We are delighted to present the final projects of the Distributed Design Residency 2023/24. For six months - from September 2023 to February 2024 - we supported makers and designers in the realization of their projects at Happylab. The results are impressive projects that you can see in our makerspace throughout March 2024. So feel free to drop by!
And for anyone interested in taking part in the Distributed Design Residency themselves, we have good news: Together with the Distributed Design Platform, Happylab is once again supporting creative talent this year. The new round will start in September 2024! The Open Call is already online and runs until June 16, 2024, we look forward to your applications!
HANDMADE MASSPRODUCTION - MARIIA SAMAHALA & MYKHAILO ZHUK
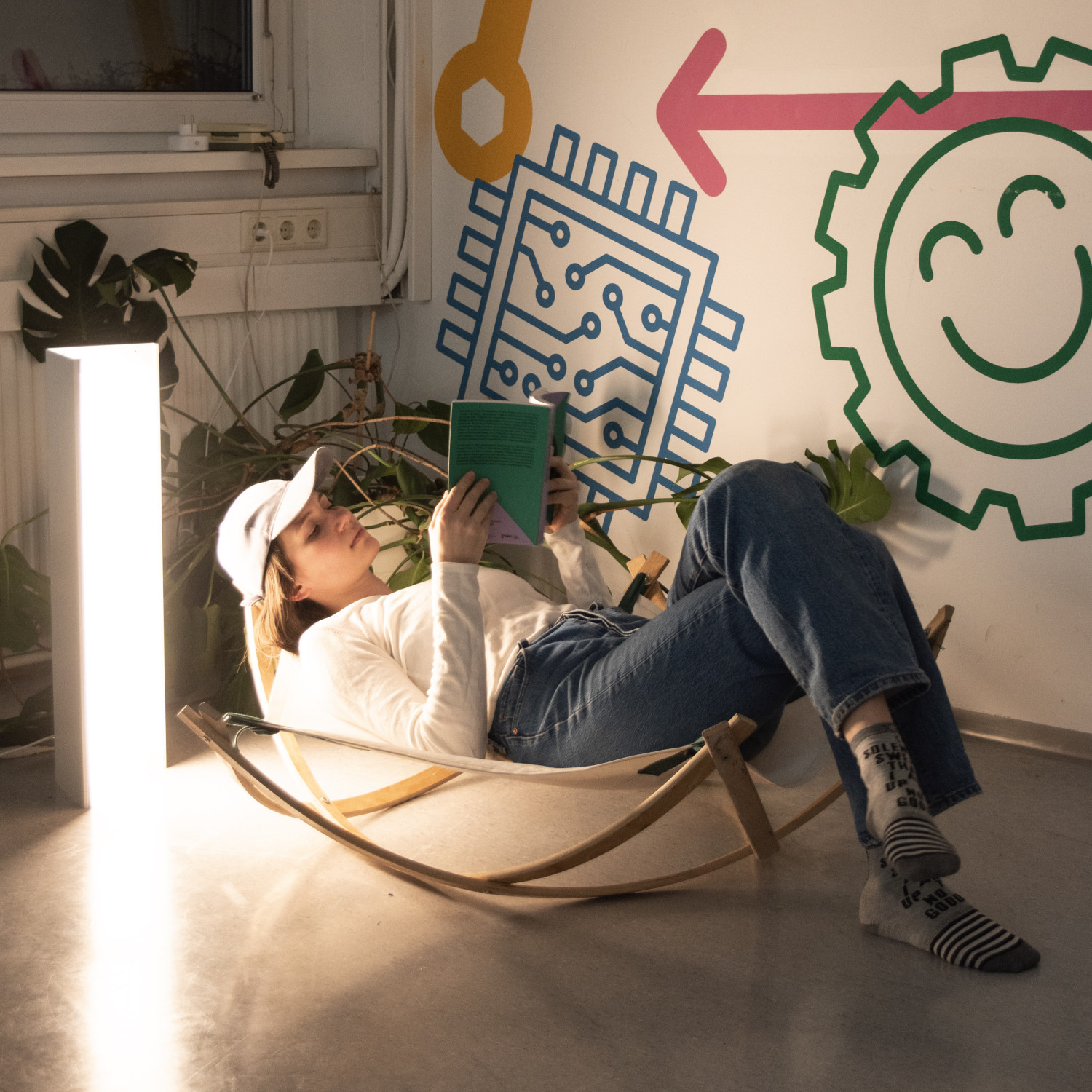
Mariia and Mykhailo believe that minimizing waste is one of the main ways designers can reduce the environmental impact of their products. They wanted to rethink the materials they work with. As part of the Distributed Design Residency, they tested a design principle that aims to use prefabricated objects as material to build new designs. This has resulted in a chair and a lamp made from reused parts. The chair is made from old slatted frame bars that have been steam-bent and put under tension. For the lamp body, the two used an aluminum profile found in a scrap yard.
Another experiment focused on the waste produced in the Happylab. They used the sawdust from the wood workshop as a basis for the growth of mycelium material, which the designers would like to work with more intensively in the future.
