooter ist in den letzten Monaten im Happylab entstanden. Zum Einsatz kamen dafür Laser Cutter, Metall Laser, Metall- und Holzwerkstatt, CNC-Fräse, 3D-Drucker und der Finishing Bereich im Happylab.
"Im Rahmen der Distributed Design Residency hatte ich viel Zeit, unterschiedliche Materialien an den Maschinen im Happylab zu testen. Gerade am Metall Laser habe ich viel Schweiß und „Tränen“ vergossen. Es ist ein großer Vorteil, wenn der Projektarbeitsplatz direkt vor Ort ist und auch die diversen Teile und Werkzeuge gelagert werden können. Dadurch, dass ich im Rahmen der Residency mehr Zeit im Happylab verbracht habe, bin ich mit vielen anderen Mitgliedern ins Gespräch gekommen und habe wertvollen Input und Feedback erhalten. Auch die Zusammenarbeit und Unterstützung der Lab Manager war großartig. Bevor ich die Residency gestartet habe, war ich an der Acctek CNC-Fräse sehr unsicher. Nun traue ich mich problemlos, selbst Platten damit zu fräsen."

Mini Motoz - Design, Innovation und Nachhaltigkeit (Robert Poeckh)
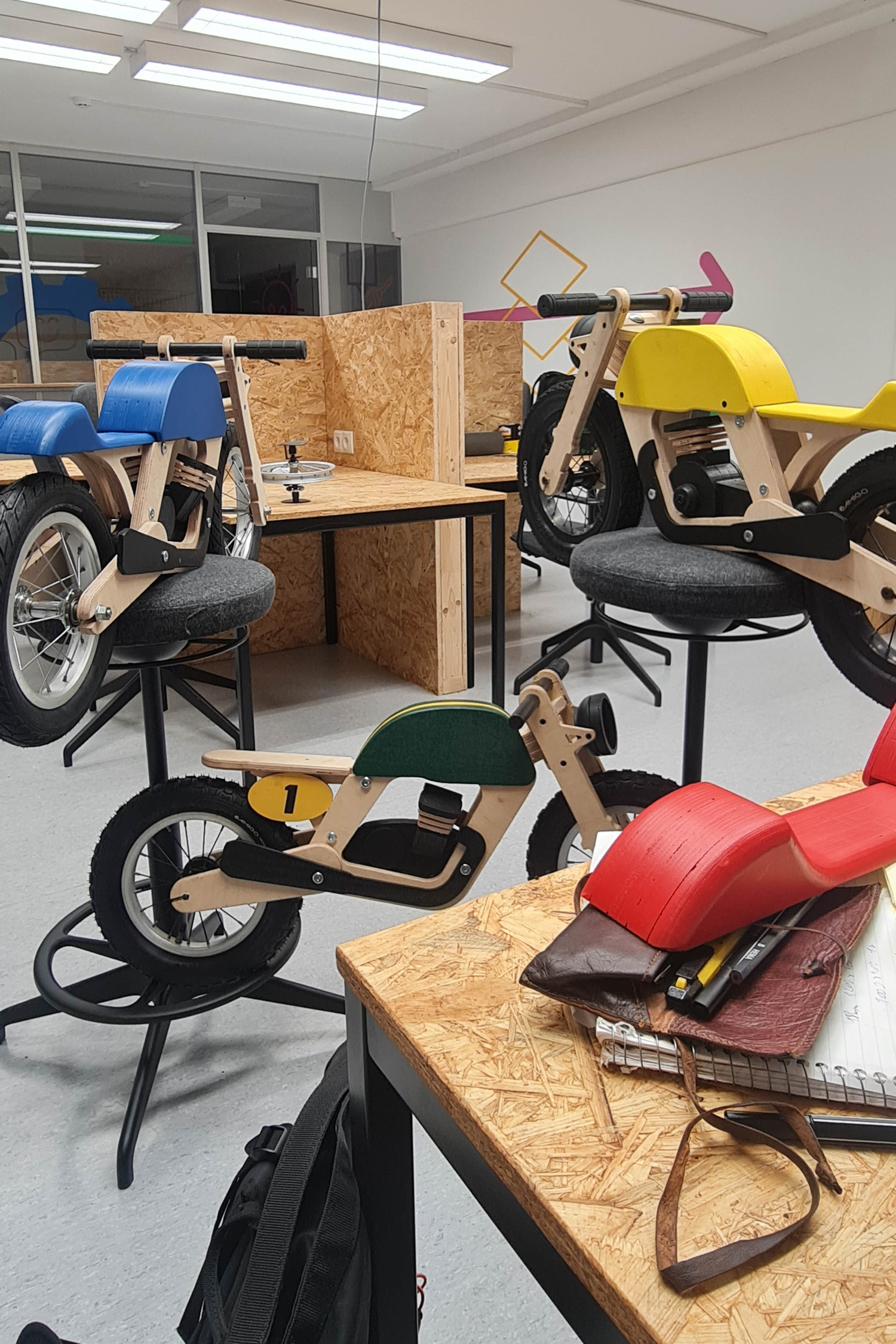
Die Mini Motoz sind einzigartige, handgefertigte Mini-Motorräder aus Holz, die nicht nur nachhaltig, sondern auch langlebig sind. Durch die Verwendung traditionellen Holzhandwerks in Verbindung mit modernen Fertigungstechniken wie CNC-Fräse und Lasercutter entstehen in begrenzten Stückzahlen kleine Unikate. Das Ziel war es, durch Innovation und Kreativität Laufräder zu entwickeln, die durch ihre Qualität und Ästhetik die kleinen Fahrer*innen ebenso wie großen Erwachsenen begeistern.
Während im Coworking-Space Materialien bestellt, Teile entworfen und die Produktion geplant wurden, sind im unteren Bereich Holzteile mit den Trotec Lasern graviert, sowie die Schnittmustern für die Kunstledersitze ausgeschnitten worden. Die einzelnen Kunstlederstücke wurden anschließend auf der Nähmaschine mit Schaumstoff und Vlies zusammengenäht. Mit Hilfe der Prusa 3D-Drucker wurden neben vielen Kleinen Gimmiks rund um das Projekt z.B ein Ständer sowie einzelne Jigs gedruckt, die die Nachbearbeitung der Holzteile erheblich vereinfachen. Über 53 der 69 einzelnen Holzteile, aus denen ein Bike besteht, wurden mit der Acctek Fräse aus Multiplexplatten gefräst und anschließend auf der Tischfräse nachbearbeitet, verleimt, geschliffen und im Finishingraum lackiert. In der Hobbywerkstatt wurden Schlauch und Reifen auf die Felgen montiert und aufgepumpt. Am Ende wurden die Bikes dort zusammengebaut. Außerdem kommen auch Bandsäge - Metall und Holz- Kappsäge, Plotter, Stickmaschine, Bandschleifer, Standbohrer zum Einsatz.
"Kurzum ohne das Happylab und die Kombination von Maschinen und Fertigungstechniken wär das Projekt kaum bis gar nicht durchführbar gewesen."
