Wir freuen uns sehr, euch die finalen Projekte der Distributed Design Residency 2023/24 vorstellen zu dürfen. Sechs Monate lang – von September 2023 bis Februar 2024 – haben wir Maker*innen und Designer*innen bei der Realisierung ihrer Projekte bei uns im Happylab unterstützt. Die Resultate sind eindrucksvolle Projekte, die ihr den ganzen März 2024 bei uns im Makerspace bewundern könnt. Also schaut gerne vorbei!
Und für alle, die Interesse daran haben, selbst an der Distributed Design Residency teilzunehmen, haben wir gute Neuigkeiten: Gemeinsam mit der Distributed Design Plattform fördert das Happylab auch heuer wieder kreative Talente. Ab September 2024 starten wir in die neue Runde! Der Open Call ist bereits online und läuft bis 16. Juni 2024, wir freuen uns auf eure Anmeldungen!
HANDMADE MASSPRODUCTION - MARIIA SAMAHALA & MYKHAILO ZHUK
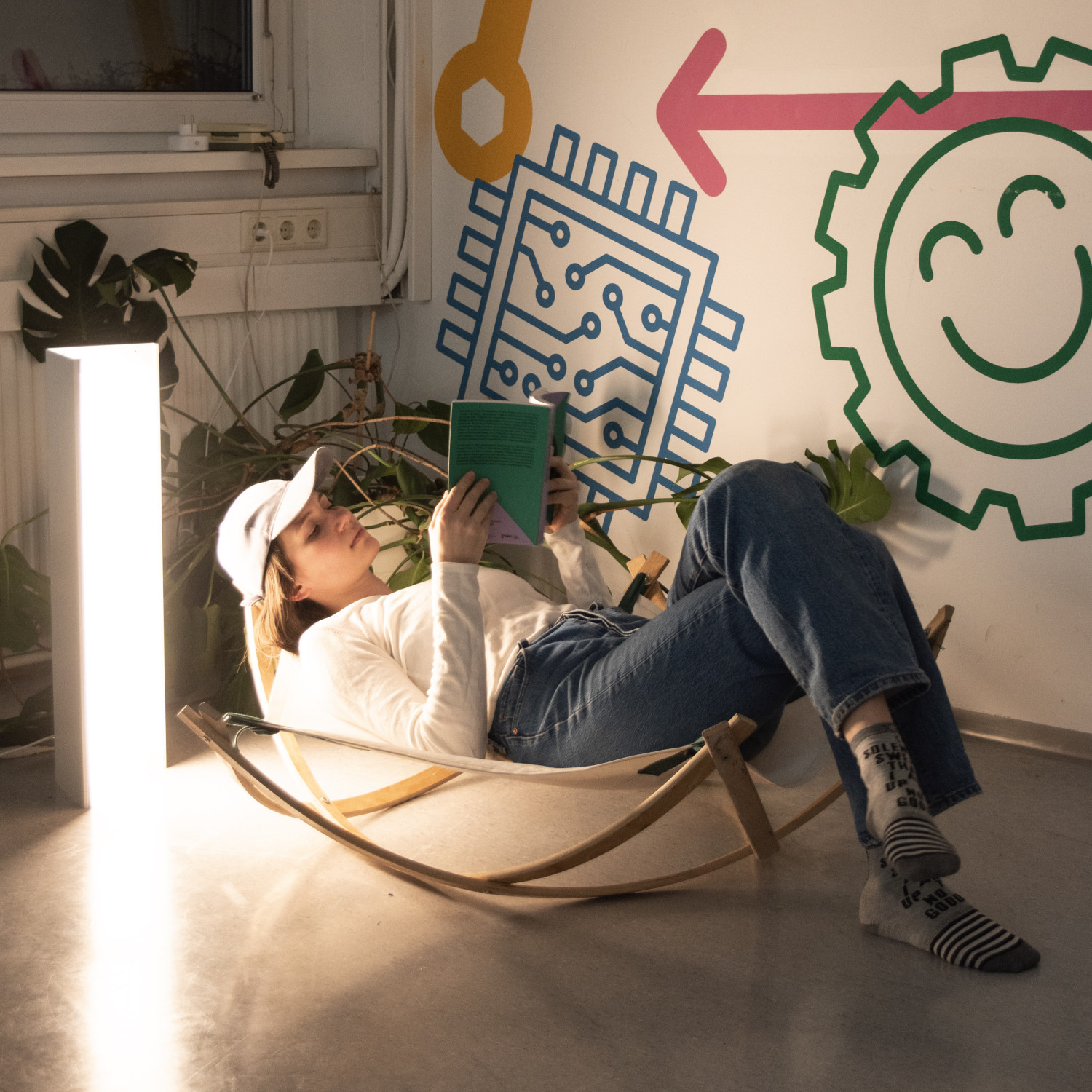
Mariia und Mykhailo glauben, dass die Minimierung von Abfall eine der Hauptmöglichkeiten ist, wie Designer*innen die Umweltauswirkungen ihrer Produkte verringern können. Es ging ihnen um ein Umdenken der Materialien, mit denen sie arbeiten. Im Rahmen der Distributed Design Residency haben sie ein Designprinzip getestet, das darauf abzielt, vorgefertigte Gegenstände als Material für den Bau neuer Designs zu verwenden. Dadurch sind ein Stuhl und eine Lampe aus wiederverwendeten Teilen entstanden. Der Stuhl besteht aus alten Lattenroststäben, die dampfgebogen und unter Spannung gesetzt wurden. Für den Lampenkörper haben die beiden ein Aluminiumprofil verwendet, das auf einem Schrottplatz gefunden wurde.