"In the last 6 months, we experimented with many new techniques and expanded our skillset thanks to the residency. We were most excited about the exchange program, which allowed us to get to know successful makers and designers with values very close to our own. The project-oriented format also helps to structure and evaluate the work processes."
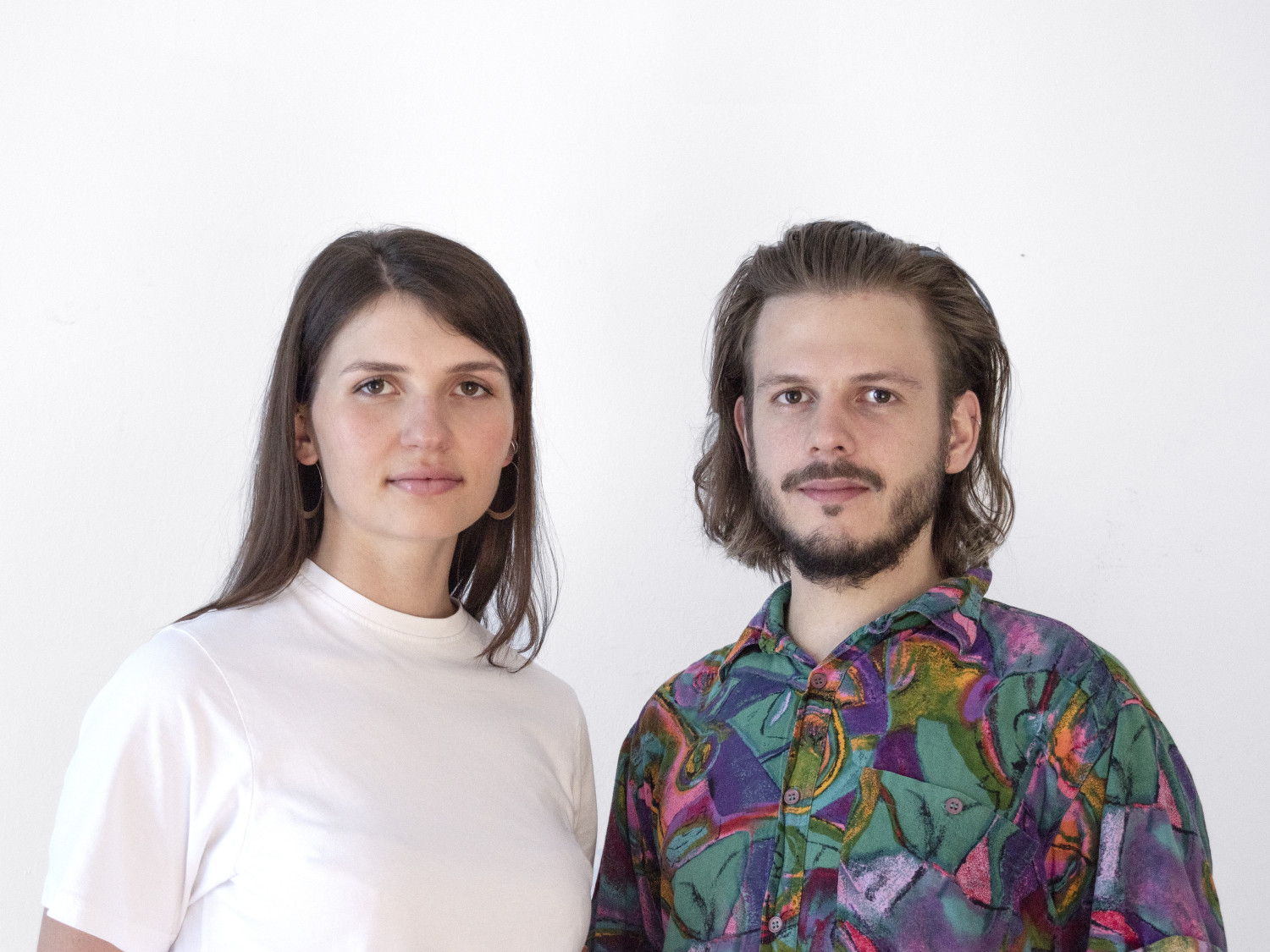
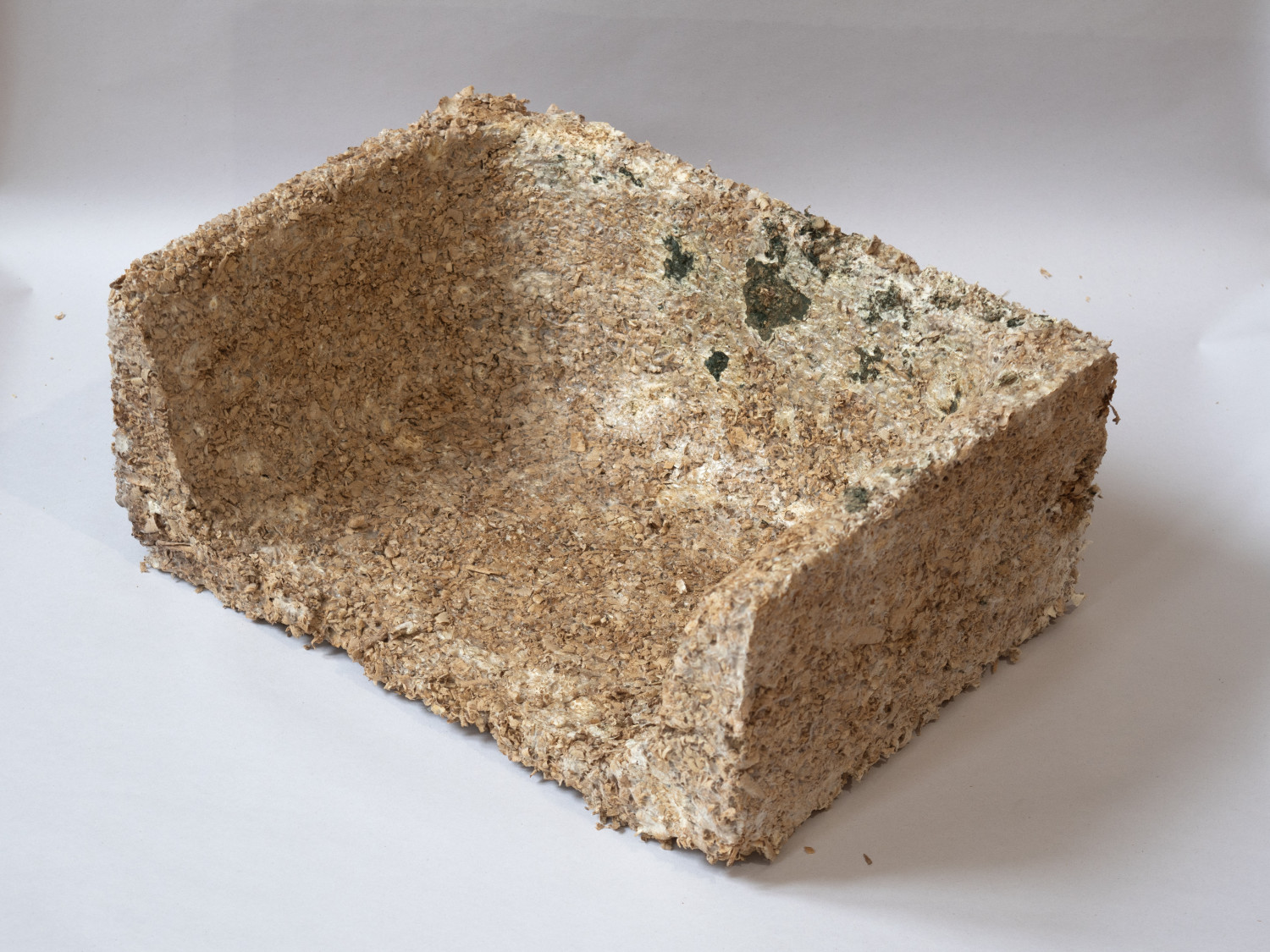
L(EFT)OVERS - NINA MCNAB
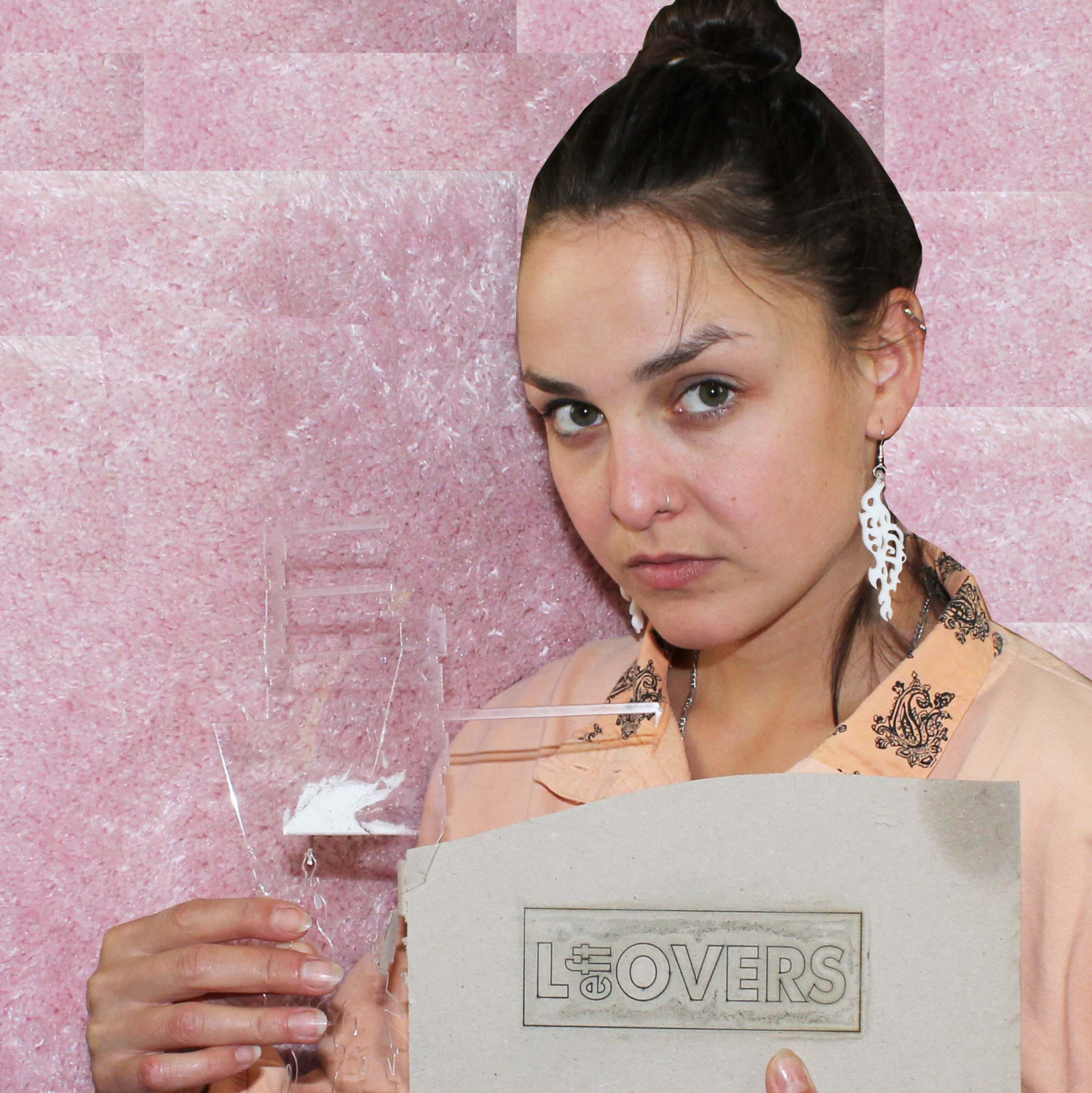
L(eft)OVERS is a free database of vectors that fill the spaces between laser files. This reduces waste production and conserves resources. The vectors - small practical, cute or playful objects - are intended to show the potential of supposed leftovers and encourage people to develop and share their own designs.
Nina spent several days a week at Happylab, where she primarily used the laser cutter. She particularly enjoyed the input and exchange from and with other members and residents in the lab and co-working space.
"Through the residency, I was able to consolidate existing skills in digital production practice and raise them to an experienced level, which not only enabled efficient production. The deeper, practical understanding allowed me to open up a new area of use for digital production machines in my creative approach, which is already being applied in my artistic practice. The personal and close supervision of our projects also resulted in motivated work and a sense of belonging not only to the Happylab community, but also to the entire designer and maker scene."