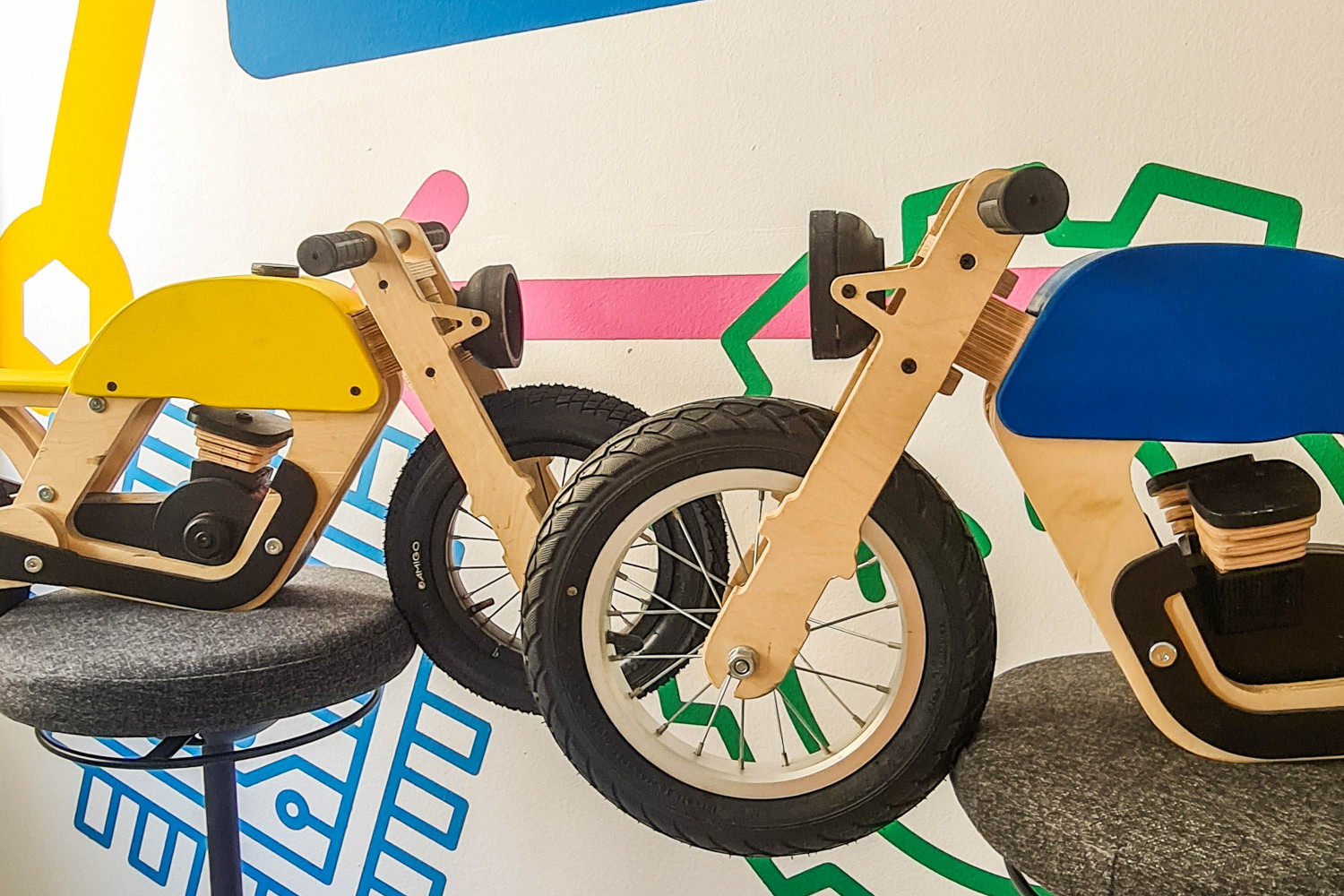
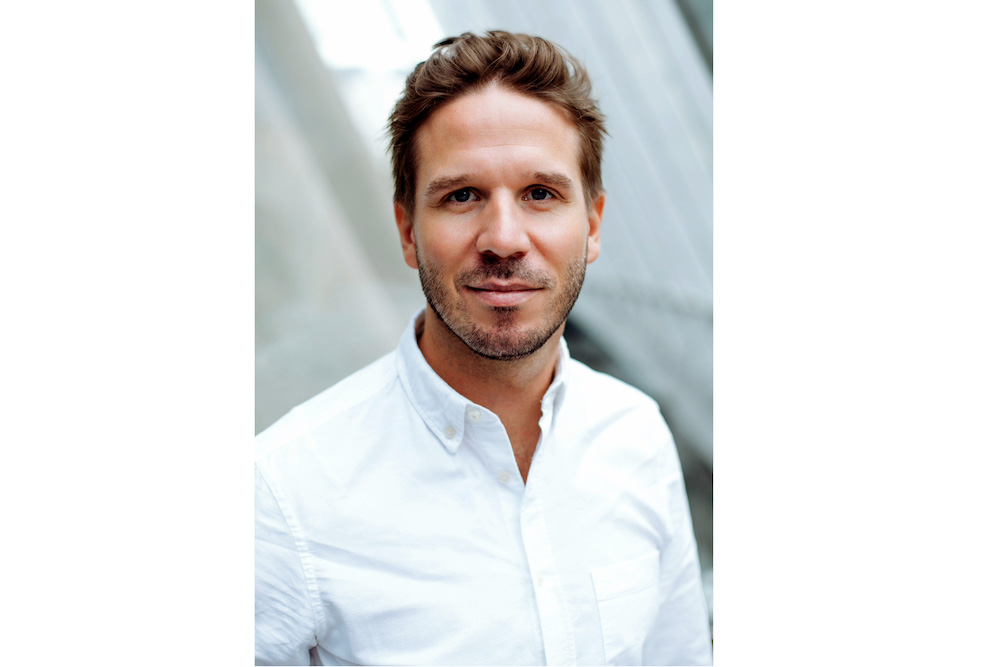
QuadO Schmuckkollektion (Konstanze Prechtl)
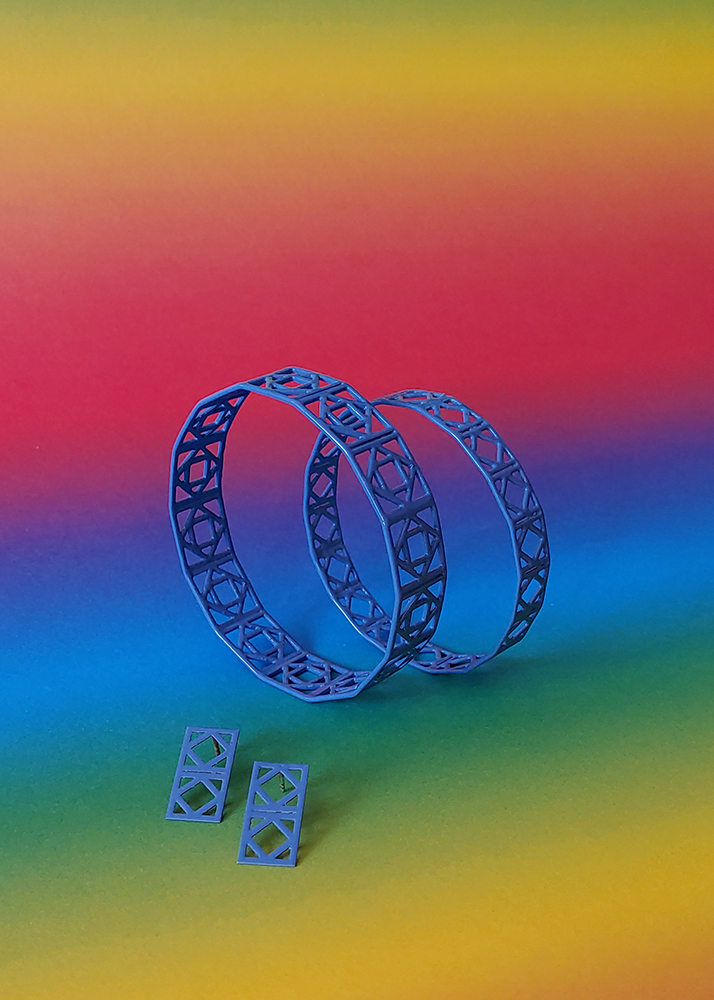
QuadO ist die neue Schmuckkollektion aus Edelstahl, Messing & Silber der freischaffenden Künstlerin & Schmuckdesignerin Konstanze Prechtl.