Ein weiteres Experiment richtete sich auf den im Happylab produzierten Abfall. Sie haben das Sägemehl aus der Holzwerkstatt als Basis für das Wachstum von Myzelmaterial verwendet, mit dem die Designer*innen in Zukunft intensiver arbeiten möchten.
„In den letzten 6 Monate haben wir dank der Residency viele neue Techniken ausprobiert und unser Skillset erweitert. Am meisten waren wir von dem Austauschprogramm begeistert, durch das wir erfolgreiche Maker*innen und Designer*innen mit uns sehr naheliegenden Werten kennenlernen durften. Das projektorientierte Format hilft auch, die Arbeitsprozesse zu strukturieren und zu evaluieren.“
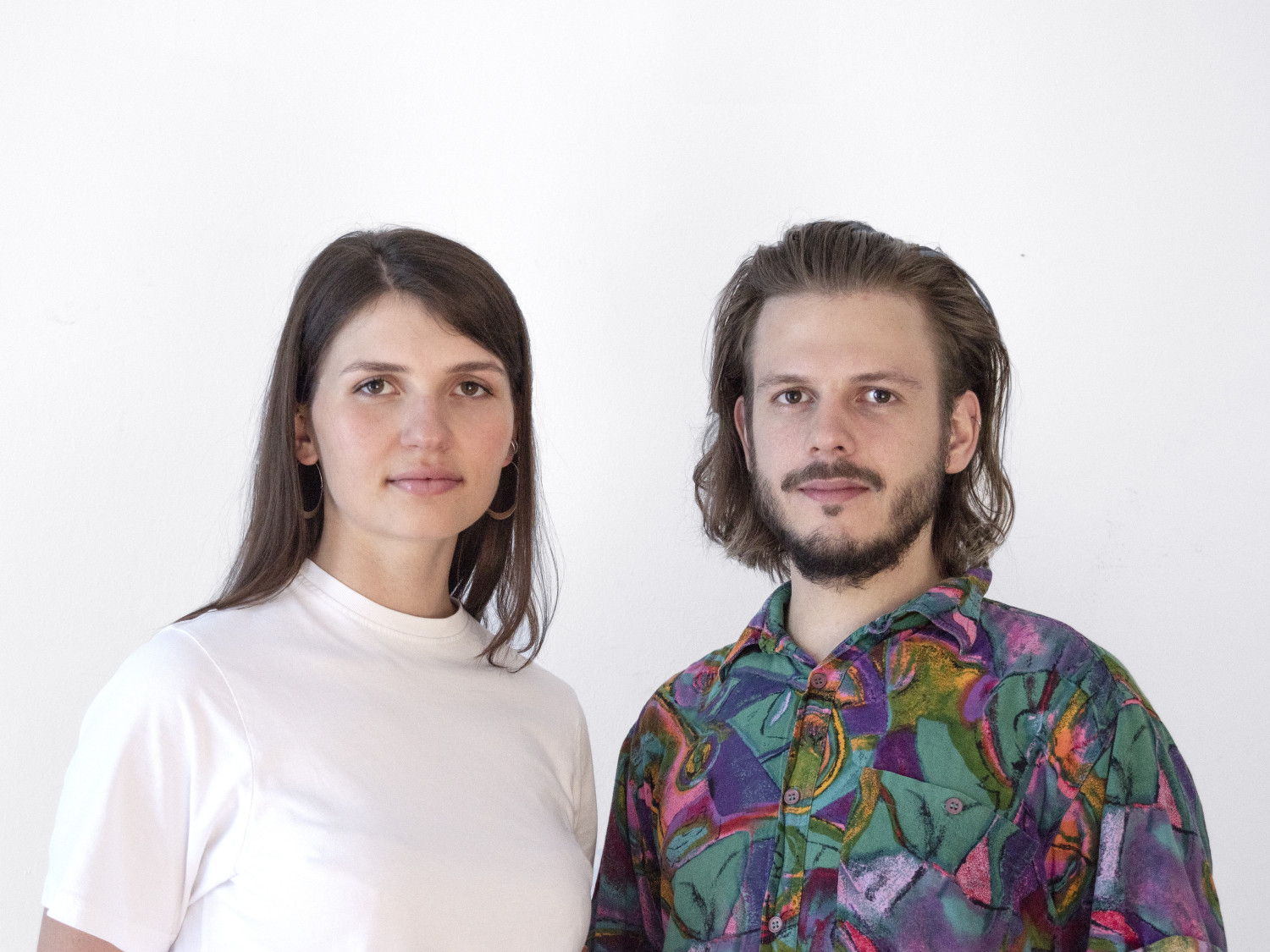
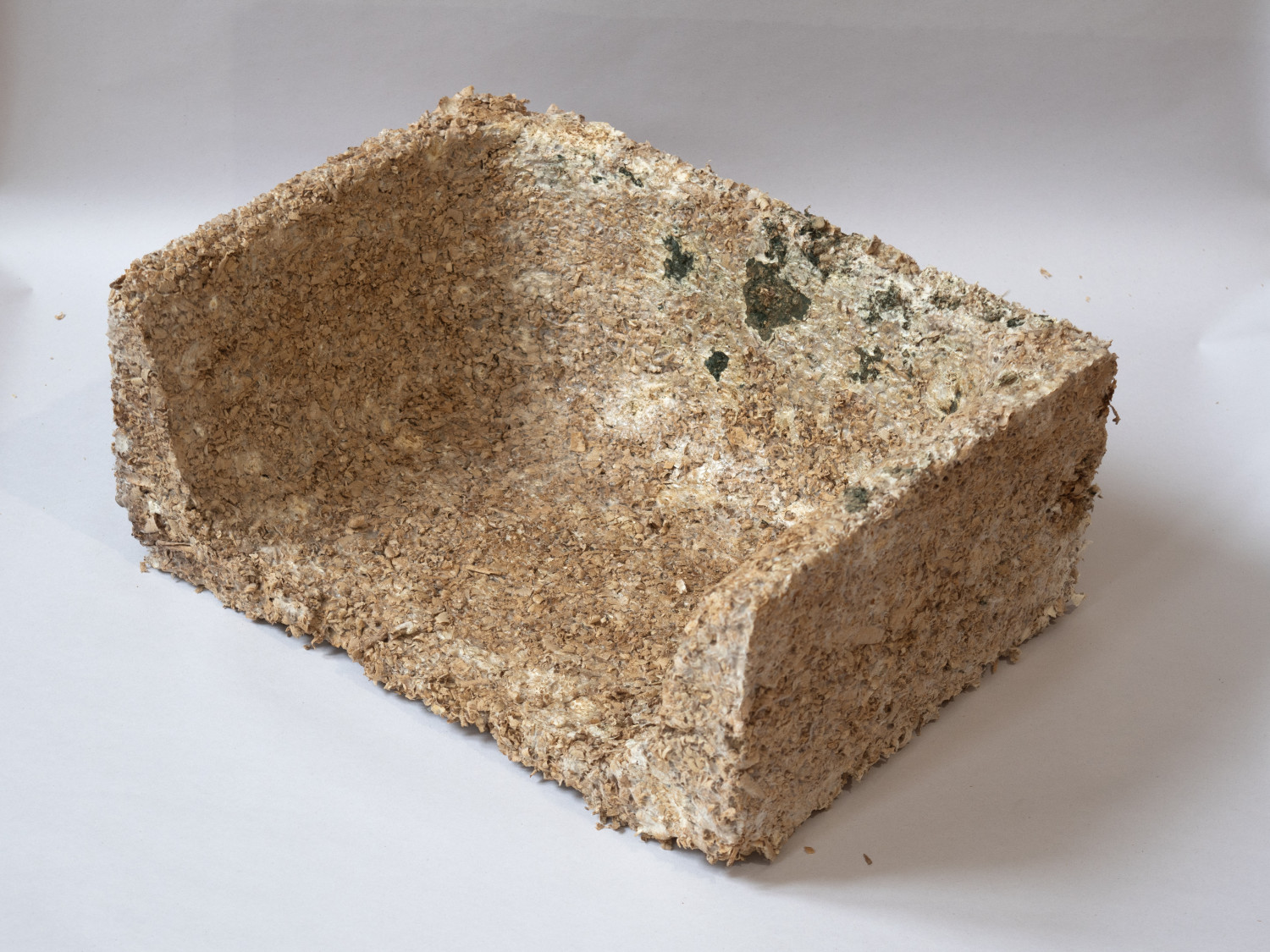
L(EFT)OVERS - NINA MCNAB
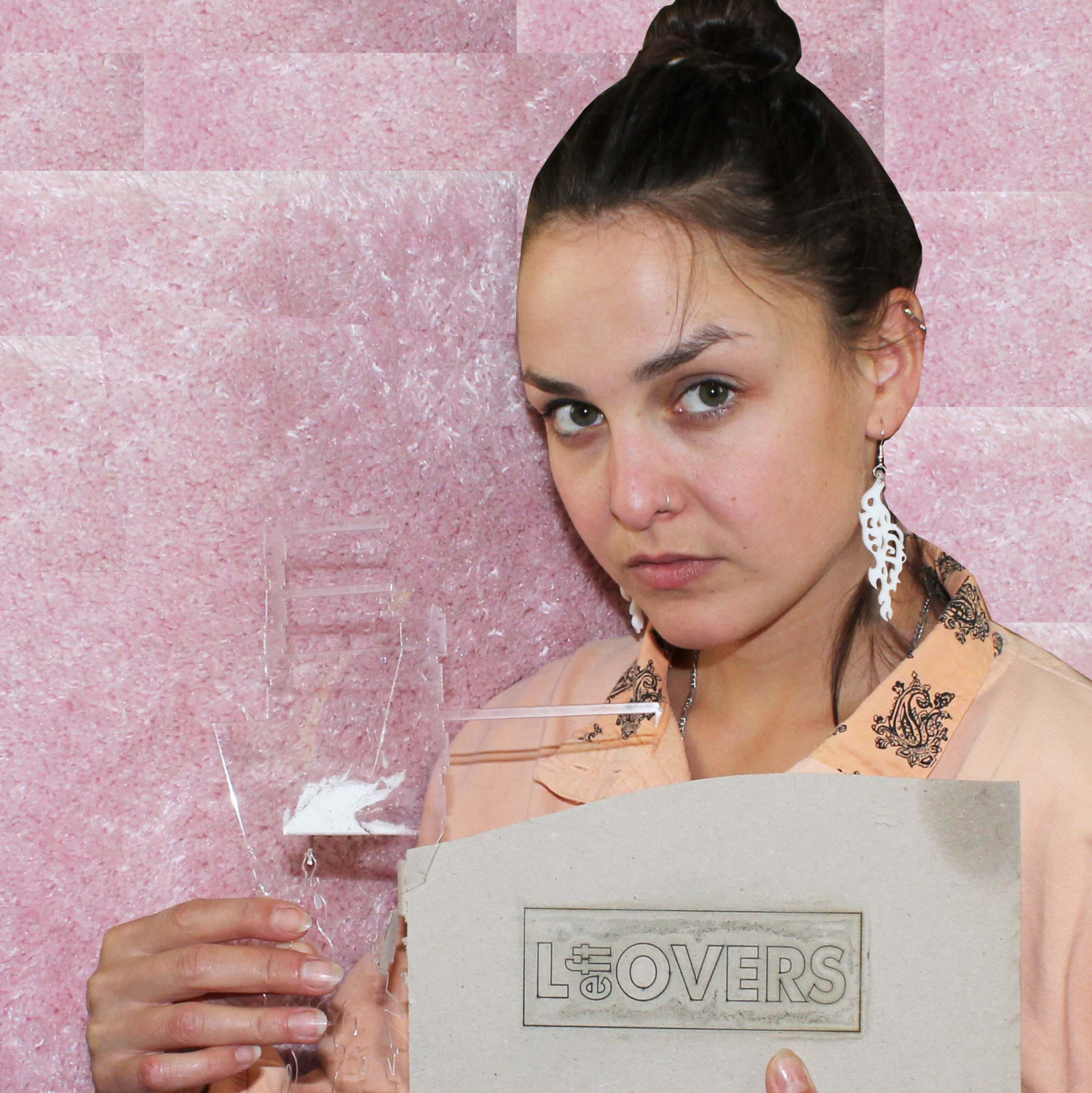
L(eft)OVERS ist eine kostenlose Datenbank an Vektoren, die Freiräume zwischen Laserfiles füllen. Dadurch wird die Restproduktion verringert und Ressourcen geschont. Die Vektoren – kleine praktische, nette oder spielerische Objekte – sollen aufzeigen, welches Potenzial vermeintliche Reste in sich tragen und dazu anregen, eigene Designs zu entwickeln und zu teilen.
Nina verbrachte mehrere Tage pro Woche im Happylab und hat dort primär den Lasercutter genutzt. Der Input und Austausch von und mit anderen Mitgliedern und Residents im Lab und Co-Working-Space hat ihr besonders gefallen.