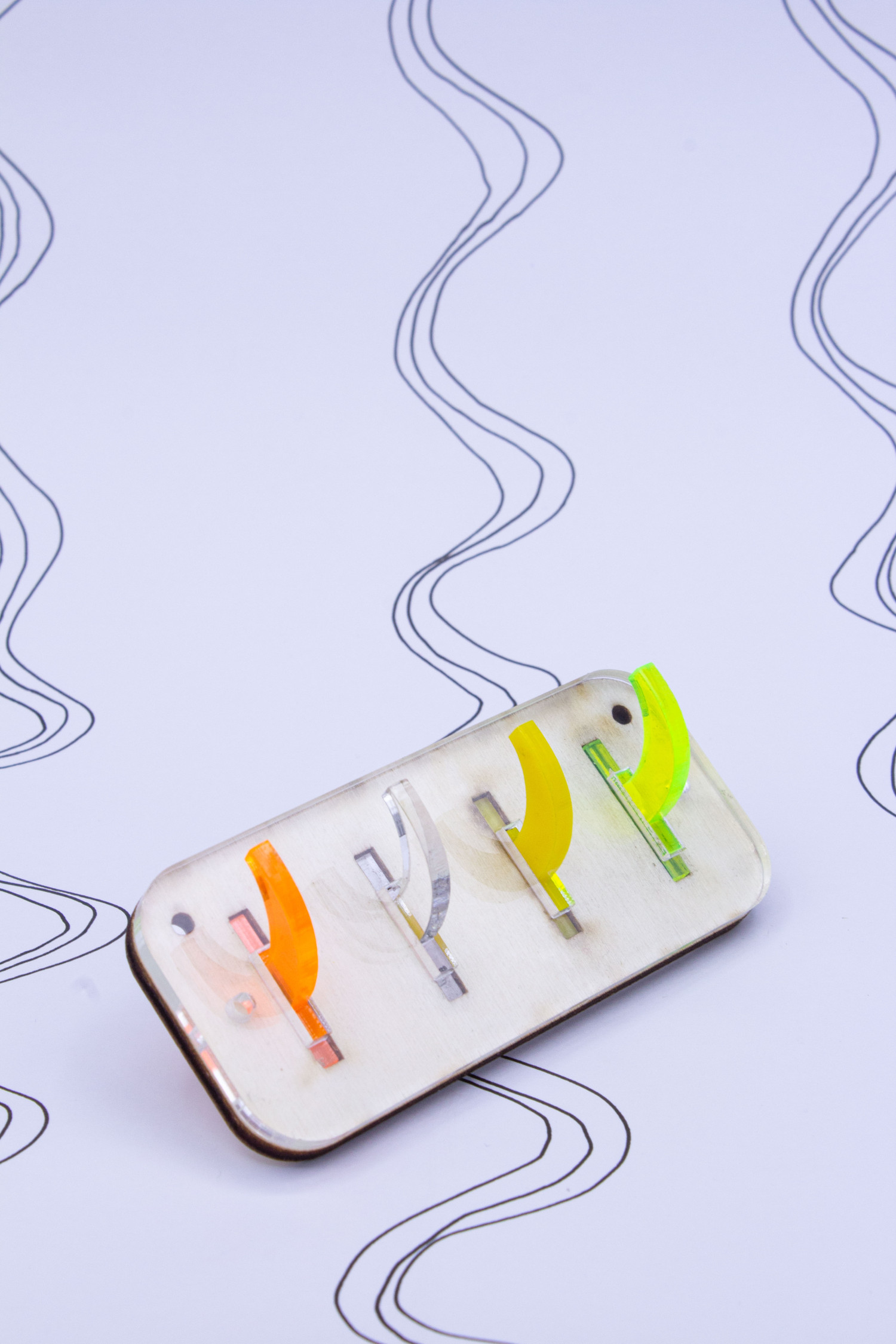
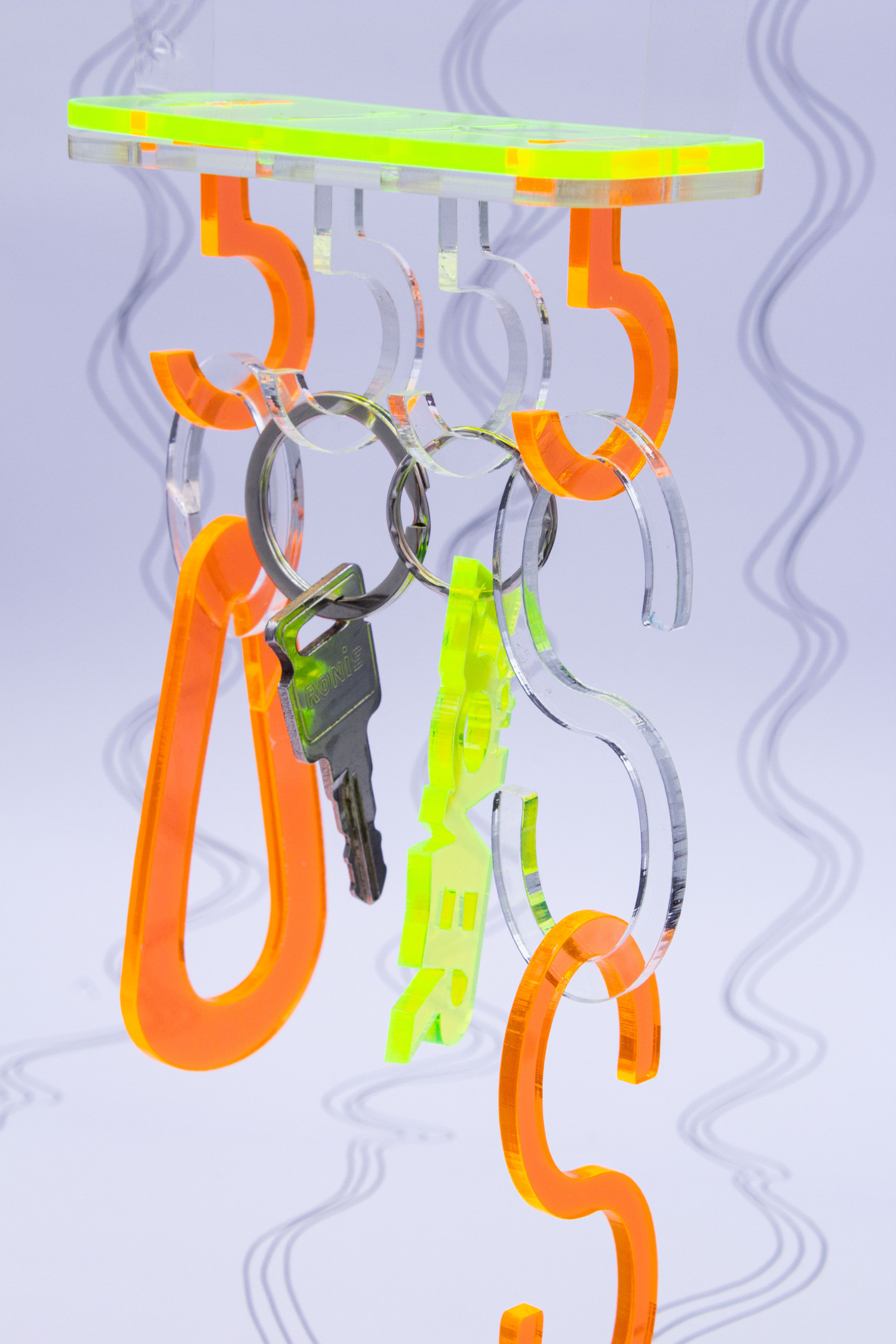
WEAVING WITH JOHANN - GUNDULA HICKISCH
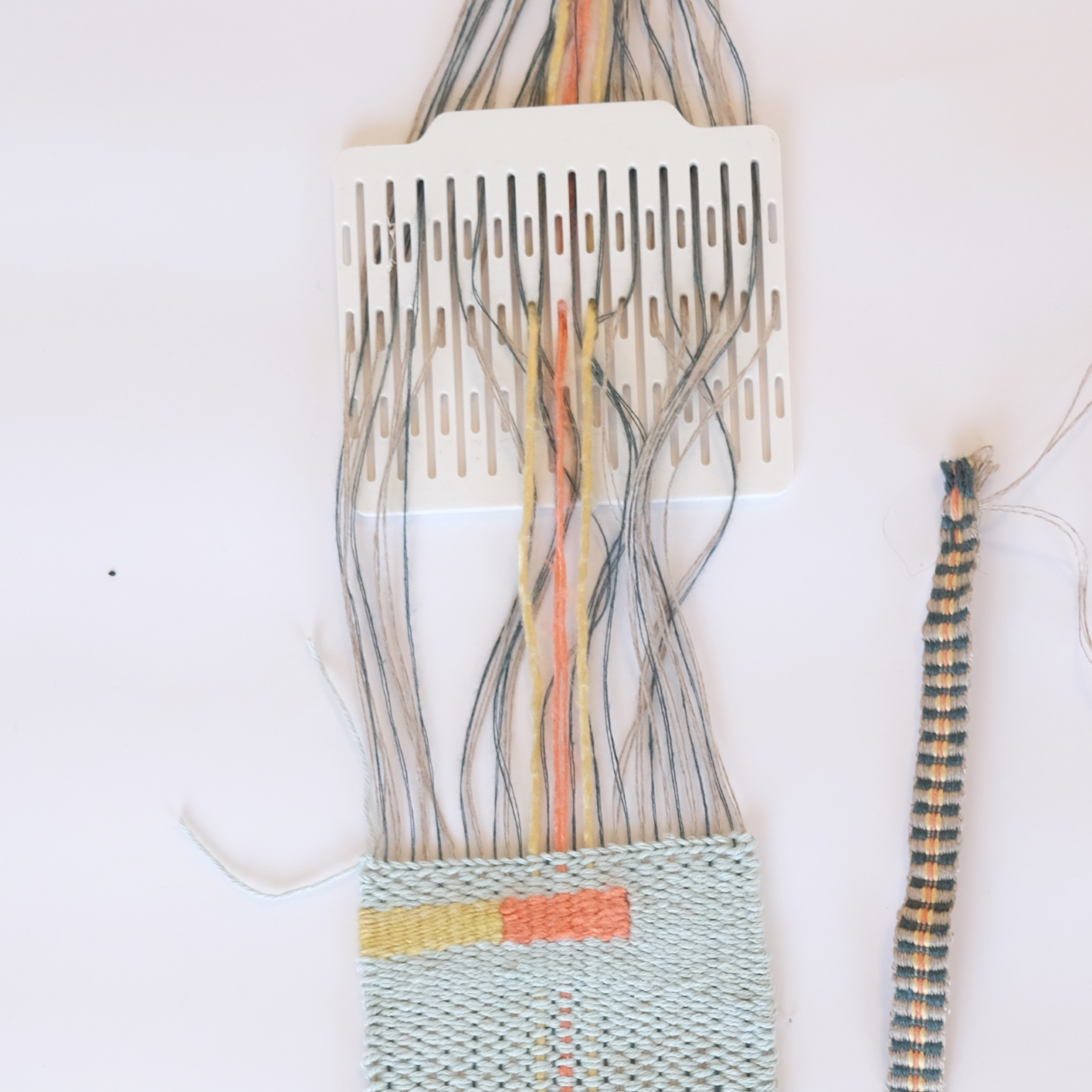
Who says that weaving is only possible with a large loom? The Johann weaving comb can be used to create ribbons, fabric fragments and miniature pictures. Gundula's aim was to develop a beautiful and simple weaving device. So she worked on her Johann weaving comb during the residency.