Der Designprozess beginnt bei Konstanze meistens mit einer groben Skizze und einem Papiermodell. Dieses hilft ihr dabei zu sehen, wie das ganze dreidimensional wirken könnte. Im nächsten Schritt nutzt sie digitale Zeichen-Programme, um die Modelle exakt auszuarbeiten. Die Modelle werden plan am Metall Laser ausgeschnitten und anschließend durch Knicken in Form gebracht. Anschließend werden die Modelle versäubert und bei Konstanze im Atelier weiterbearbeitet. Das heißt, sie werden gefeilt und geschmirgelt, in Form gebogen und gegebenenfalls gelötet oder mit Ohrsteckern verbunden. Im letzten Schritt werden die Stücke dann pulverbeschichtet.
Bei den Designs der neuen Kollektion hat Konstanze eine Form aufgegriffen, die sie zuletzt in größeren Arbeiten (Bilder, Schmuck und Objekten) umgesetzt hat: Quader und Würfel, die leicht angeschnitten sind und deren Form zwischen Zwei- und Dreidimensionalität changiert.
"Die gelaserten Stücke habe ich bislang im Ausland fertigen lassen, wollte dies aber sehr gerne selbst machen - zum einen, um so weit möglich alles vor Ort zu fertigen, zum anderen, um mit unterschiedlichen Materialien und Blechstärken zu experimentieren. Die Distributed Design Residency hat mir bei der Weiterentwicklung der Schmuckkollektion geholfen, durch die Möglichkeit an den Maschinen arbeiten zu können."