„Durch die Residency konnte ich bestehende Skills digitaler Produktionspraxis fundieren und auf ein routiniertes Niveau heben, wodurch sich nicht nur eine effiziente Produktion ermöglichte. Das tiefere, praktische Verständnis ließ sich mir einen neuen Nutzungsraum digitaler Produktionsmaschinen im kreativen Zugang erschließen, welcher bereits in meiner künstlerischen Praxis Anwendung findet. Die persönliche und nahbare Betreuung unserer Projekte bedingte zudem ein motiviertes Arbeiten und ein Zugehörigkeitsgefühl nicht nur zur Happylab-Community, sondern auch zur gesamten Designer- und Makerszene.“
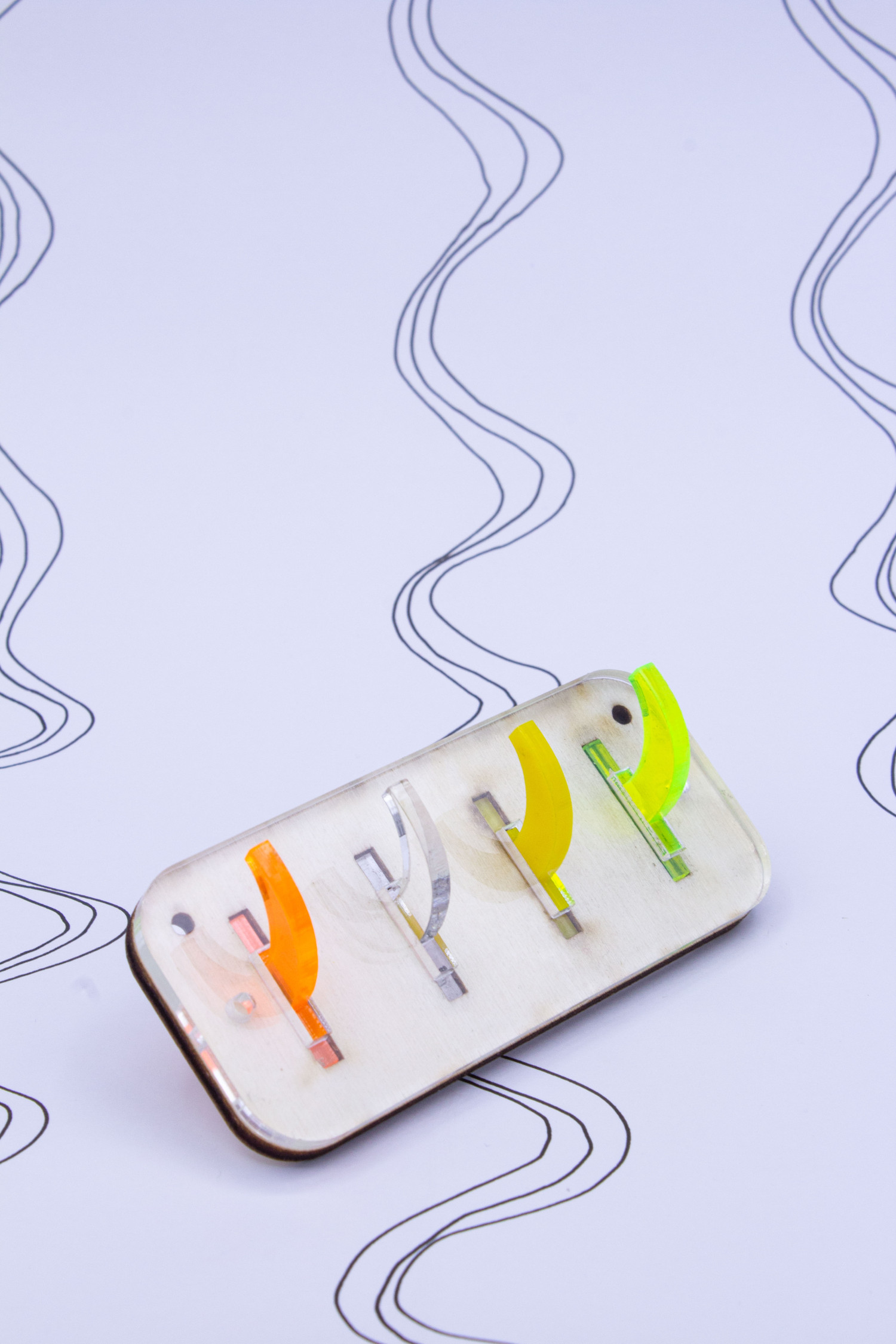
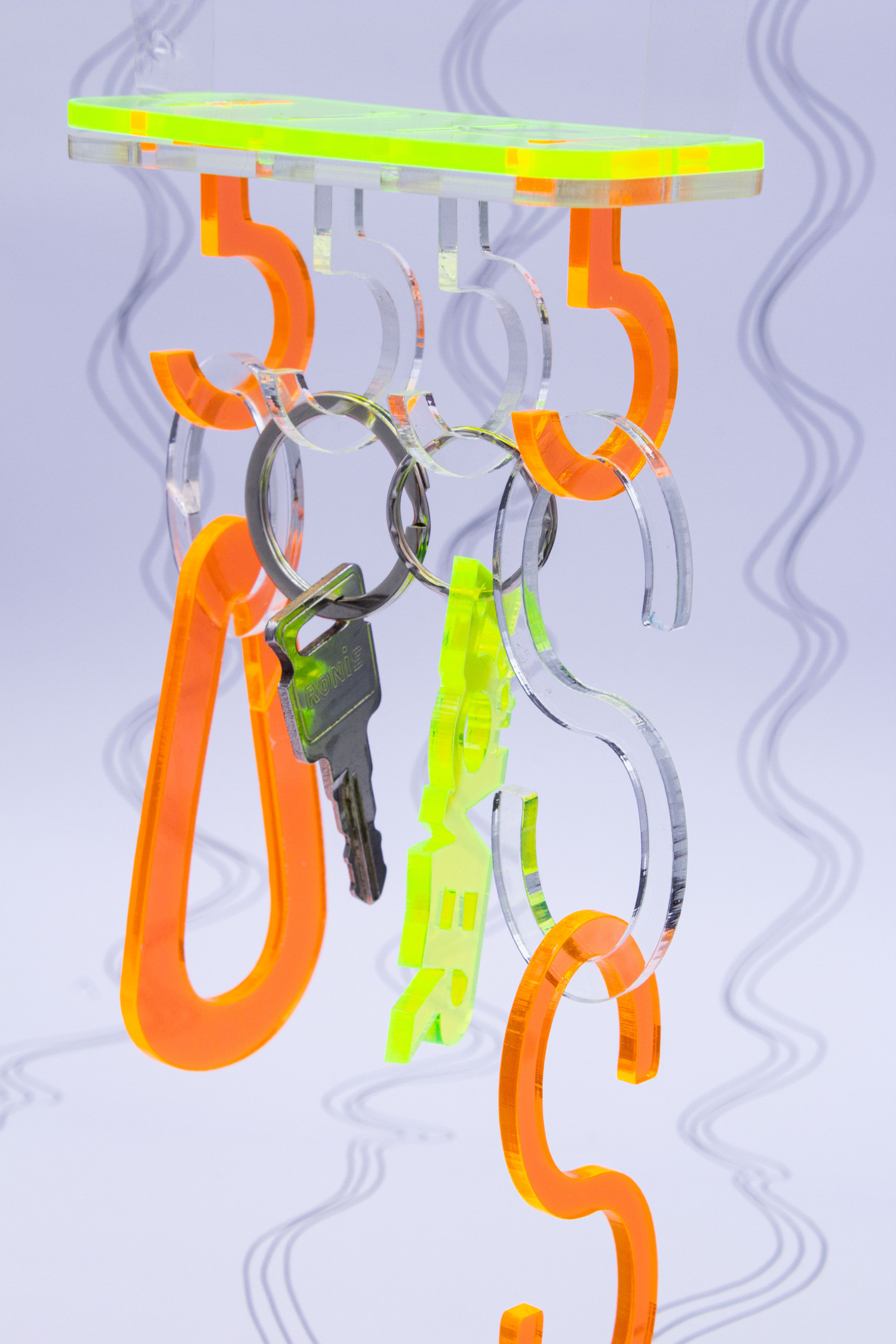
WEBEN MIT JOHANN - GUNDULA HICKISCH
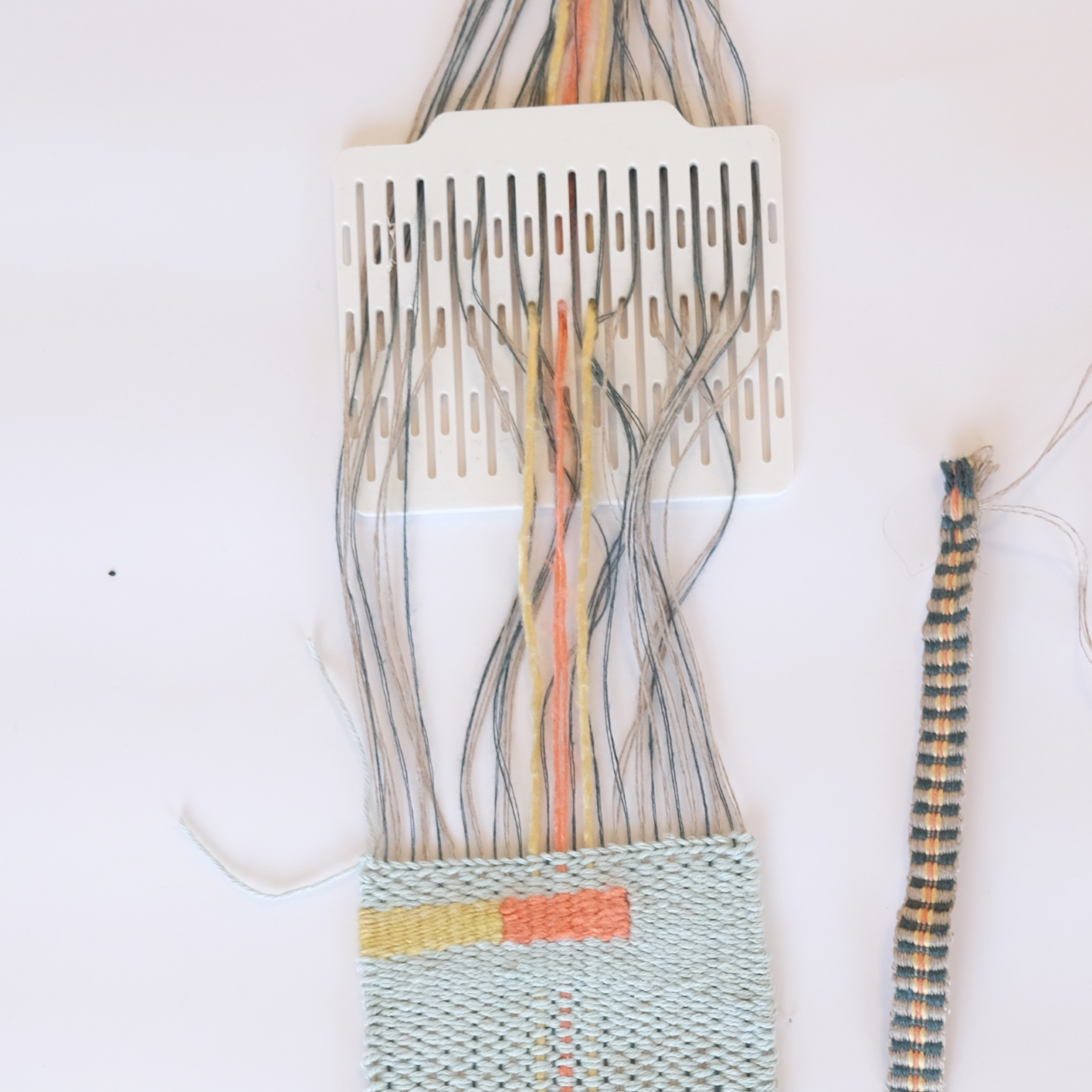
Wer sagt, dass Weben nur mit einem großen Webstuhl möglich ist? Mit dem Webkamm Johann können Bänder, Stoff-Fragmente und Miniatur-Bilder entstehen. Ziel von Gundula war es, ein schönes und simples Webgerät zu entwickeln. So arbeitete sie in der Residency an ihrem Webkamm Johann.