The result: the next generation Johann is produced using 3D printing. Although it could be produced very quickly using a laser cutter, the edges of the comb become very sharp and it is less stable. Gundula therefore opted for 3D printing and worked primarily with the 3D drawing program Fusion 360 to produce Johann in detail as she imagined him.
"The opportunity to work with machines that are otherwise only available in special workshops or industrial companies is a luxury - I'm very grateful for that. It makes work processes possible that would have been unimaginable for me without the equipment and the expert support of the Happylab team."
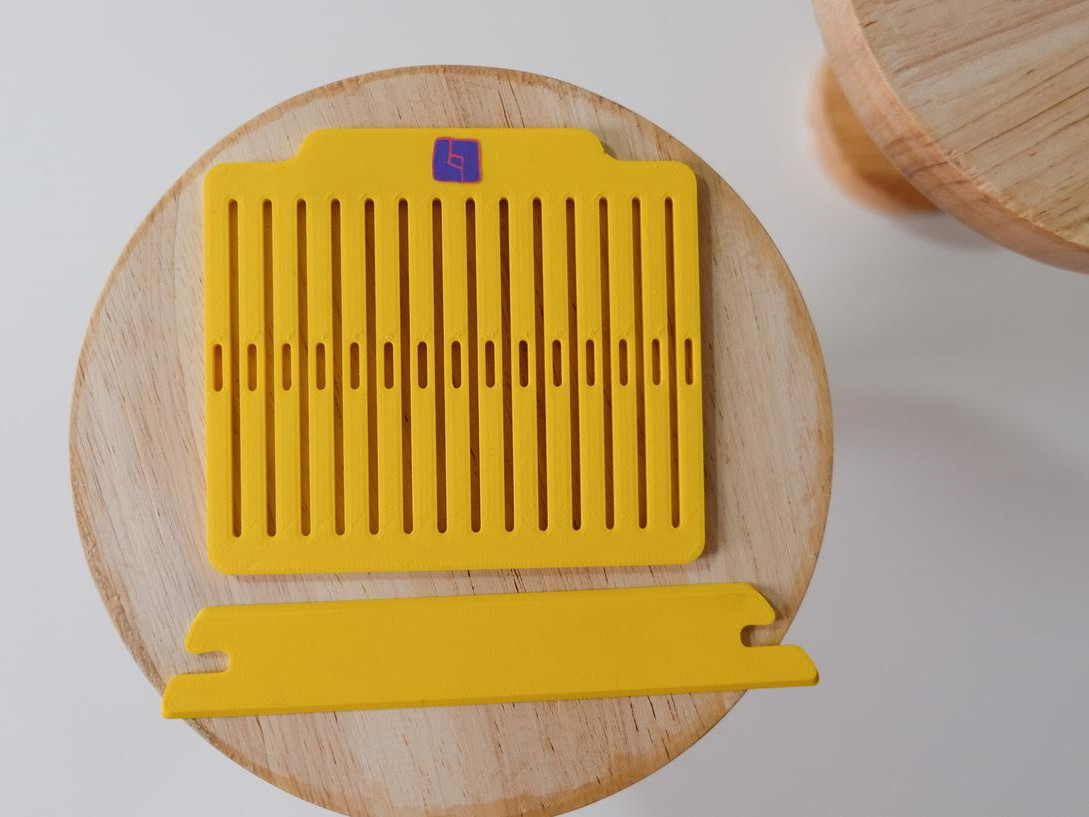
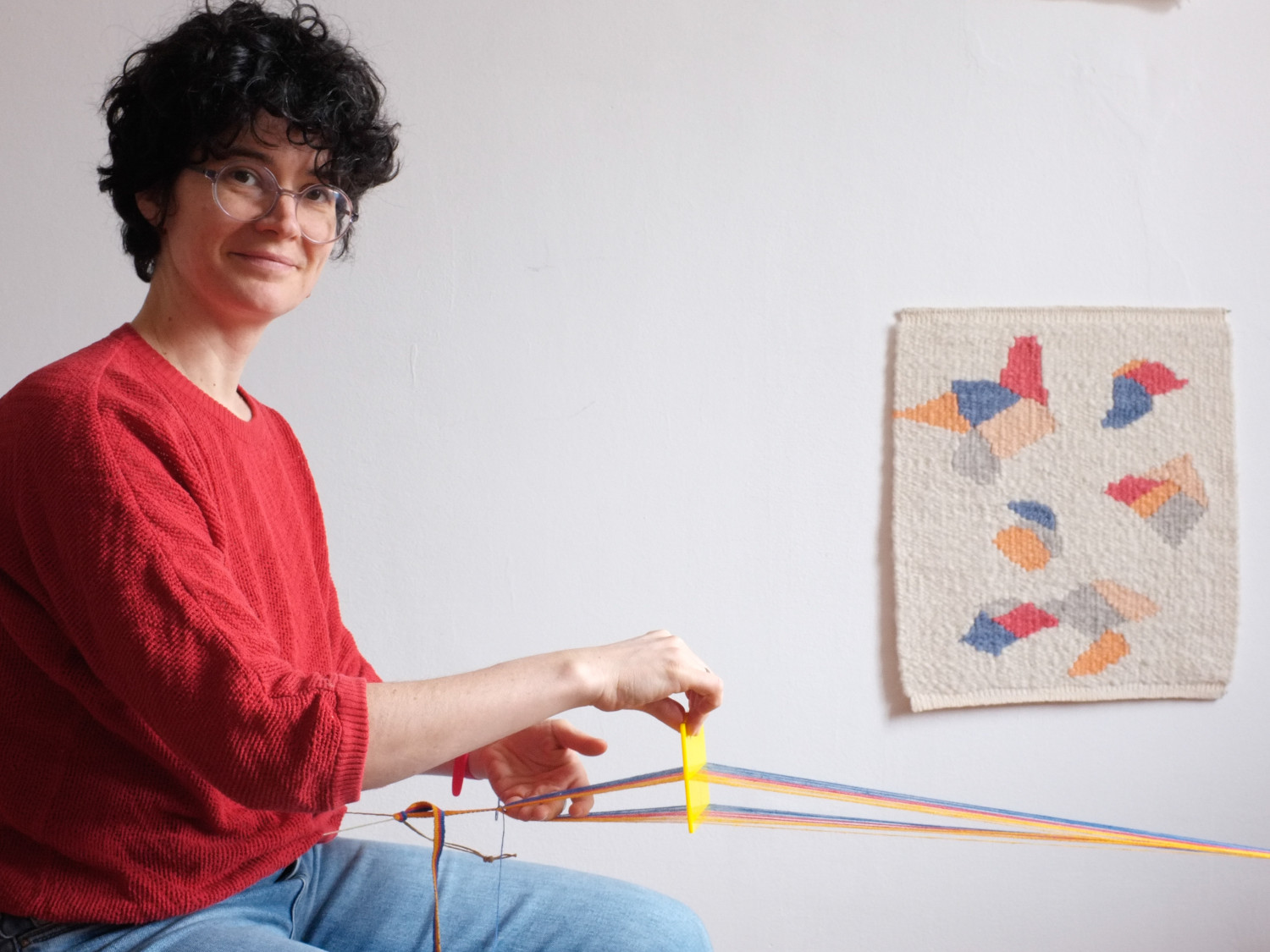
EEVI GARDENS - HANS-HENNING BÖRSTINGER & VIPUL KHATANA
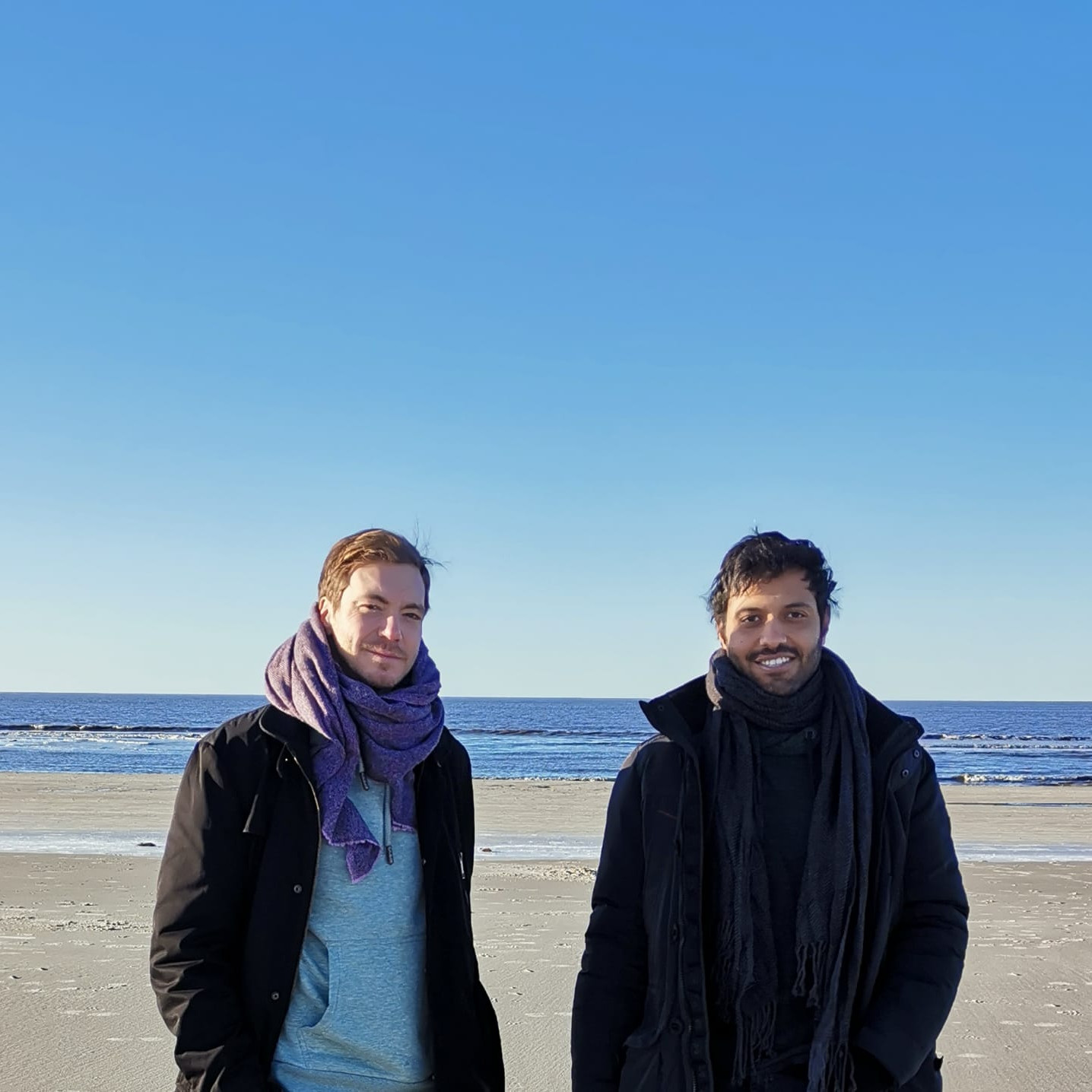
With Eevi Gardens, Hans-Henning and Vipul make a variety of regional and exotic favorite flavors accessible and convertible.imagine a floor lamp that provides passive lighting for the home, putting the beauty of the plants in the spotlight and ensuring the well-being of the plants and residents through daylight quality. - This is Eevi. Automated watering cycles mean you don't have to worry about maintenance for up to 3 weeks. The realization of this project was a very important matter for both of them.