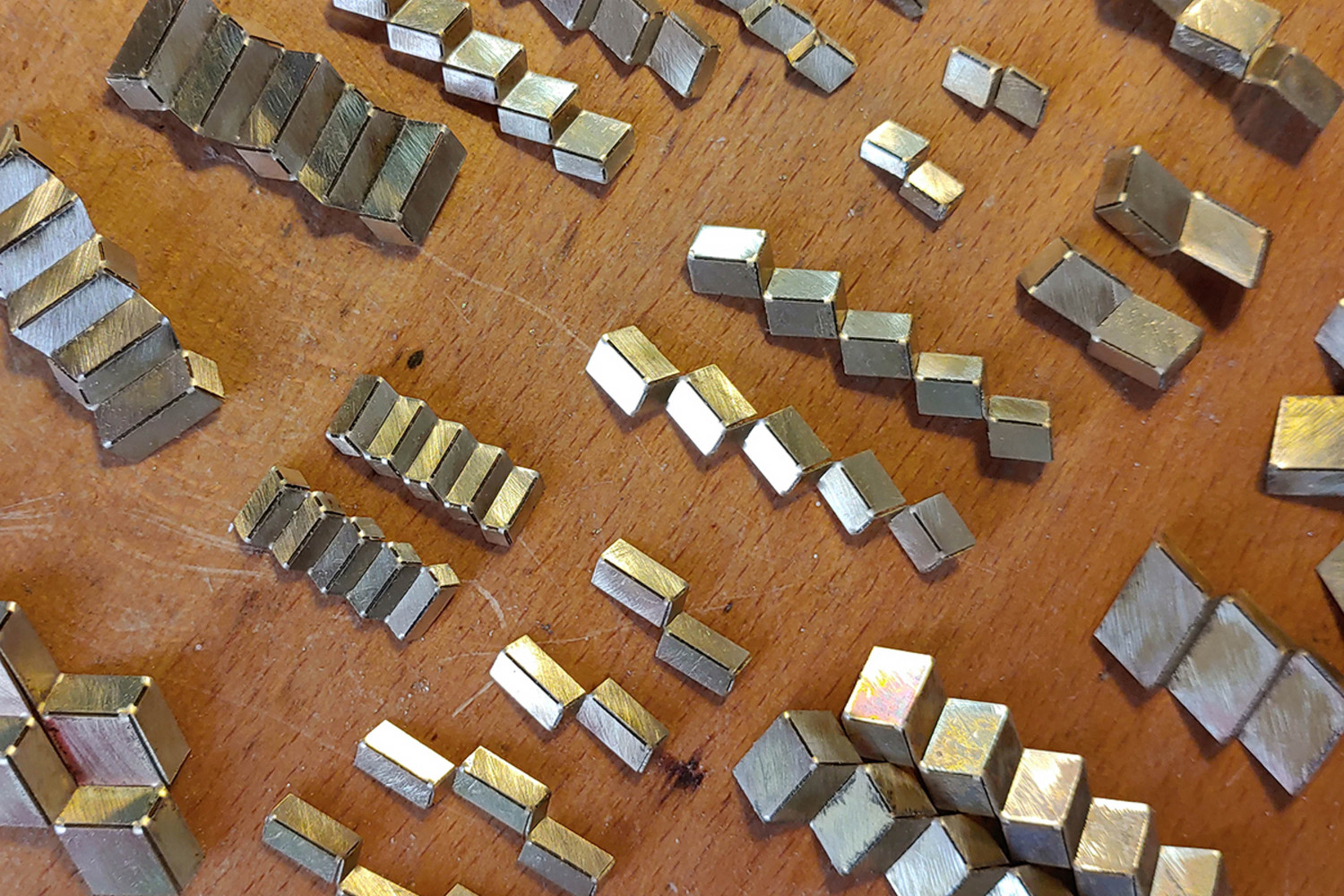

Biomaterialien (Cindy Fodor)
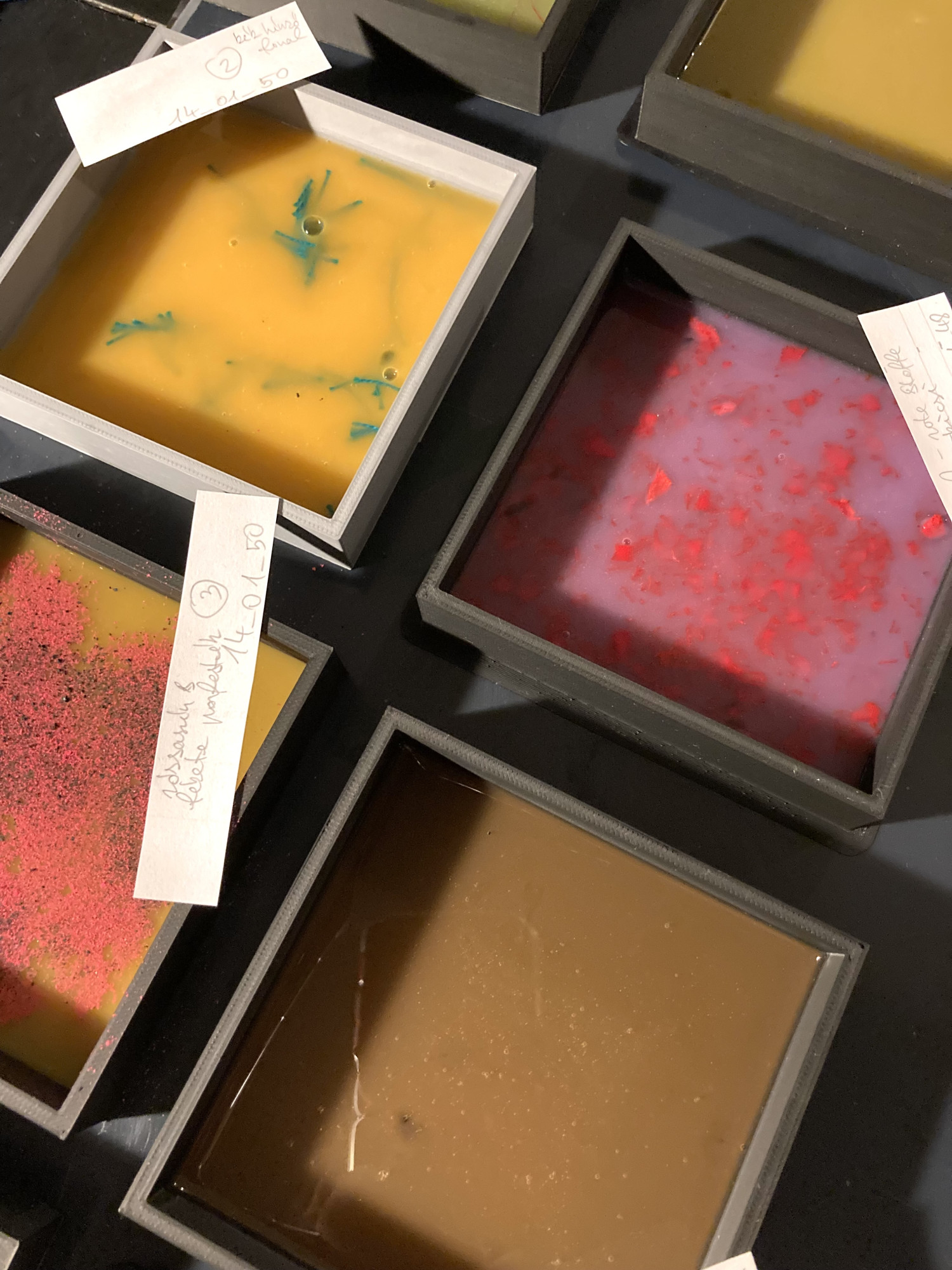
Cindy Fodor ist Modedesignerin. Sie arbeite gerne mit ihren eigenen Händen, aber auch mit neuen Technologien. Im Happylab hat sie für ihre Modekollektionen bereits mit unseren 3D-Druckern und Laser Cuttern experimentiert. Für die Zukunft hat Cindy sich vorgenommen, mit Biodesign und Biomaterialien zu experimentieren. Der Startschuss dafür fiel im Rahmen der Distributed Design Residency!
Für ihre Experimente hat Cindy mit vielen unterschiedlichen Zutaten gearbeitet. Drei davon, die sehr oft zum Einsatz kamen: Alginat, Agar agar und Gelatine. Die Zutaten werden gekocht, gemixt und die Masse anschließend in Formen gegossen und ausgehärtet. Die maßgeschneiderten Petrischalen entstanden an den 3D-Druckern im Happylab und sind mit speziellen 3D-Mustern versehen, um die Oberfläche der Biomaterialien zu formen.
Ihre Ergebnisse hat Cindy in einem "Biomaterialien Kochbuch" zusammengefasst, das sie auf Anfrage gerne an Interessierte weiterleitet!
"Mein Ziel für die Distributed Design Residency war es, ein Heimlabor einzurichten, in dem ich mit Biomaterialien experimentieren und selbst einige Proben herstellen kann. Ich habe außerdem ein Biomaterial-Kochbuch erstellt, damit jede*r, der/die sich für dieses Gebiet interessiert, beginnen kann."