Das Ergebnis: Die nächste Generation Johann wird per 3D- Druck hergestellt. Mit dem Lasercutter wäre seine Herstellung zwar sehr schnell möglich, allerdings werden die Kanten des Kamms dabei sehr scharf und er ist weniger stabil. Daher hat sich Gundula für den 3D-Druck entschieden und sich vor allem mit dem 3D-Zeichenprogramm Fusion 360 beschäftigt, um Johann im Detail so anzufertigen, wie sie ihn sich vorstellt.
„Die Möglichkeit, mit Maschinen zu arbeiten, die es sonst nur in speziellen Werkstätten oder Industriebetrieben gibt, ist ein Luxus – dafür bin ich sehr dankbar. Es werden Arbeitsabläufe realisierbar, die ohne die Geräte und die kompetente Unterstützung des Happylab-Teams für mich nicht vorstellbar gewesen wären.“
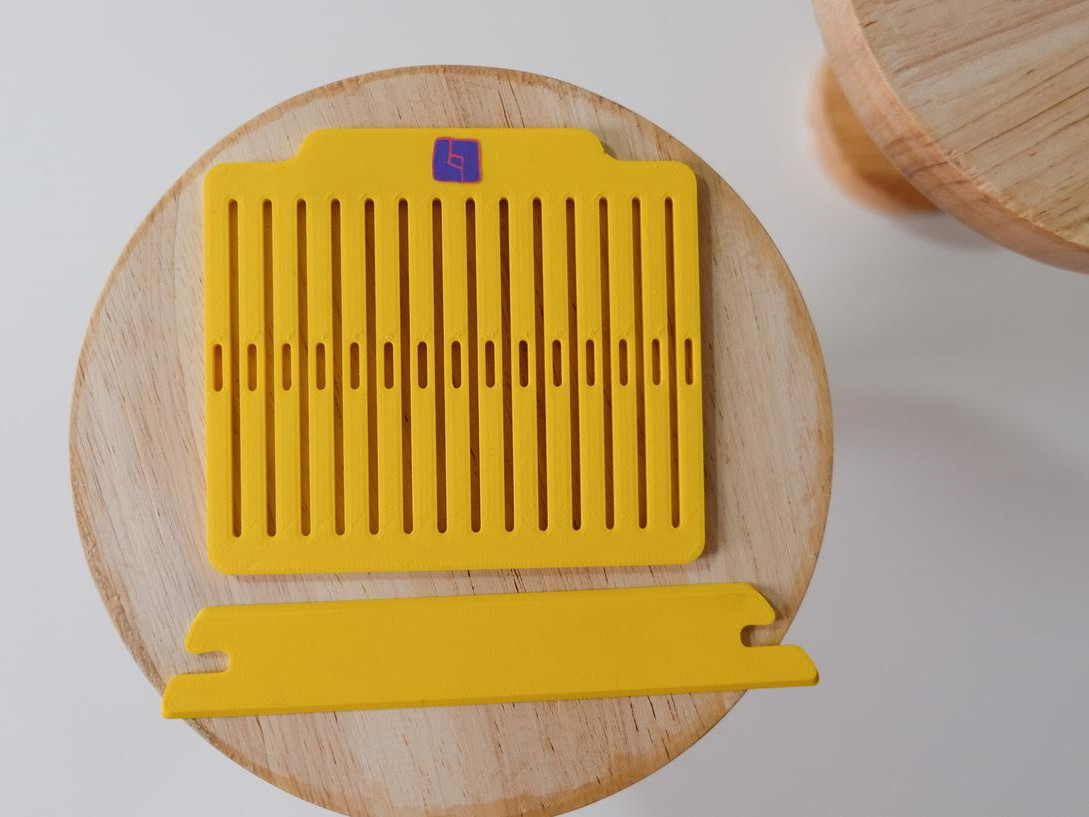
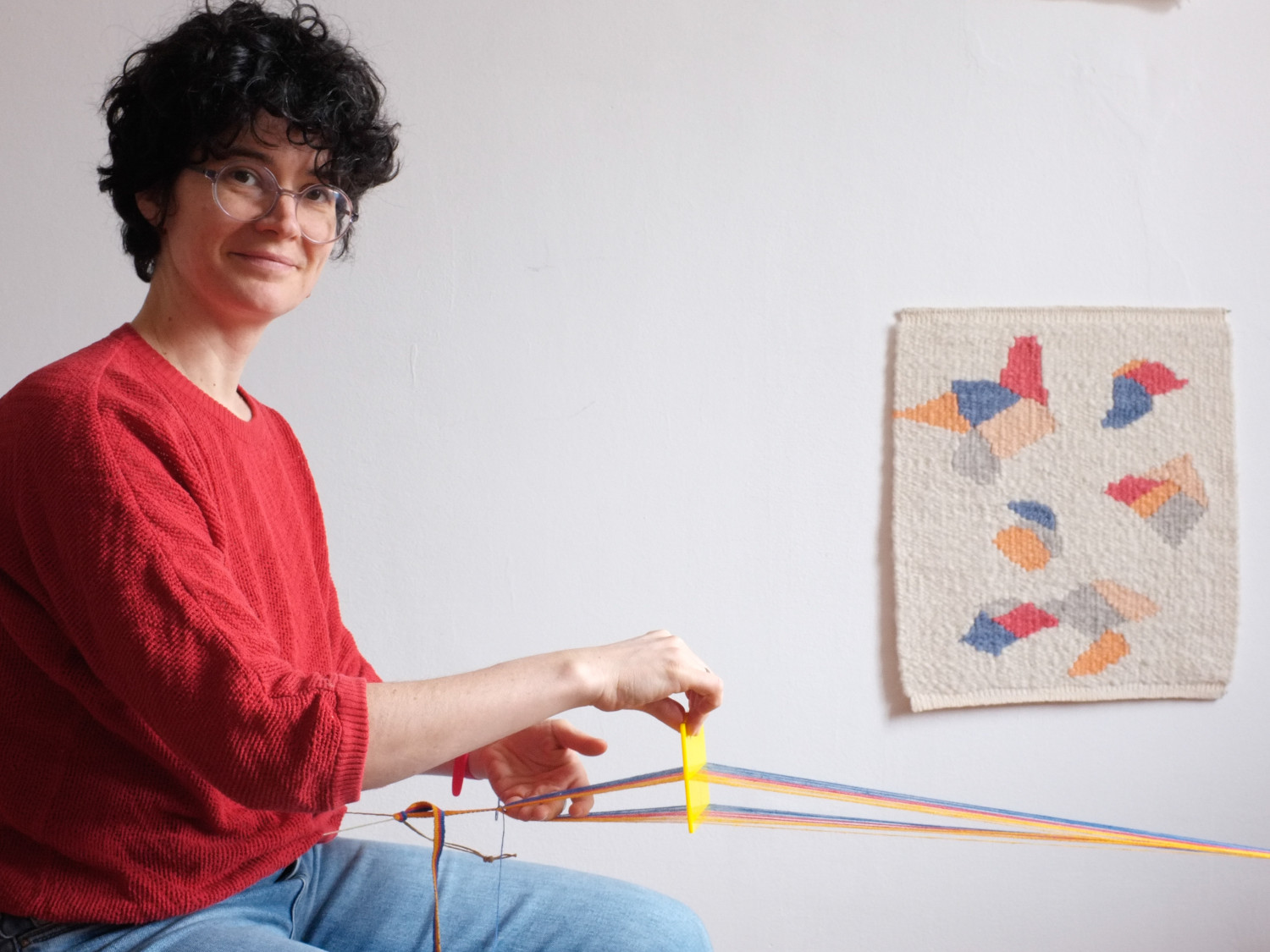
EEVI GARDENS - HANS-HENNING BÖRSTINGER & VIPUL KHATANA
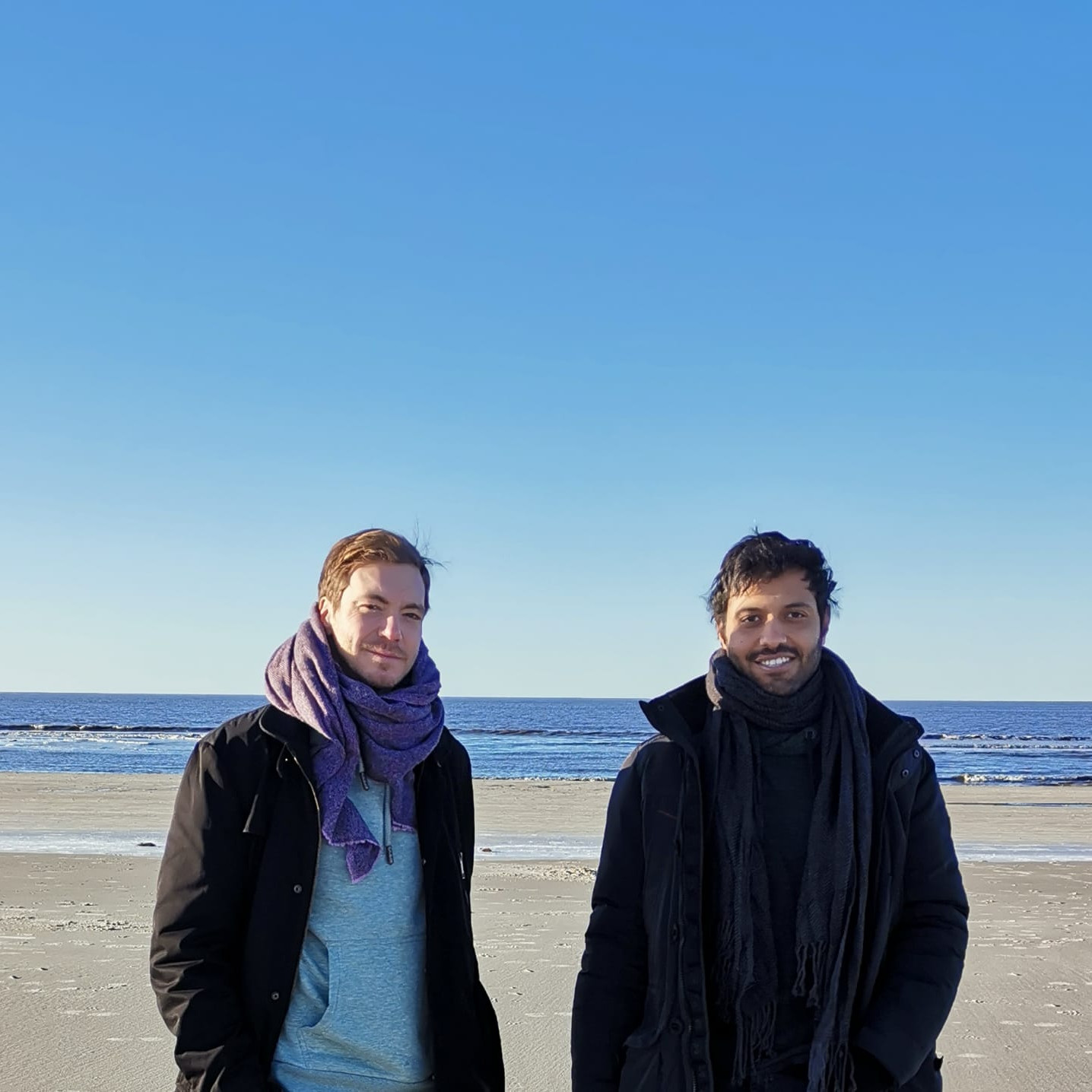
Hans-Henning und Vipul machen mit Eevi Gardens eine Vielzahl regionaler und exotischer Lieblingsaromen zugänglich und umsetzbar.Stellt euch eine Stehlampe vor, die passive Beleuchtung für die Wohnung liefert und dabei die Schönheit der Pflanzen ins Rampenlicht stellt und durch Tageslichtqualität das Wohlbefinden der Pflanzen und Bewohner*innen sicherstellt. – das ist Eevi. Durch automatisierte Bewässerungszyklen muss man sich bis zu 3 Wochen keine Gedanken um die Pflege machen. Die Umsetzung dieses Projektes war für die beiden eine Herzenssache.