When selecting the materials and work processes, they paid attention to the highest standards and quality. In order to combine food and user safety with user-friendliness in a sustainable product, they experimented with a wide variety of materials - and therefore also machines. Above all, the 3D printers and almost 800 hours with Fusion ensured that the design didn't just remain an idea in their heads, but ended up in front of them as Eevi.
"The Distributed Design Residency has placed the topics of circular economy, sustainability and logistics at the center of our development and work processes. One of the guiding principles of distributed design in our own interpretation "let the design file travel, not the product" has become deeply rooted in our work. Production in the customer's region has become a central element in our business model and was already planned as part of the manufacturing process. Thanks to the large number of industrial machines required and their provision, Happylab has made professional implementation economically feasible in the first place. We know of no other place than Happylab that allows us to do this in this setting close to the city center - from concept to production to finishing."
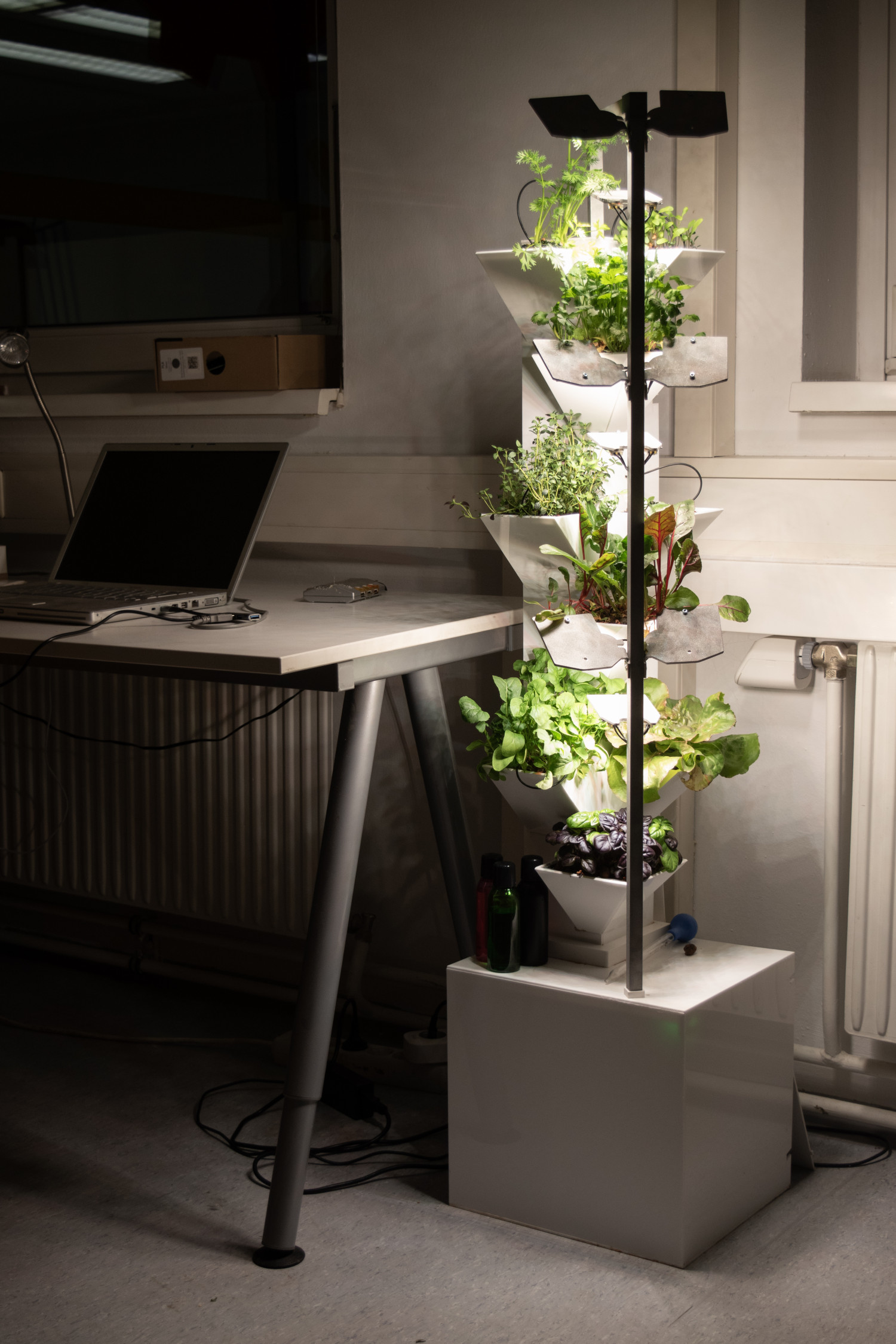
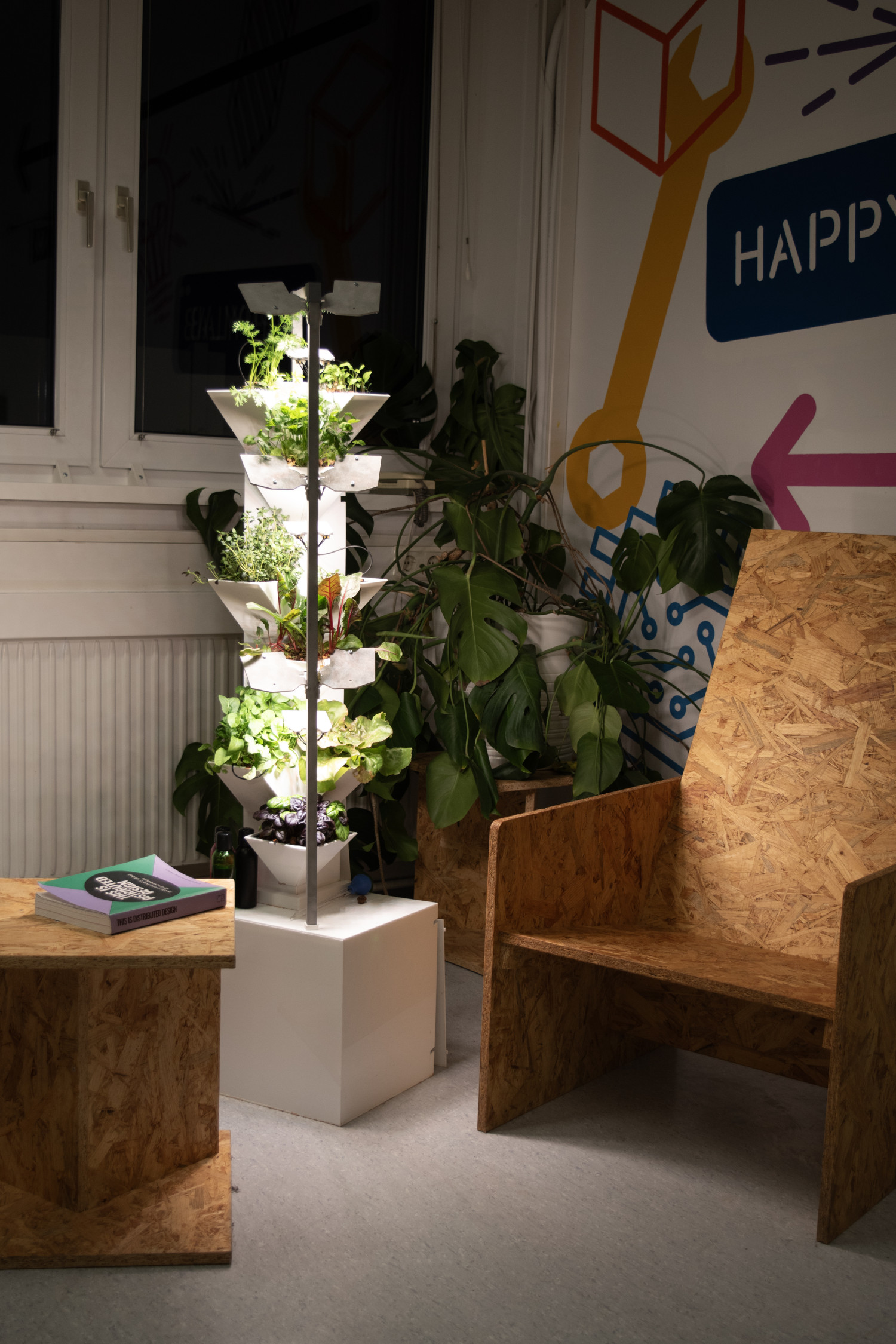
DESIGN BRAIDED TEXTILES - KATHARINA HALUSA
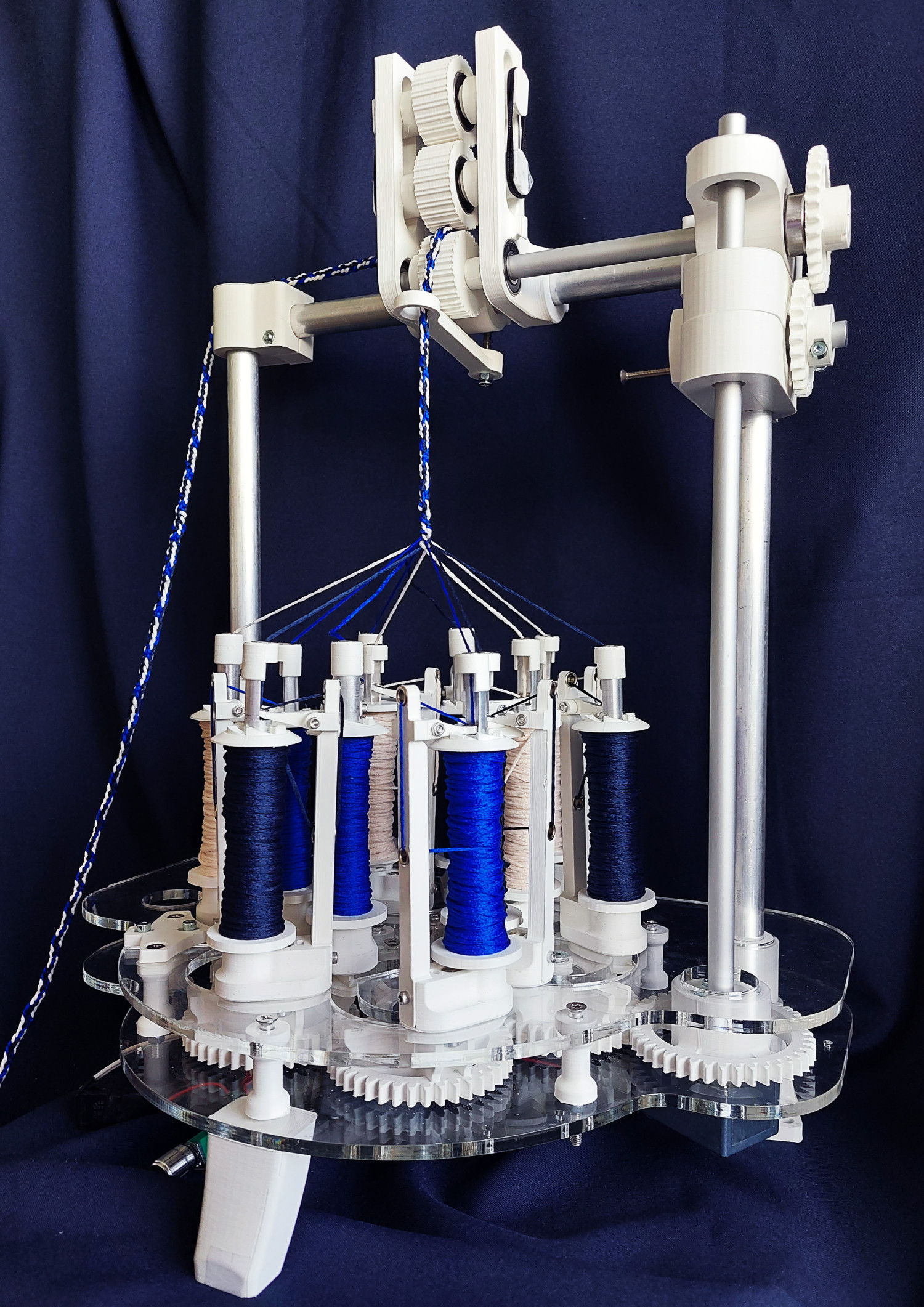
In Katharina's master's project BRAIDED TEXTILES in Fashion&Technology at the University of Art and Design Linz, textile braids were produced on a radial braiding machine.
In the residency, she has now produced a braiding machine on a smaller scale, which makes it possible to create textile braids and experiment with different yarn materials. Based on the DIY 3D Printed Braiding Machine by Fraens, different textile fibers (sustainable natural and synthetic fibers as well as biomaterials) are used. These braids could be used as accessories (e.g. bracelets or necklaces) and in clothing.
In the Happylab, she mainly used the 3D printer to produce the individual components for the braiding machine. Well over 100 individual parts were printed with it. The laser cutter was also used to cut the base plates for the braiding process. She also found the Happylab store very practical for purchasing the necessary screws and other accessories directly. Once all the individual parts had been manufactured, the assembly could begin.
"Happylab really helped me with the consultation sessions. As I don't have a technical background myself, I found some of the steps involved in assembling and preparing the individual parts difficult. During the consultation sessions, I was shown and given suggestions for solutions to my project/problem within a very short space of time. The learning process was enormous. The discussions with the other participants were also great and gave me new perspectives on my own project."