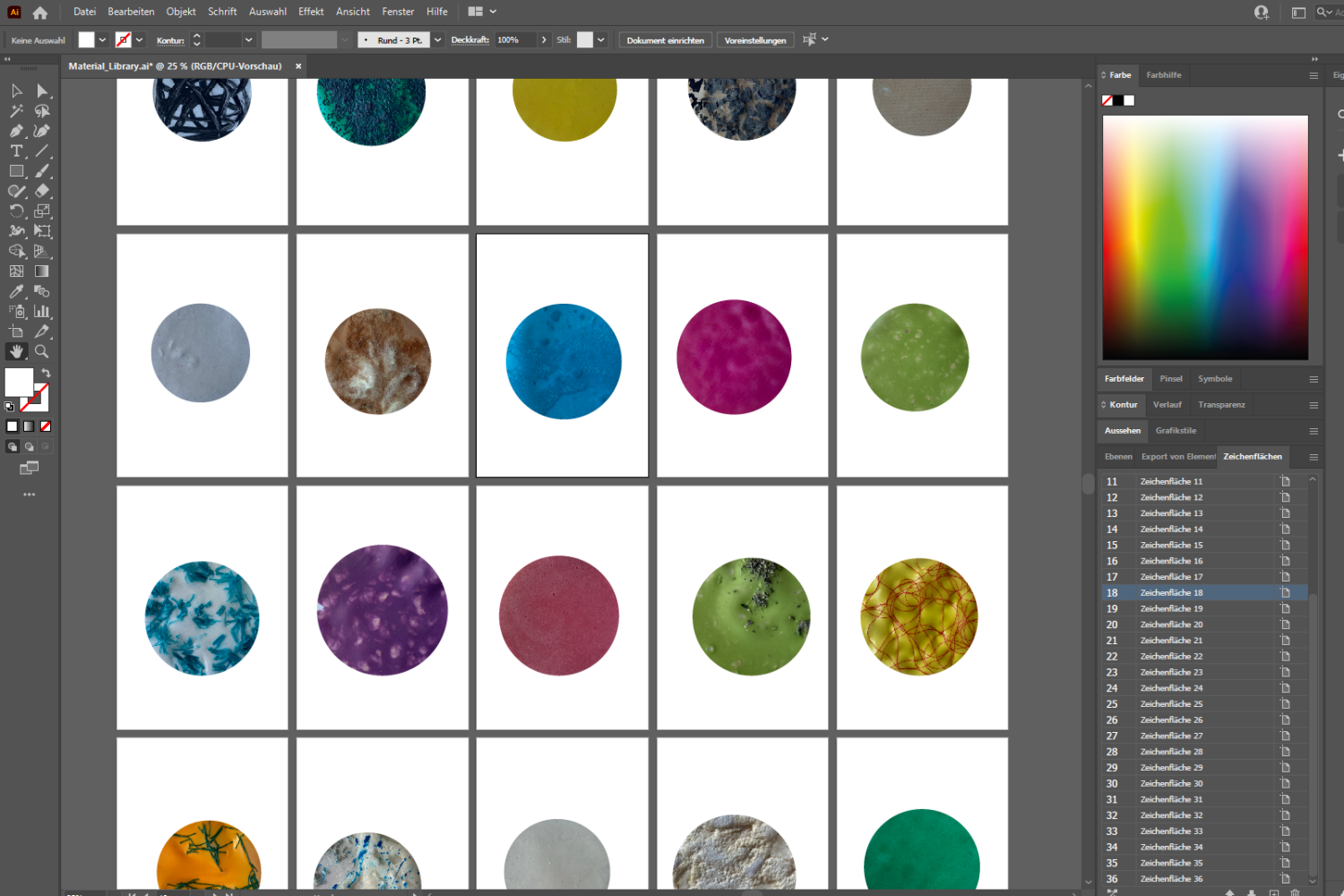

Alles Spitze (Stephanie Edelhofer)
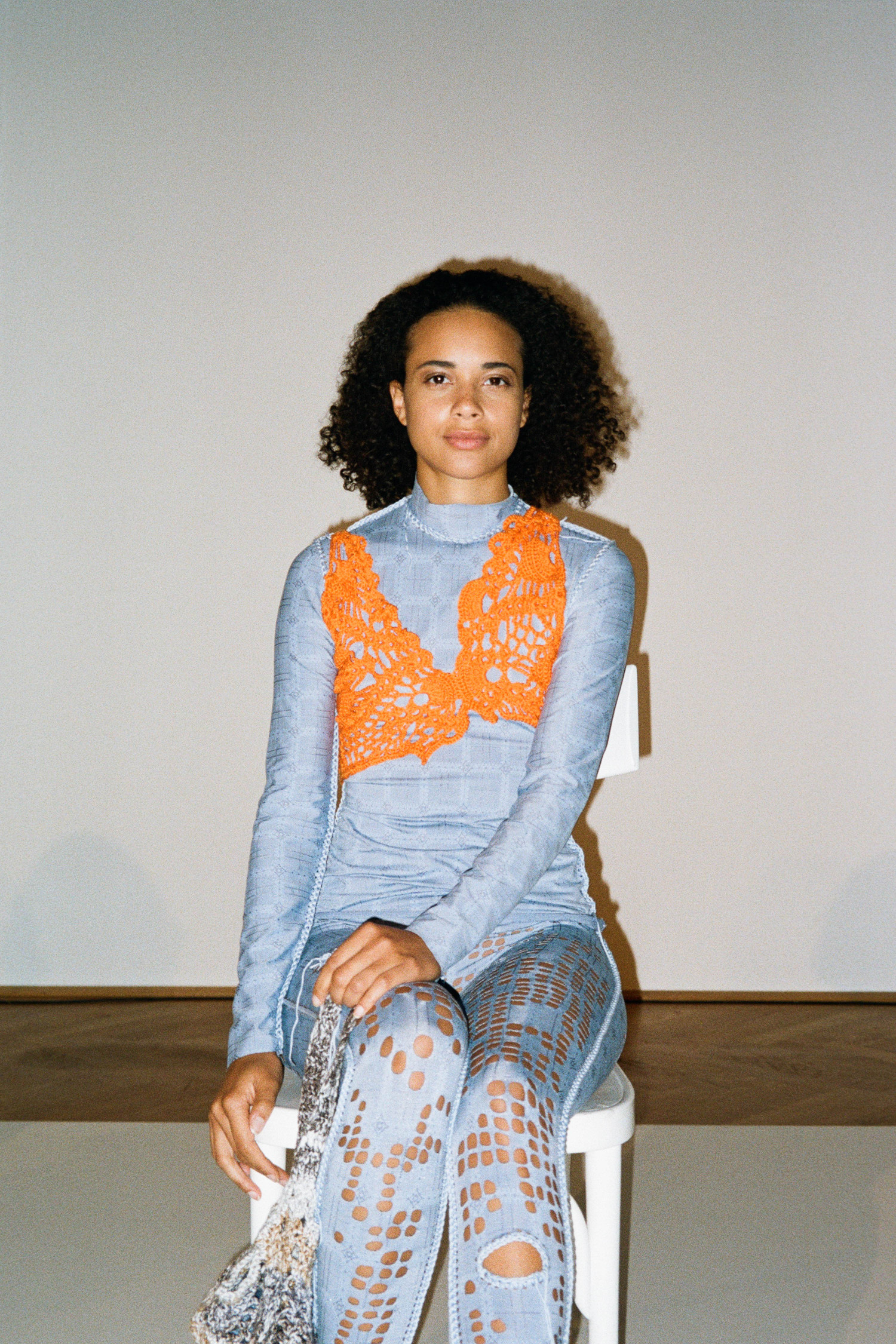
Das Projekt „Alles Spitze“ von Stephanie Edelhofer thematisiert die soziokulturelle Wertzuschreibung gegenüber Textilien und stellt einen Entwurf für konzernunabhängige Bekleiungsproduktion vor. Der Transfer des „Open Source“- Gedanken soll Einzug in den Modebereich finden, indem Schnitte frei zum Download bereit stehen, die mithilfe des Lasercutters, ohne viel textiles know-how umgesetzt werden können. In Anlehnung an die Ästhetik der Spitze, die früher den wohlhabenden Gesellschaftsschichten vorbehalten war, macht die digitale Fertigung dieses Material nun für alle zugänglich. „Alles Spitze“ spricht sich für lokale Produktion und gesellschaftliche Zusammenarbeit aus.