Bei der Auswahl der Materialien und der Arbeitsprozesse haben sie auf höchste Standards und Qualität geachtet. Um Lebensmittel- und Nutzersicherheit mit Bedienungsfreundlichkeit in einem nachhaltigen Produkt zu verbinden, haben sie mit verschiedensten Materialen – und damit auch Maschinen – experimentiert. Vor allem die 3D-Drucker und knapp 800 Stunden mit Fusion sorgten dafür, dass das Design nicht nur eine Idee im Kopf blieb, sondern am Ende als Eevi vor ihnen stand.
„Die Distributed Design Residency hat das Thema Kreislaufwirtschaft, Nachhaltigkeit und Logistik ins Zentrum der Gestaltung unserer Entwicklung und Arbeitsprozesse gerückt. Einer der Leitsätze des distributed design in Eigeninterpretation "let the design file travel, not the product" hat sich tief in unserer Arbeit verwurzelt. Die Fertigung in der Region des Kunden hat sich zu einem zentralen Element in unserem Business Model entwickelt und wurde schon im Rahmen des Herstellungsprozesses eingeplant. Durch die Vielzahl der benötigten industriellen Maschinen und dessen Bereitstellung hat das Happylab die professionelle Umsetzung überhaupt erst ökonomisch realisierbar werden lassen. Wir kennen keinen anderen Ort als das Happylab, der uns das in diesem Rahmen in Zentrumsnähe ermöglicht – vom Konzept über die Fertigung bis hin zum Finishing.“