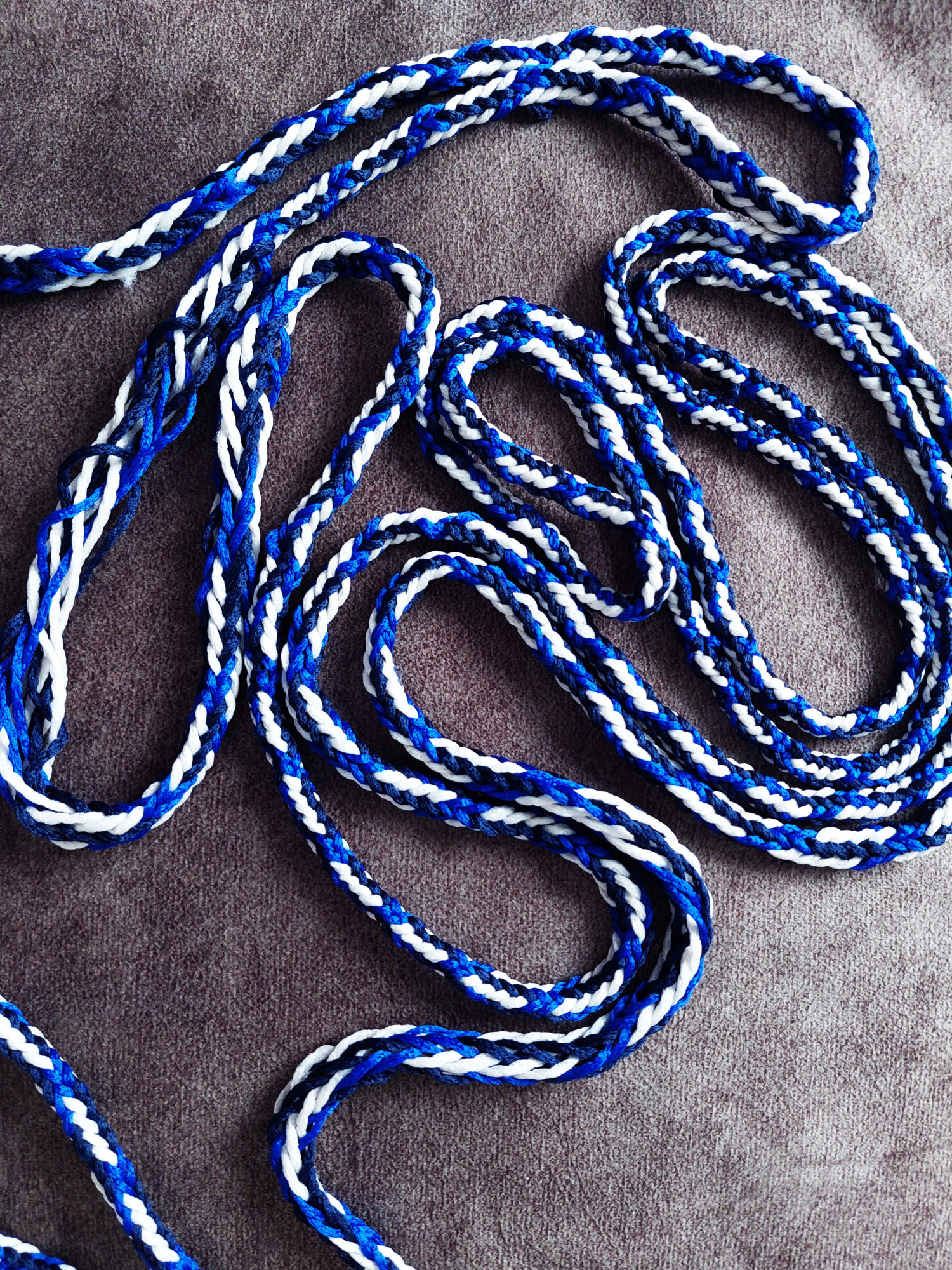
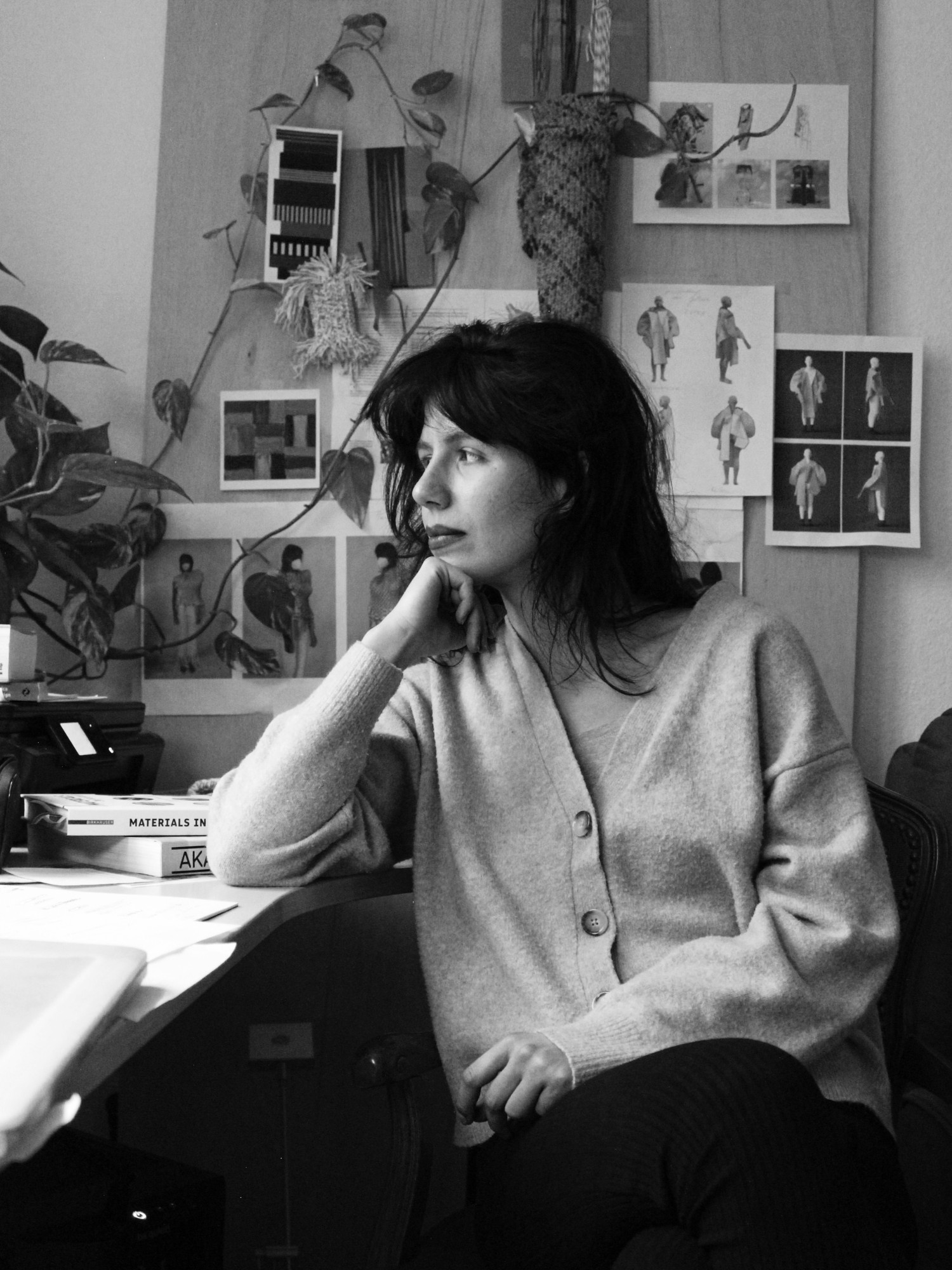
REPLIFACTORY - CATALIN RUSNAC
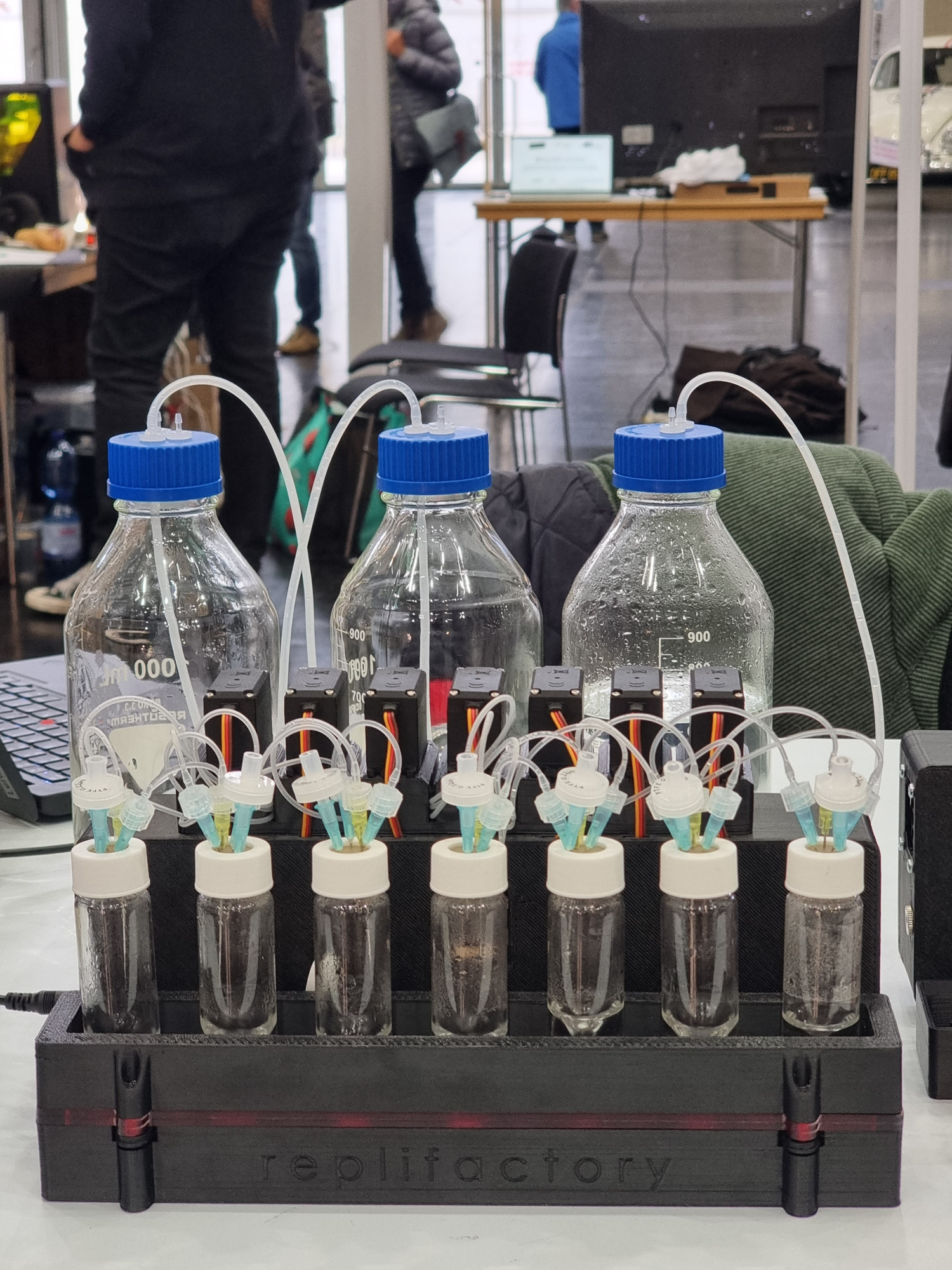
Catalin has designed replifactory, a 3D-printed laboratory device for growing bacteria. It enables a variety of typical biological experiments to be carried out - including a morbidostat (keeping the stress level constant for the culture in order to adapt it to a stress - such as antibiotics or metals). A morbidostat is a very complicated laboratory device that needs to be operated and maintained by a technician, as existing designs have not been optimized.