Für die Umsetzung des Projektes war Stephanie hauptsächlich am Laser Cutter und ein wenig an der Nähmaschine im Happylab beschäftigt. Spannend war für sie der Gedanke, die Ästhetik von Spitze mittels Lasertechnologie „nachzuahmen“. Die Distributed Design Residency hat Stephanie auch dafür genutzt, in andere Bereiche hinenzuschnuppern und sich neues Wissen anzuzeigen. In Zukunft sollen die Open Source Schnittmuster auf ihrer Website zum Download zu Verfügung stehen.
"Die täglichen Gespräche mit anderen Residents waren sehr fruchtbar und es war schön den voranschreitenden Prozess bei allen zu sehen. Die Mitarbeitenden im Happylab waren immer für Fragen da und haben auf großartige Weise Unterstützung angeboten. Danke hier vor allem an Lukas, der allseits geduldig wirkt!"
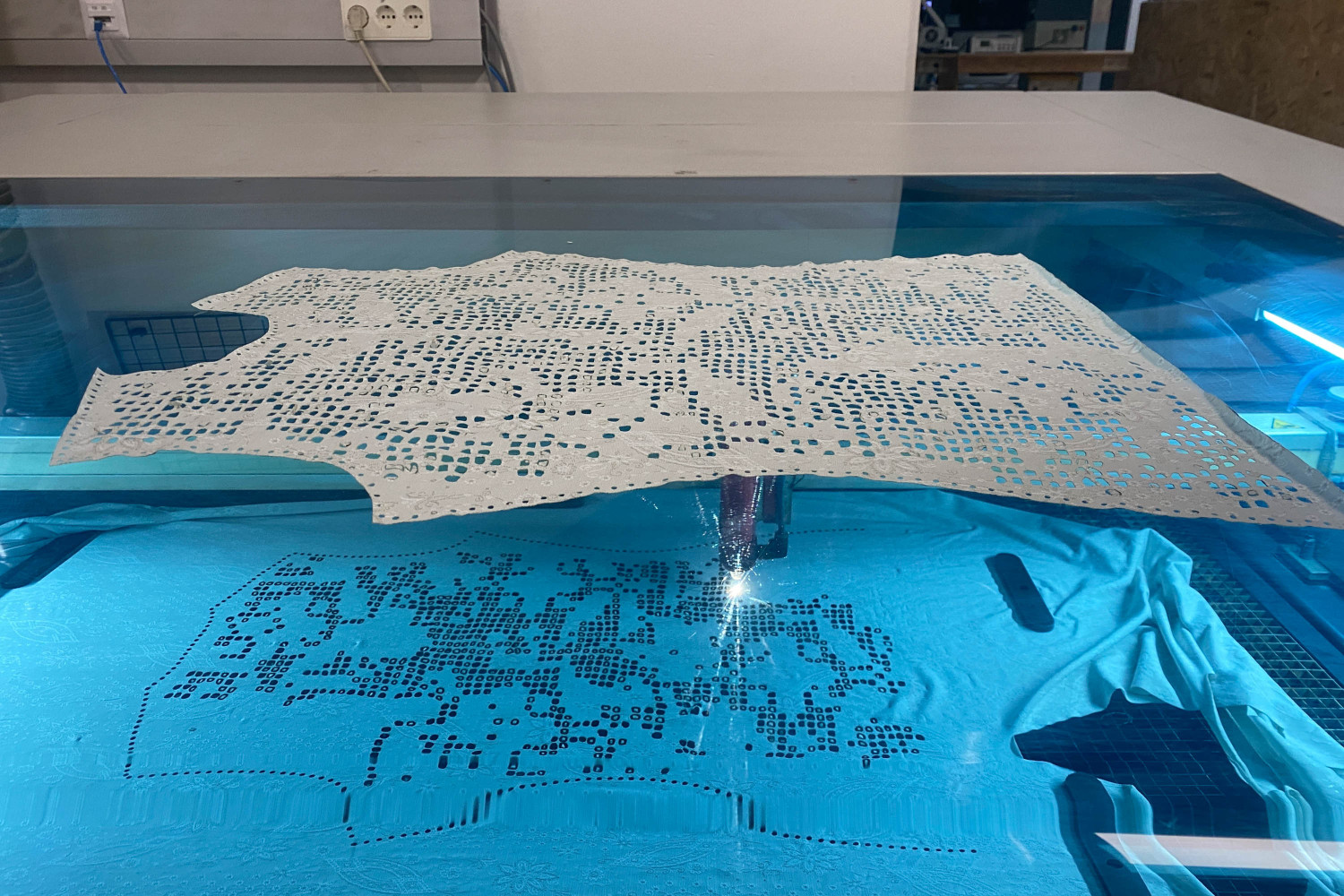
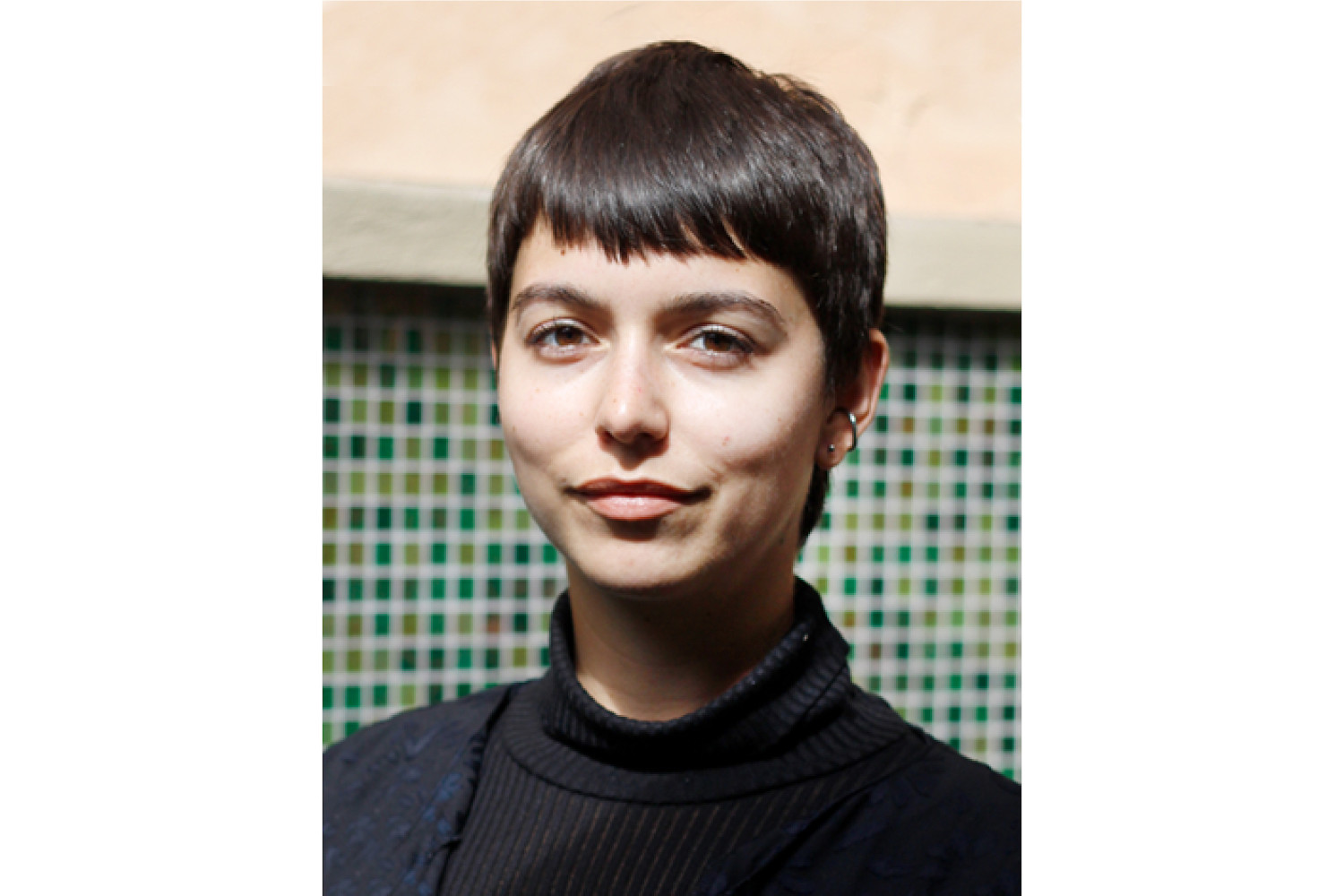