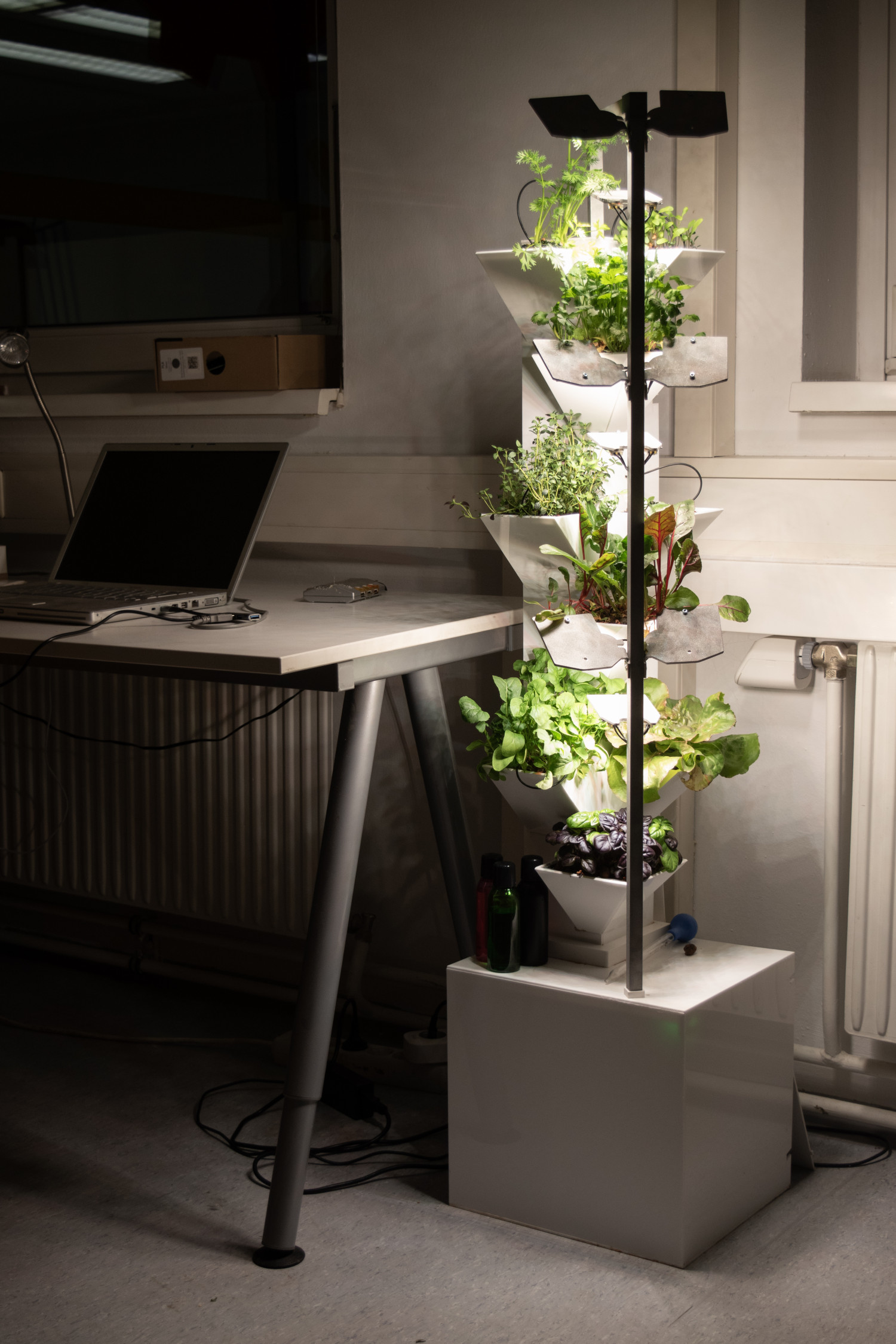
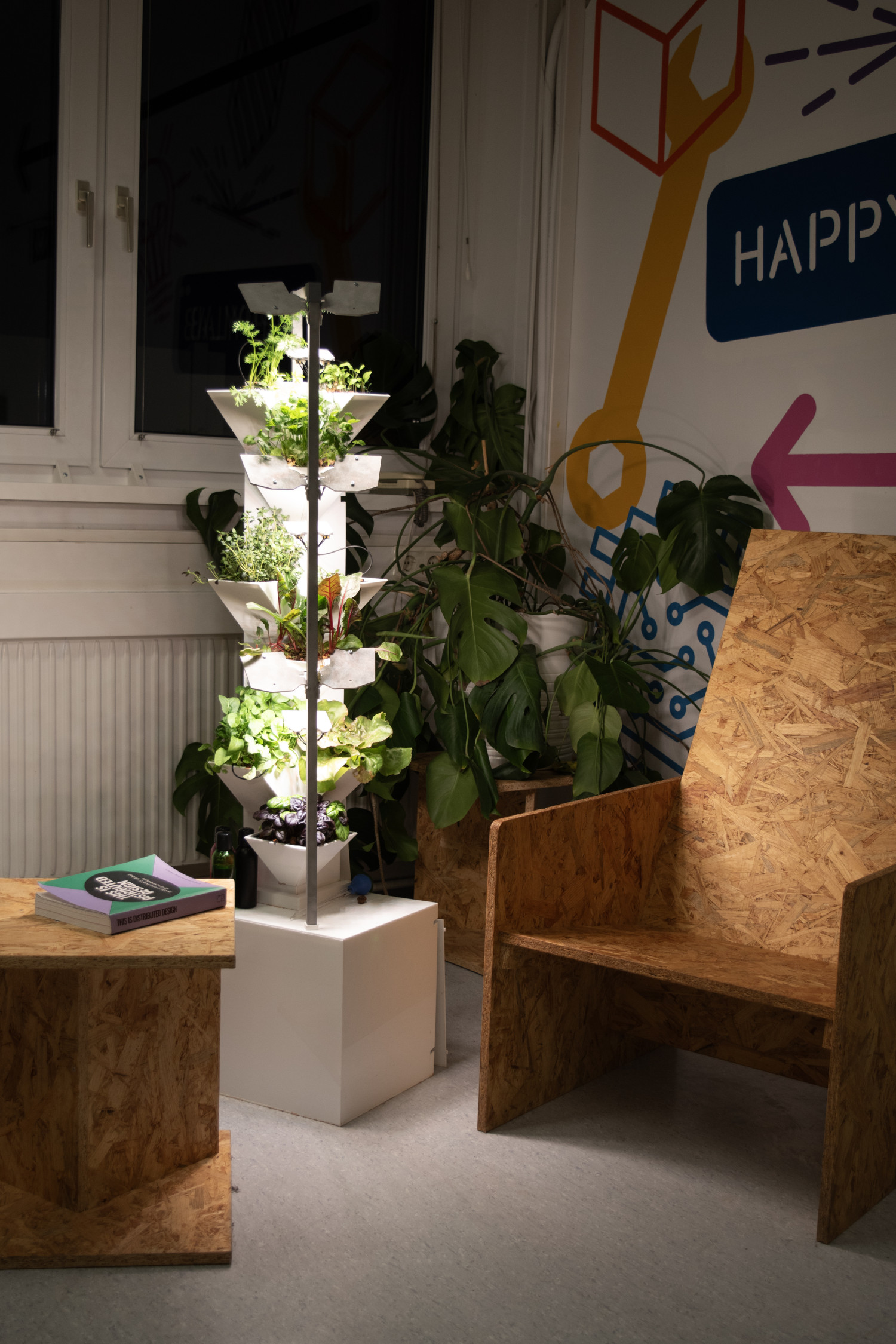
DESIGN BRAIDED TEXTILES - KATHARINA HALUSA
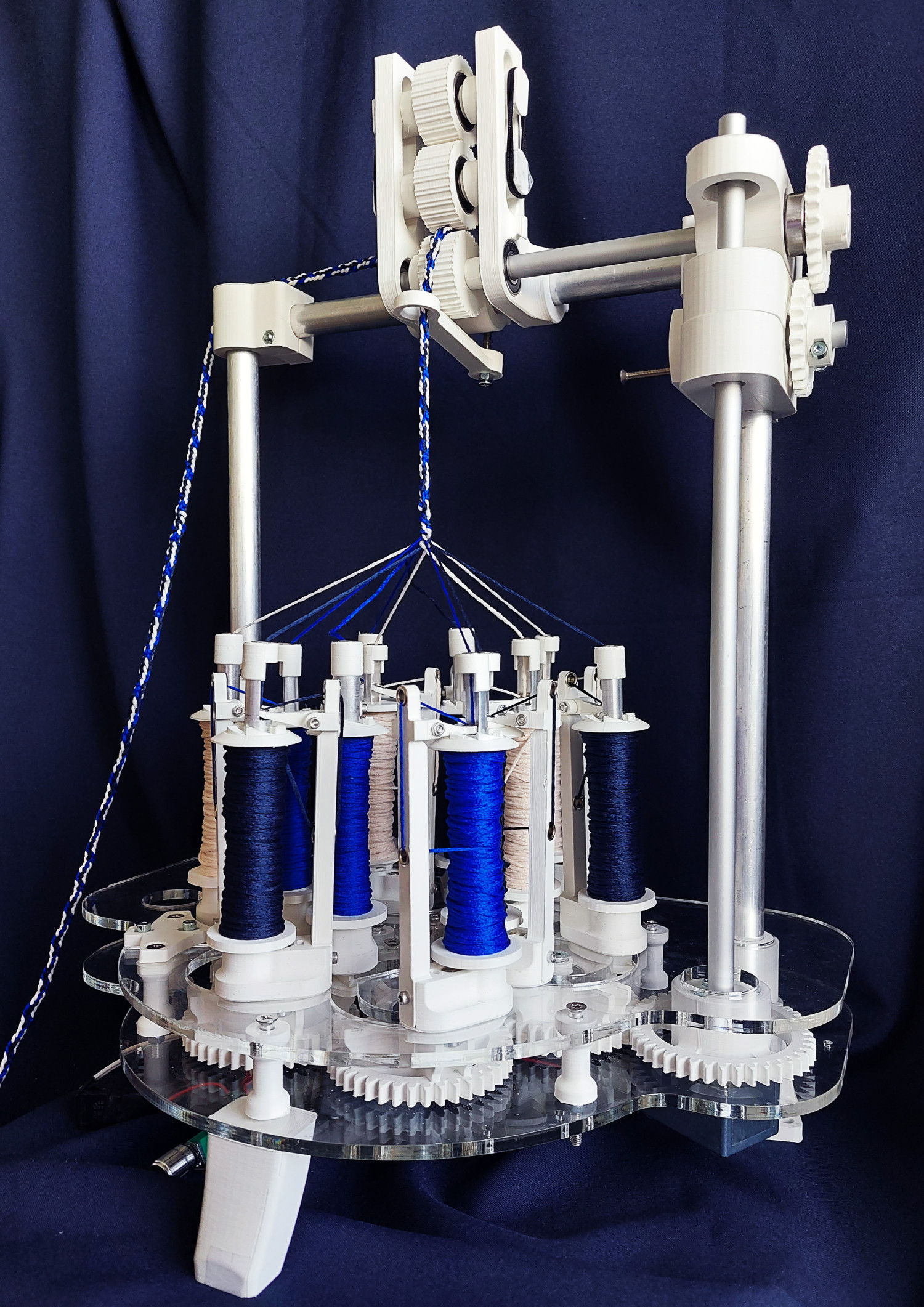
In Katharinas Masterprojekt BRAIDED TEXTILES in Fashion&Technology an der Kunstuniversität Linz wurden textile Geflechte an einer Radialflechtmaschine hergestellt.
In der Residency hat sie nun eine Flechtmaschine in kleinerem Maßstab gefertigt, die es ermöglicht, textile Geflechte zu kreieren und mit unterschiedlichen Garnmaterialien zu experimentieren. Basierend auf der DIY 3D Printed Braiding Machine von Fraens werden unterschiedliche textile Fasern (nachhaltige Natur-u. Synthetikfasern sowie Biomaterialien) herangezogen. Diese Geflechte könnten als Accessoires (wie z.B. Armbänder oder Ketten) und in der Bekleidung Anwendung finden.
Im Happylab hat sie hauptsächlich den 3D-Drucker benutzt, um die einzelnen Komponenten für die Flechtmaschine herzustellen. Weit über 100 Einzelteile wurden damit gedruckt. Weiters war der Lasercutter im Einsatz, um die Basisplatten für den Flechtprozess zu schneiden. Auch den Happylab Shop fand sie sehr praktisch, um direkt die benötigten Schrauben und anderes Zubehör zu erwerben. Nachdem alle Einzelteile gefertigt wurden, konnte der Zusammenbau beginnen.