Catalin has designed a version that is compact, easy to clean and inexpensive to build and has been developing it over the past few months. The result is an experimental evolution system - a kind of "fitness trainer for bacteria"
At Happylab, Catalin used the electronics workshop to solder circuit boards, the (metal) laser cutter and the CNC machines to develop components and devices for assembly.
"The Distributed Design Residency helped me develop my project by connecting me with a community of enthusiastic like-minded people. I had stimulating discussions with other makers and experts from different fields who come together at Happylab."
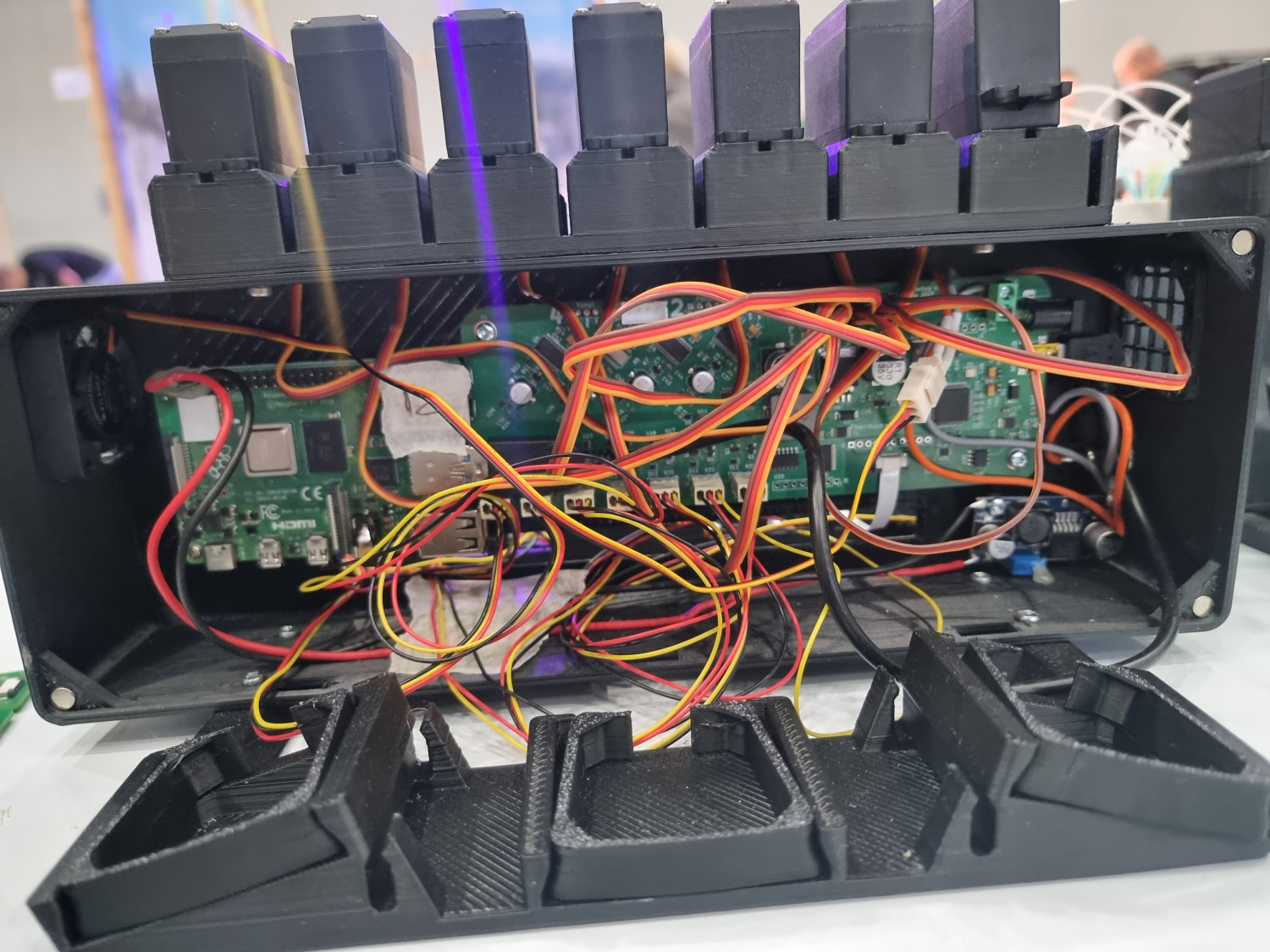
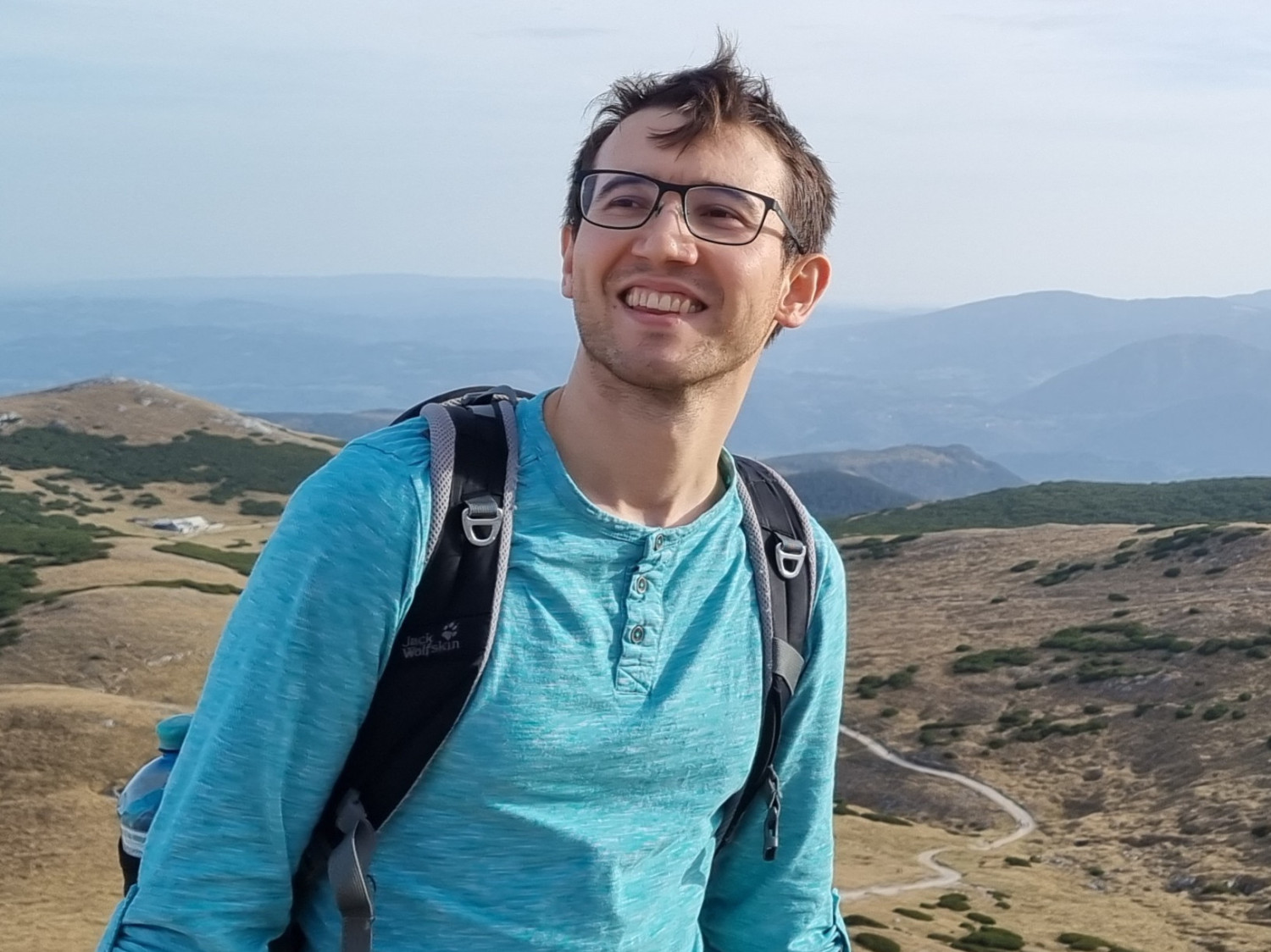