Schwangerschaftsmassageliege (Katharina Gleißberg)
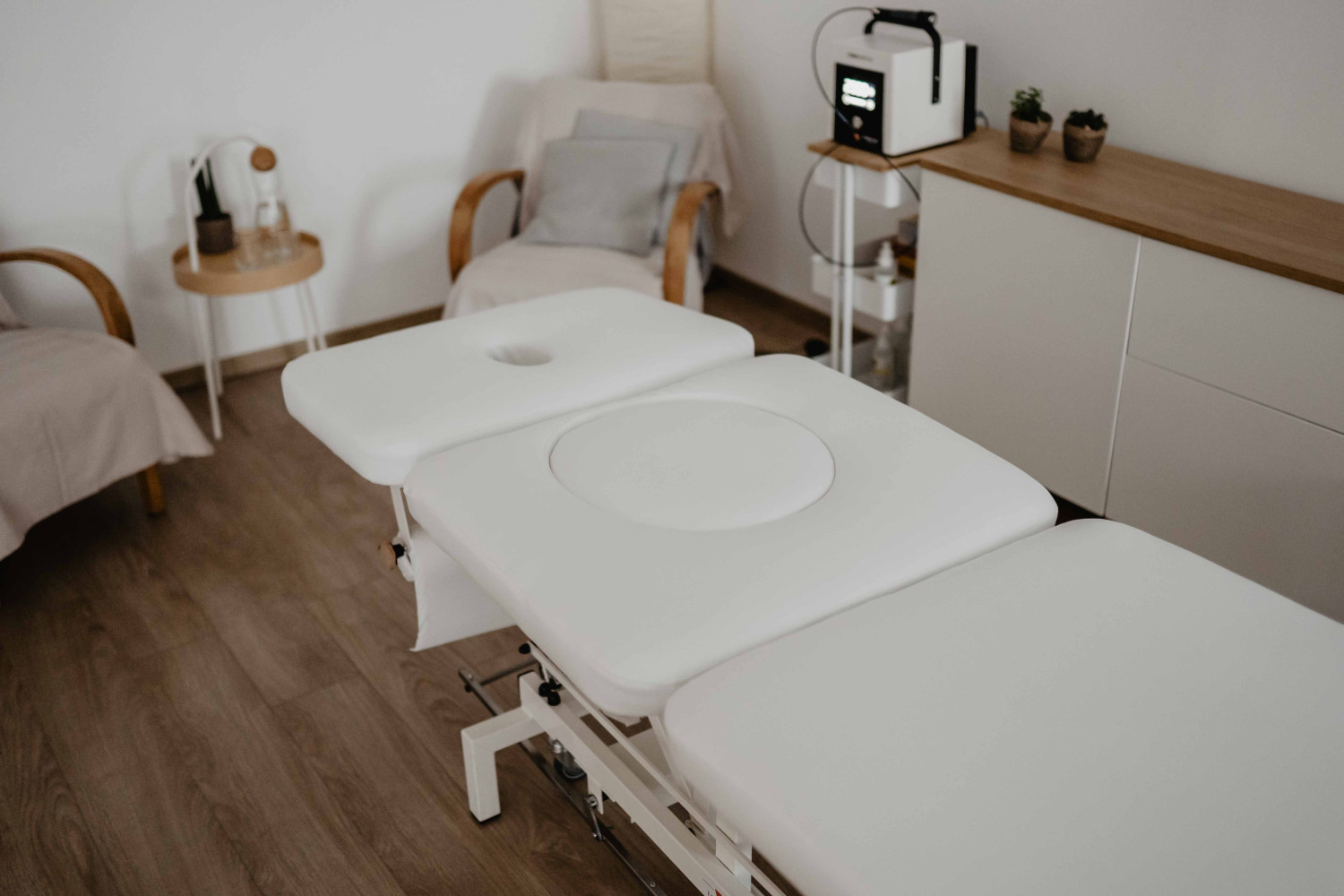
Nach Jahre langer Tätigkeit im Bereich der Heilmassage und vielen Schwangeren Patientinnen hat sich Heilmasseurin Katharina Gleißberg überlegt, eine Auflage für elektrische Massageliegen zu konzipieren, die einfach auf das Untergestell der vorhanden Liege geschraubt werden kann. Der Clou - das Loch für den Bauch. Der Bauch wird durch ein verstellbares Tuch gehalten um sich an jeden Bauchumfang anzupassen.
Im Happylab hat Katharina die CNC Fräse, den Lasercutter zum Zuschnitt der Schaumstoffteile und Näh- & Stickmaschine zur Erstellung des Lederbezugs verwendet.
"Vor allem der Co-Working Space und die Beratungsstunden im Rahmen der Distributed Design Residency waren super, ebenfalls das untereinander vernetzen war klasse!"