„Das Happylab hat mir mit dem Angebot der Beratungsstunden total weitergeholfen. Da ich selbst keinen technischen Background habe, fielen mir manche Handgriffe beim Zusammenbau bzw. bei der Vorbereitung der Einzelteile schwer. In den Beratungsstunden wurden mir innerhalb kürzester Zeit Lösungsvorschläge für mein Vorhaben/Problem dargelegt und gezeigt. Der Lernprozess war enorm. Auch der Austausch mit den anderen Teilnehmer*innen war toll, um neue Sichtweisen auf das eigene Projekt zu bekommen.“
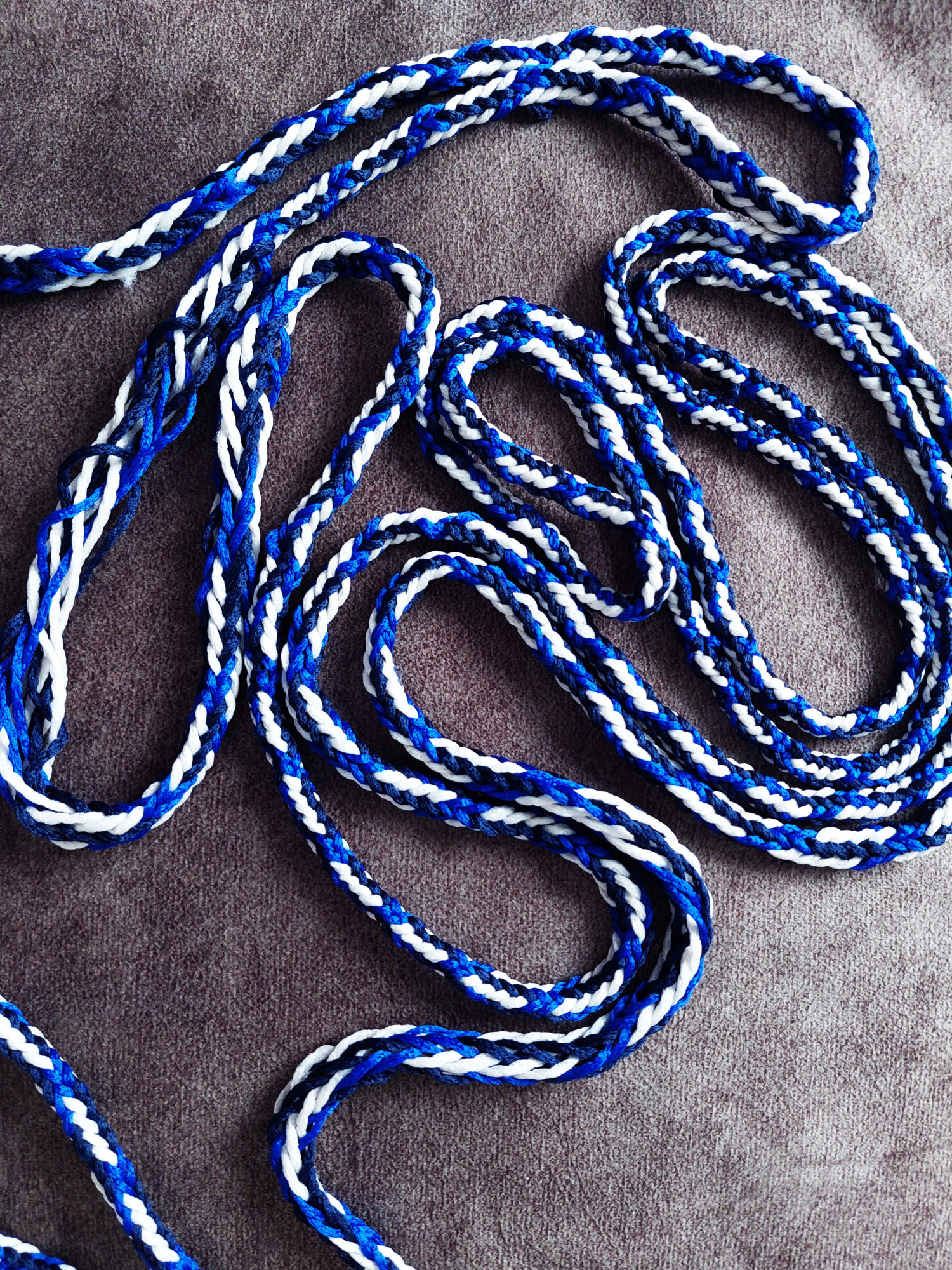
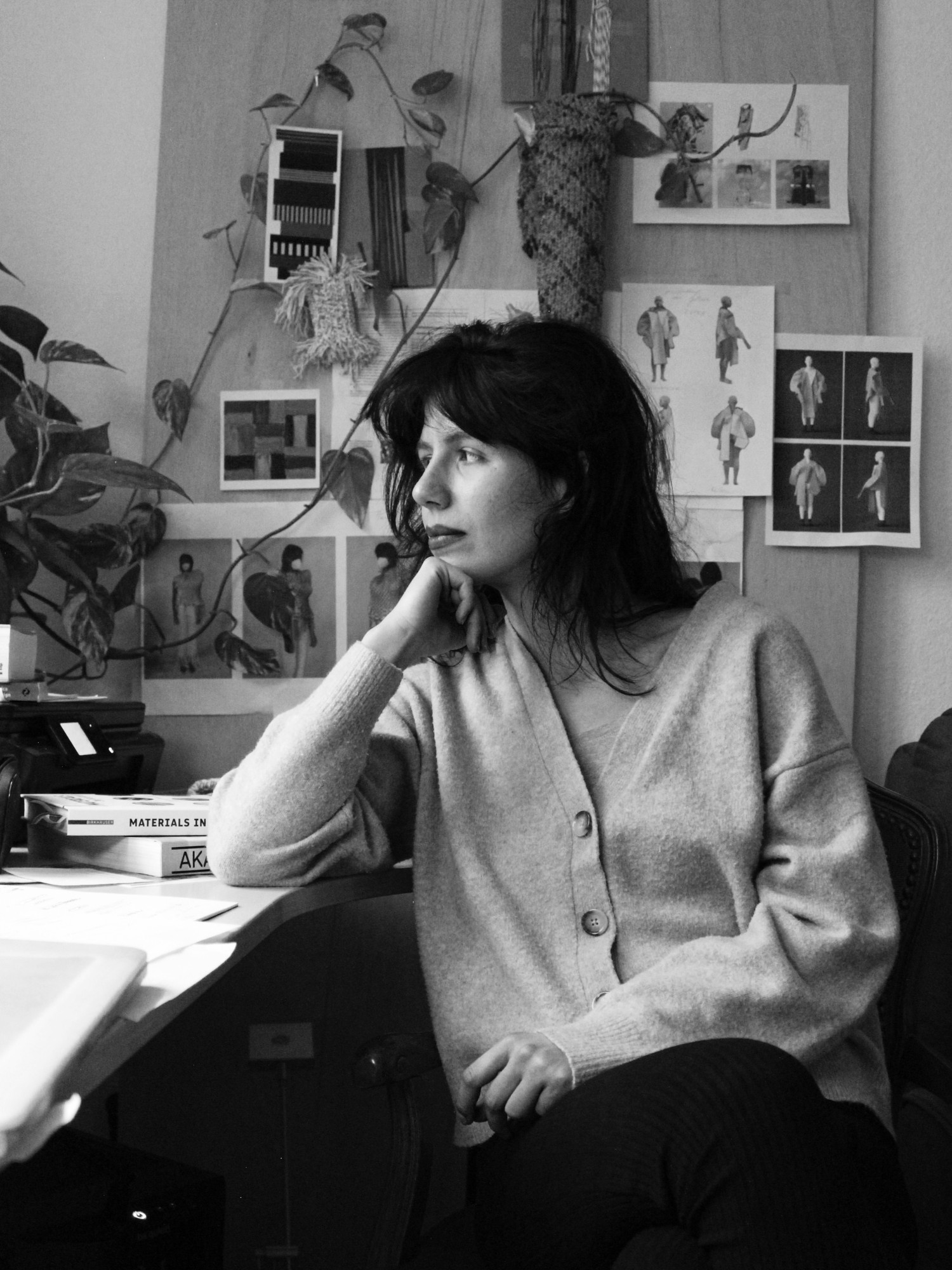
REPLIFACTORY - CATALIN RUSNAC
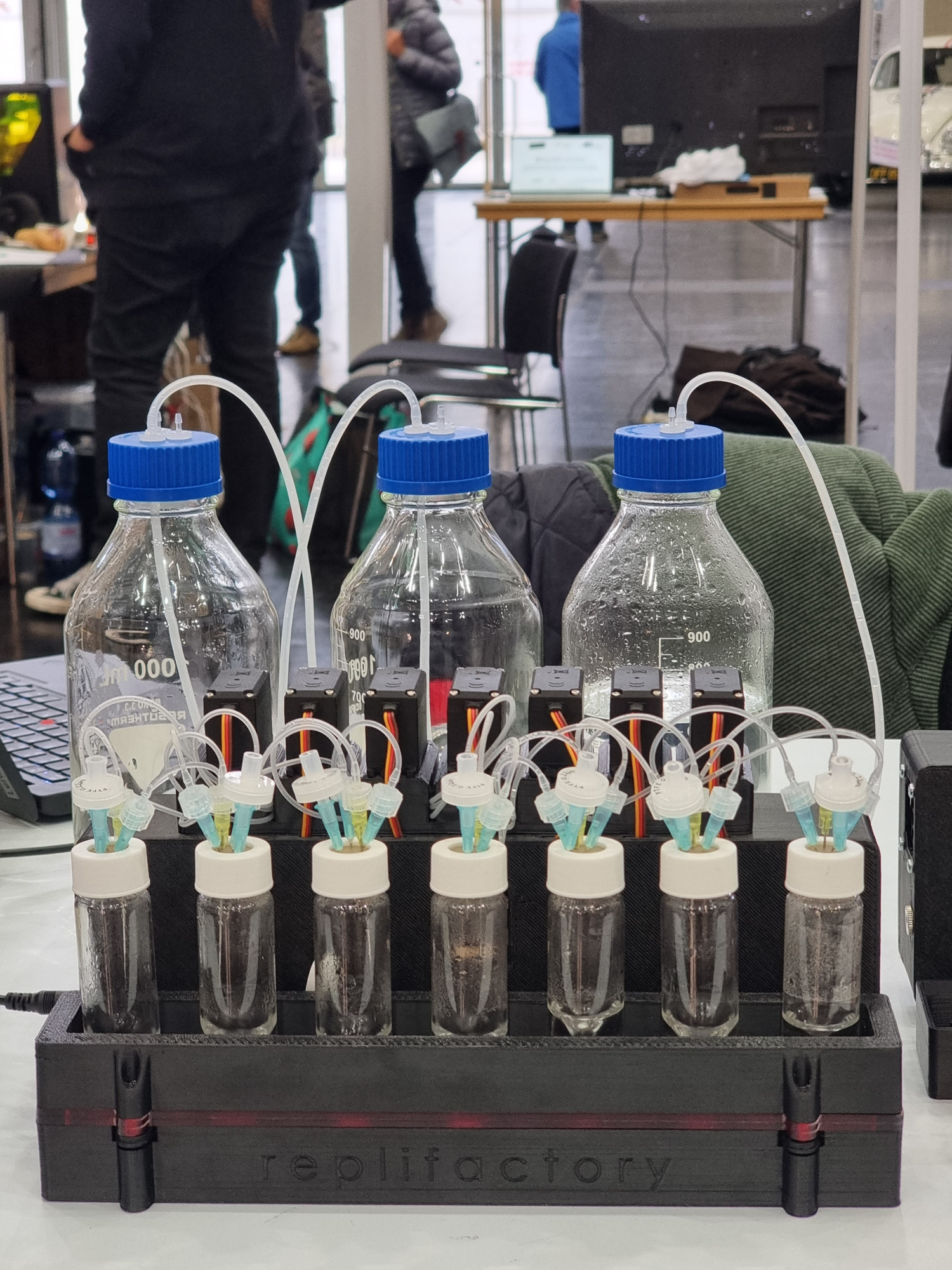
Catalin hat mit replifactory ein 3D-gedrucktes Laborgerät für die Anzucht von Bakterien entworfen. Es ermöglicht die Durchführung einer Vielzahl typischer biologischer Experimente – unter anderem wie ein Morbidostat (Konstanthaltung des Stressniveaus für die Kultur, um sie an eine Belastung – wie Antibiotika oder Metalle – anzupassen). Ein Morbidostat ist ein sehr kompliziertes Laborgerät, das von einem Techniker bedient und gewartet werden muss, da die bestehenden Konstruktionen nicht optimiert wurden.
Catalin hat eine Version entworfen, die kompakt, leicht zu reinigen und kostengünstig zu bauen ist, und diese in den vergangenen Monaten weiterentwickelt. Herausgekommen ist ein experimentelles Evolutionssystem – quasi ein "Fitnesstrainer für Bakterien“
Catalin hat im Happylab die Elektronikwerkstatt zum Löten von Leiterplatten, den (Metall-) Laser Cutter und die CNC-Maschinen zur Entwicklung von Bauteilen und Vorrichtungen für die Montage benutzt.
“Die Distributed Design Residency half mir bei der Entwicklung meines Projekts, indem sie mich mit einer Gemeinschaft begeisterter Gleichgesinnter verband. Ich hatte anregende Diskussionen mit anderen Makern und Experten aus verschiedenen Bereichen, die im Happylab zusammenkommen.“
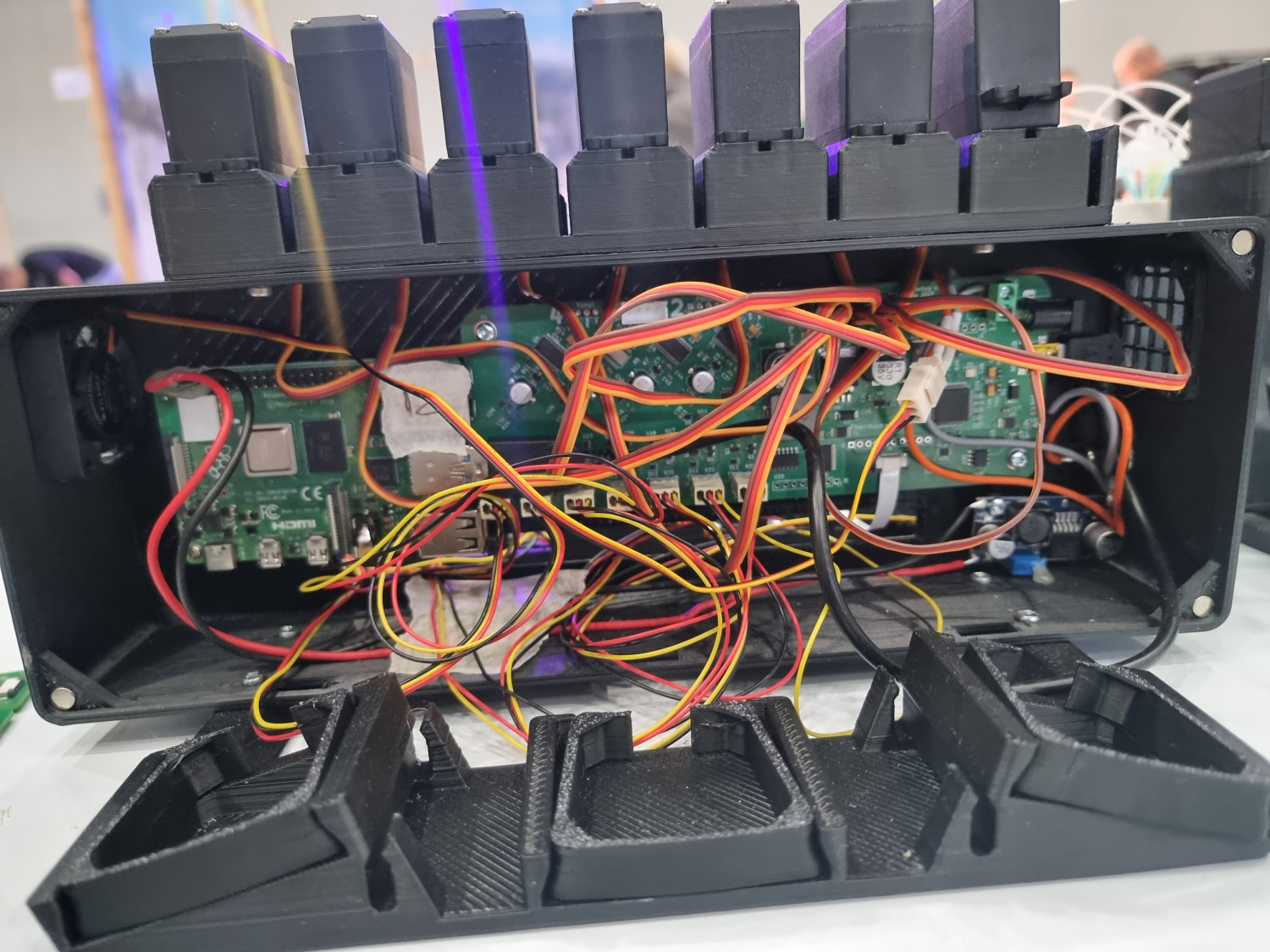
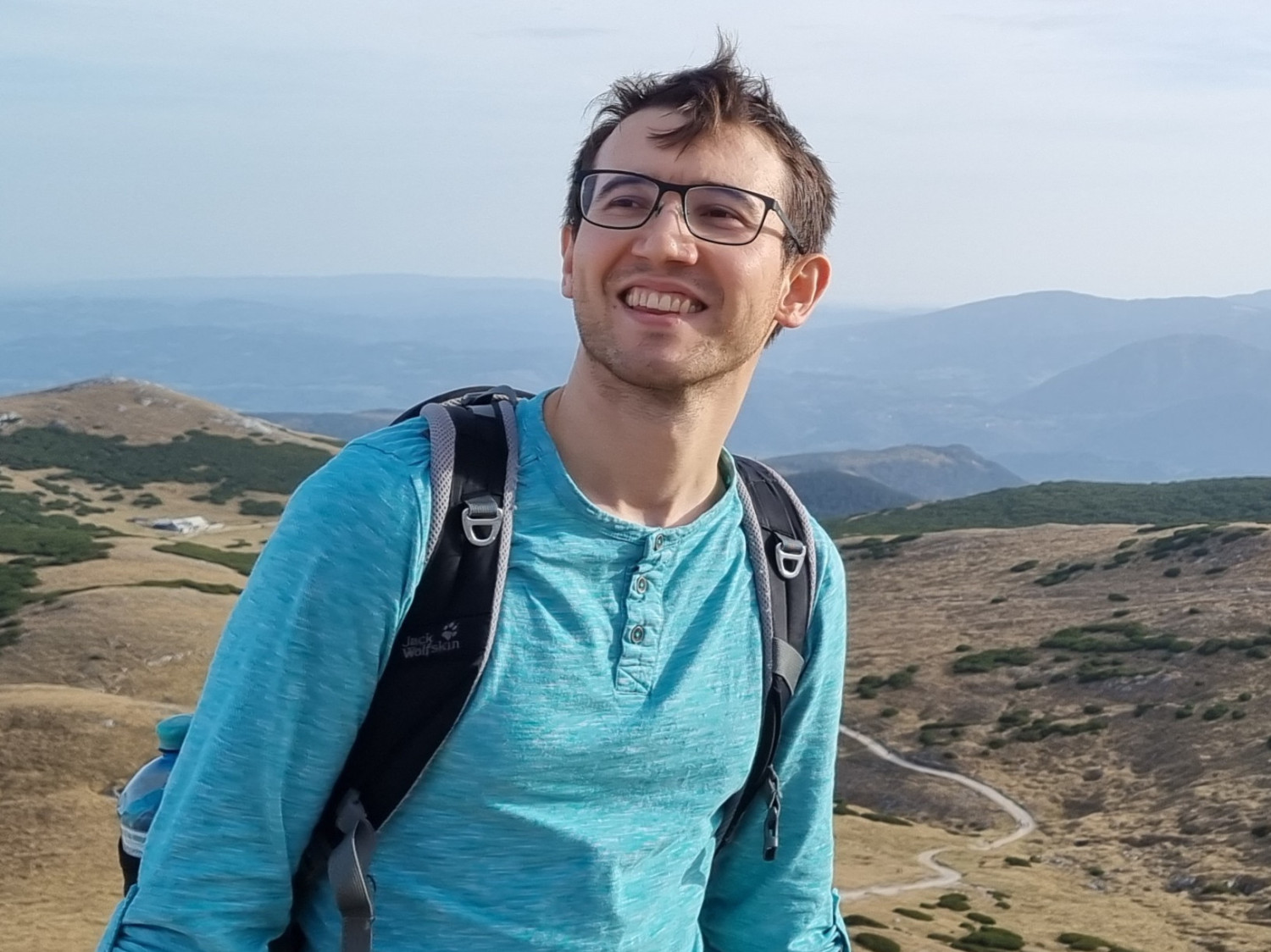