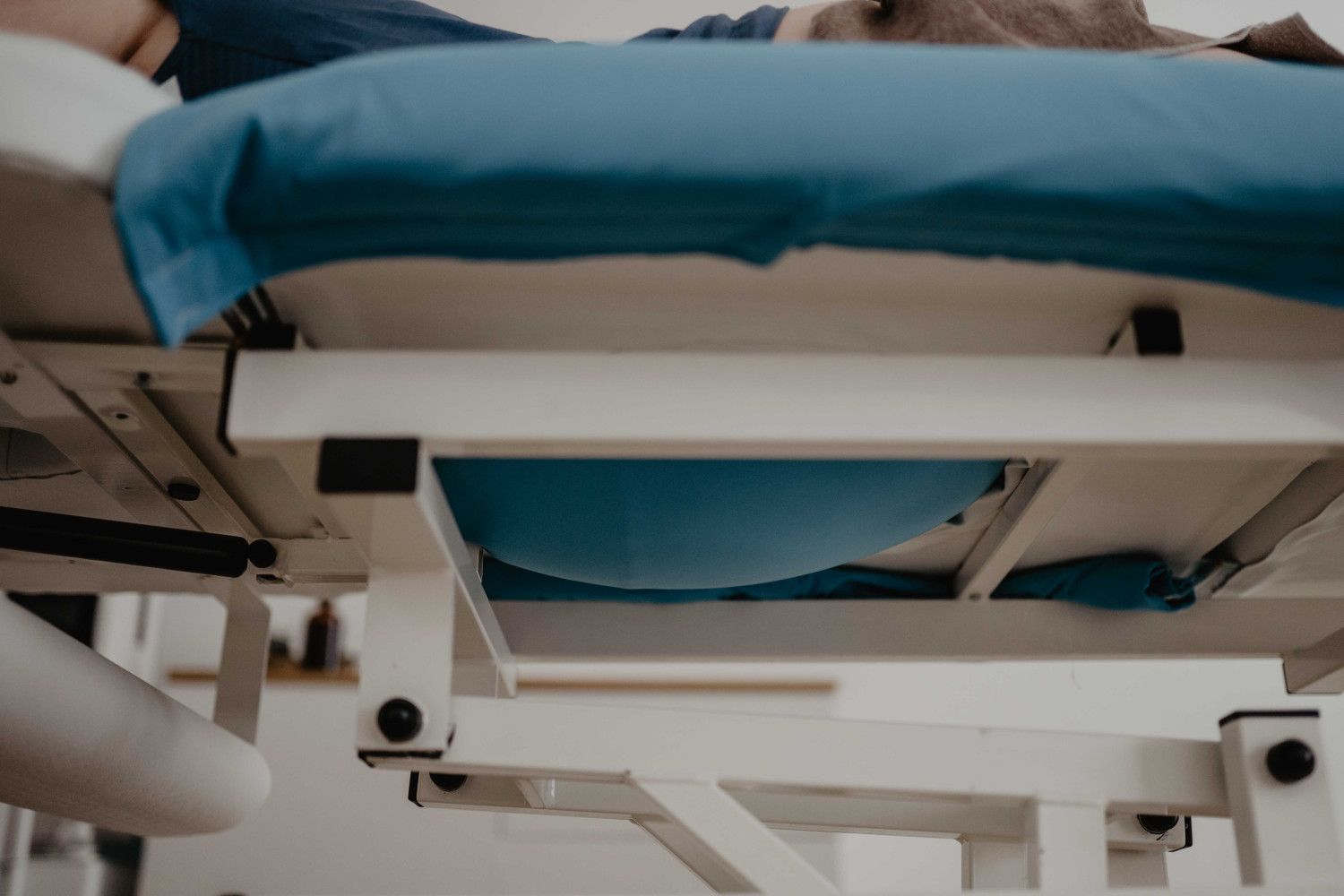
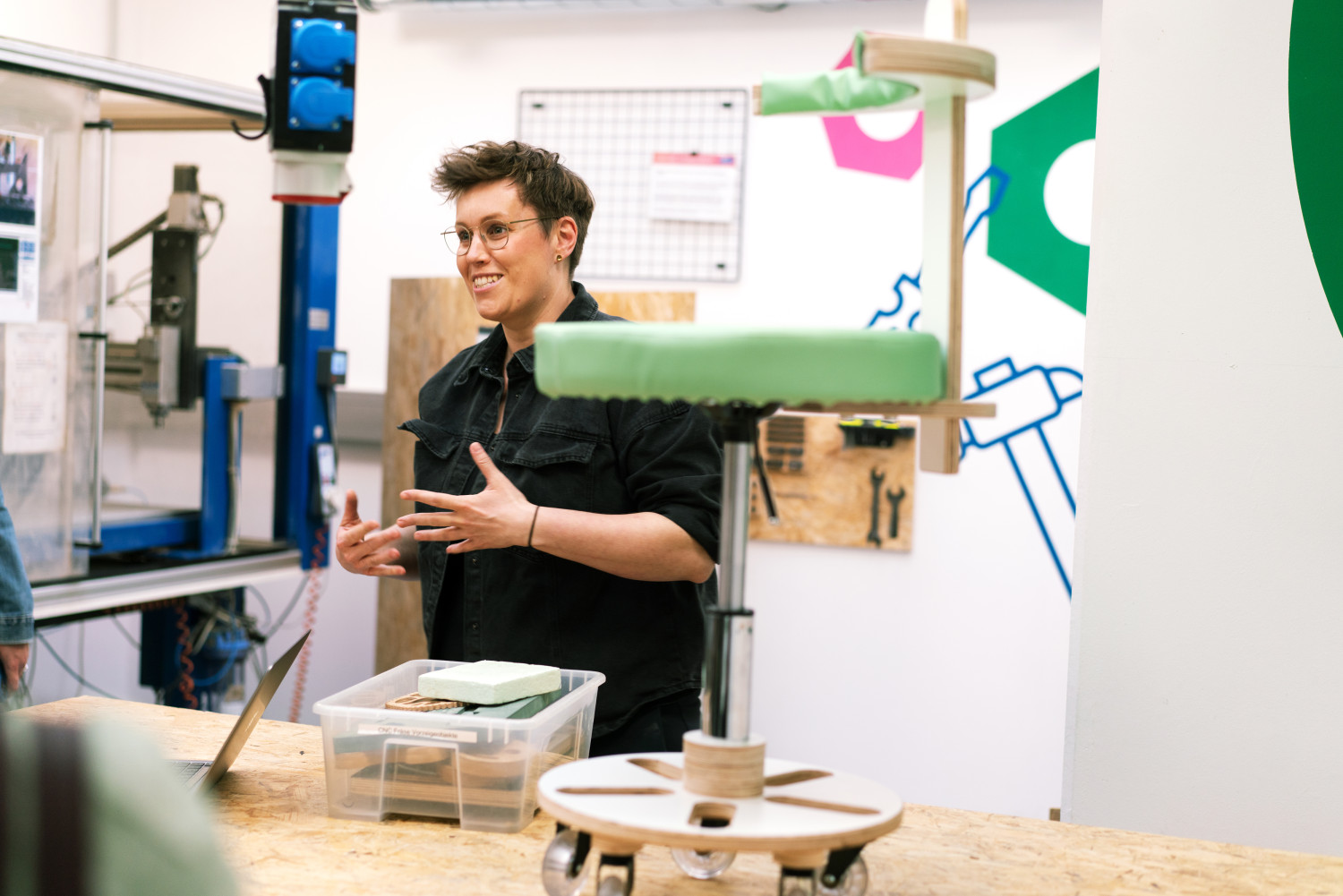