The idea of taking workshops from Happylab on the road has been in the works for quite some time. Now, it's finally here: our Mobile Maker Lab has arrived! And no, it's not a large truck but a small, sophisticated, and eco-friendly alternative. It's a bicycle trailer equipped with simple, mobile production machines.
The trailer is based on an open-source design by "Carla Cargo" and was built entirely within the Happylab over the past few months by Roland and Gerhard from the Happylab team. They've been welding, sawing, painting, and even upcycling a part of an old children's bike to make it happen.
We asked them what motivated them, how the project progressed, and where they envision the journey with this flexible lab is heading.
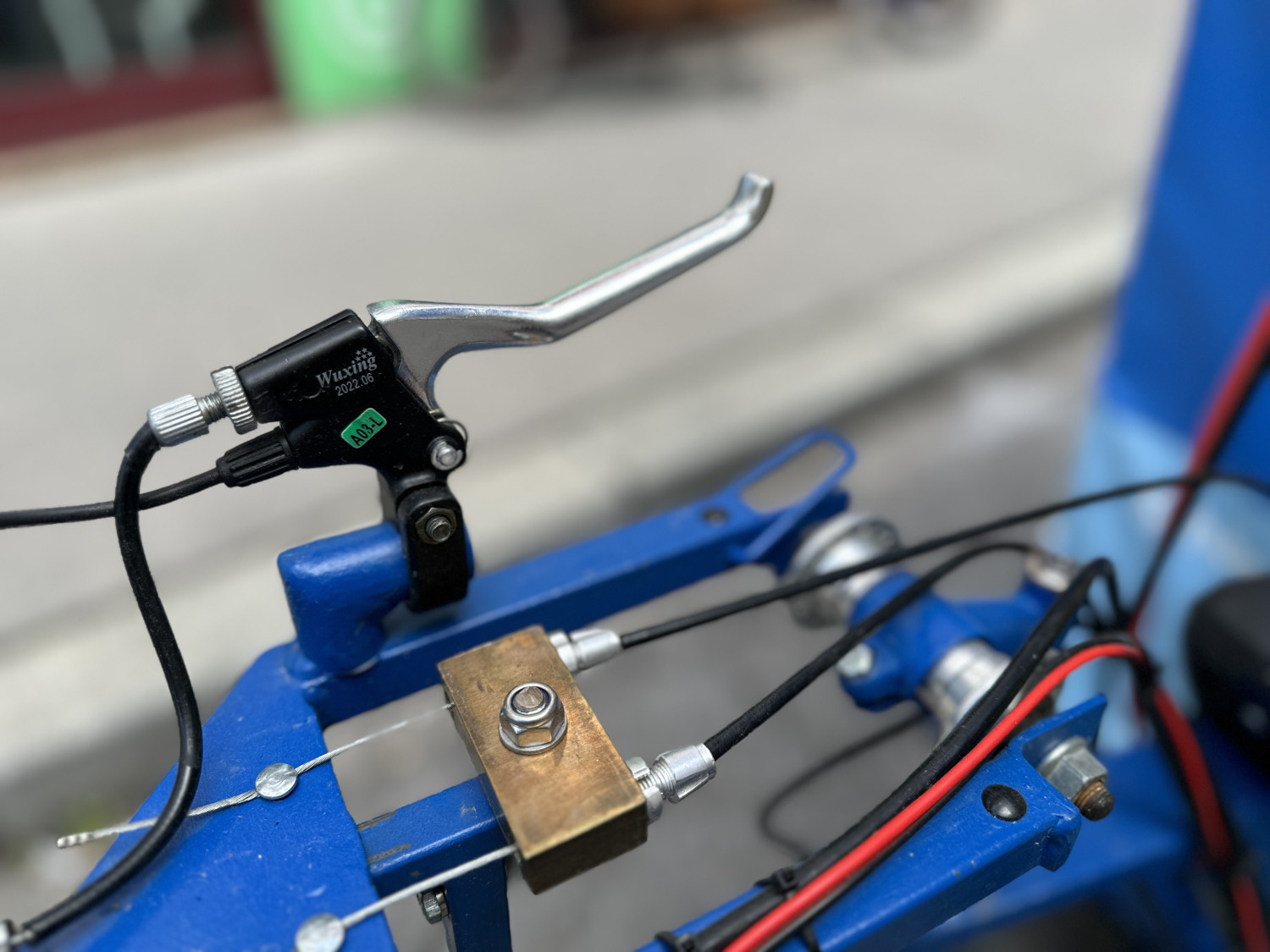
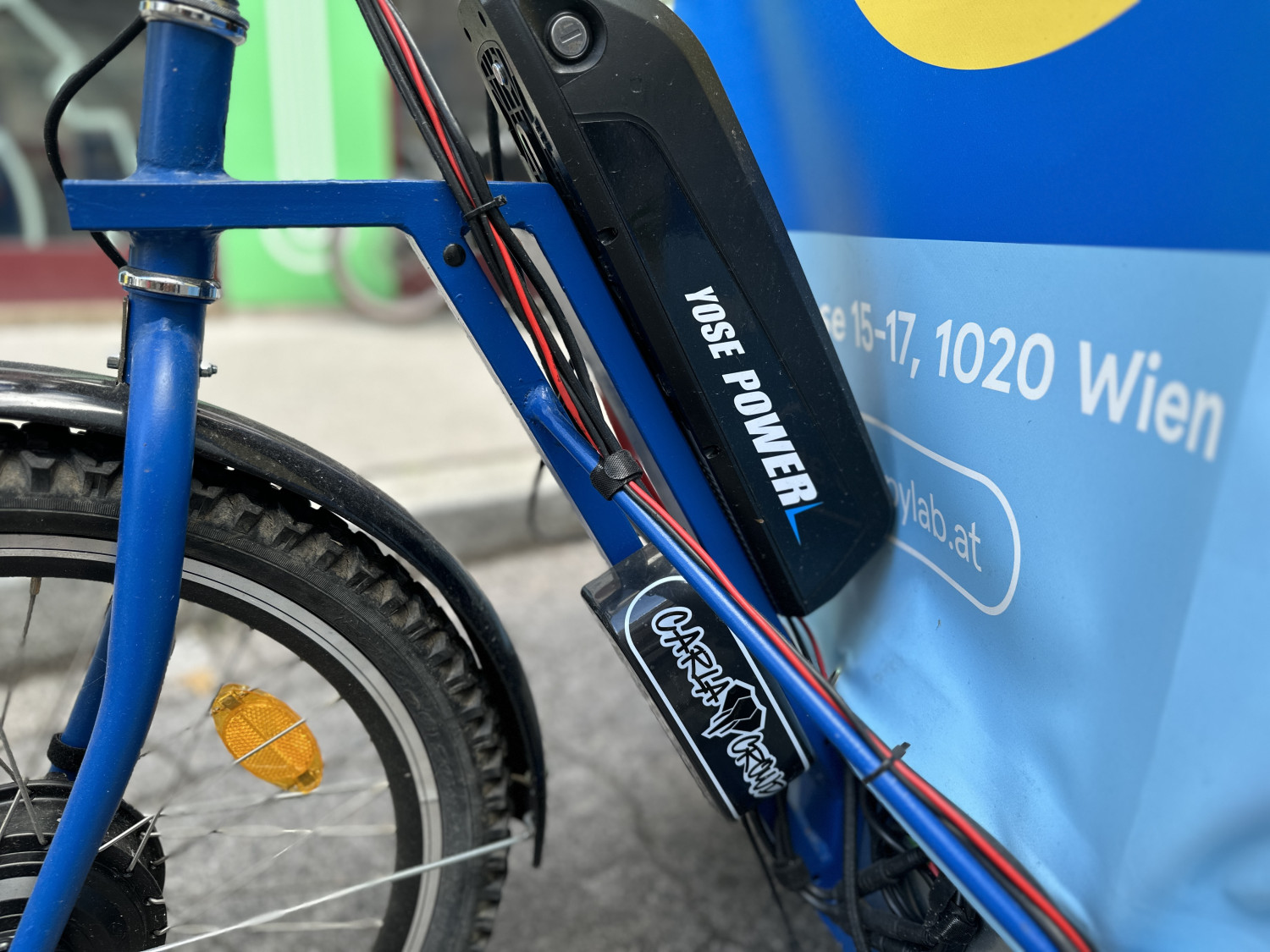
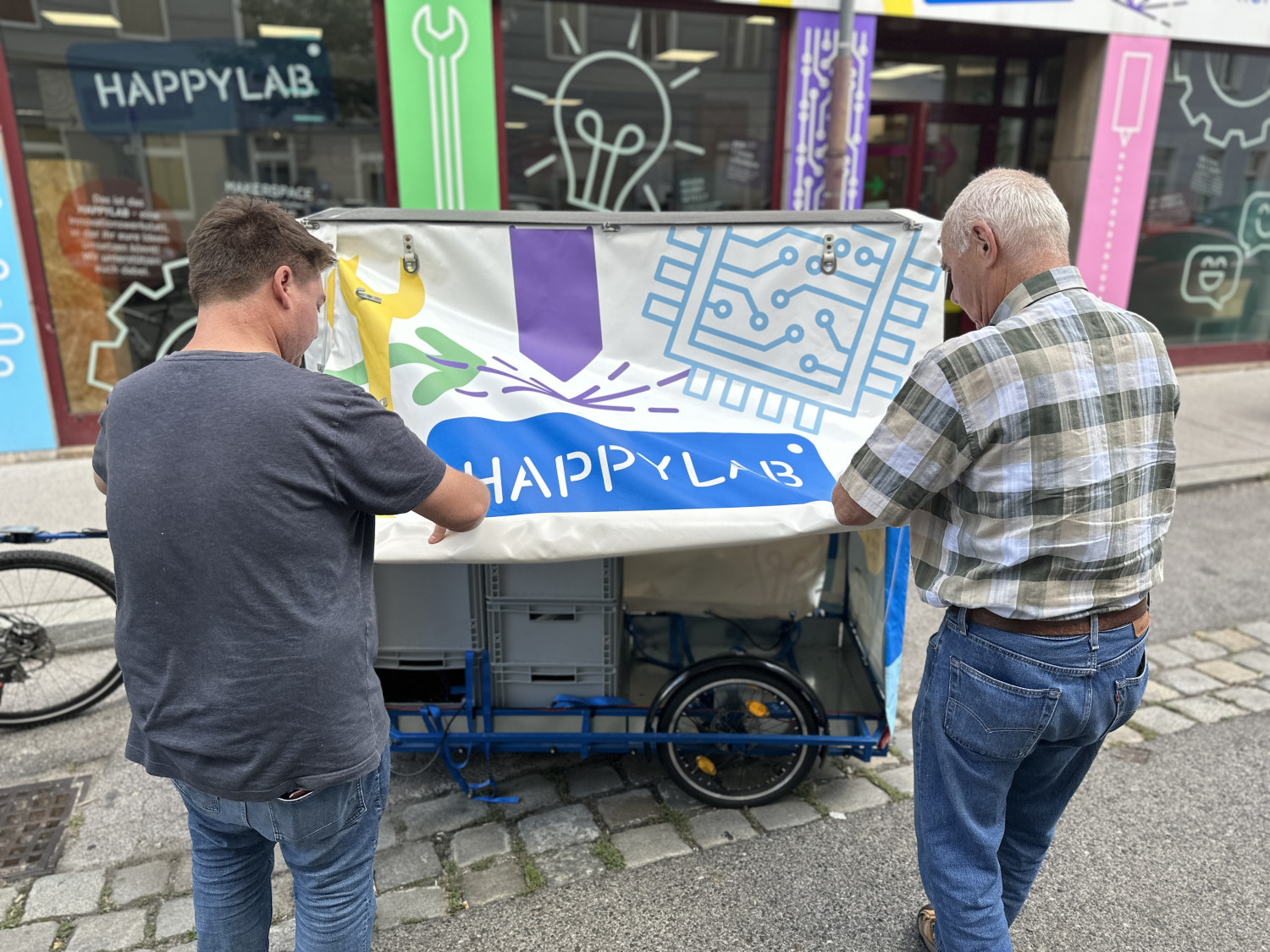
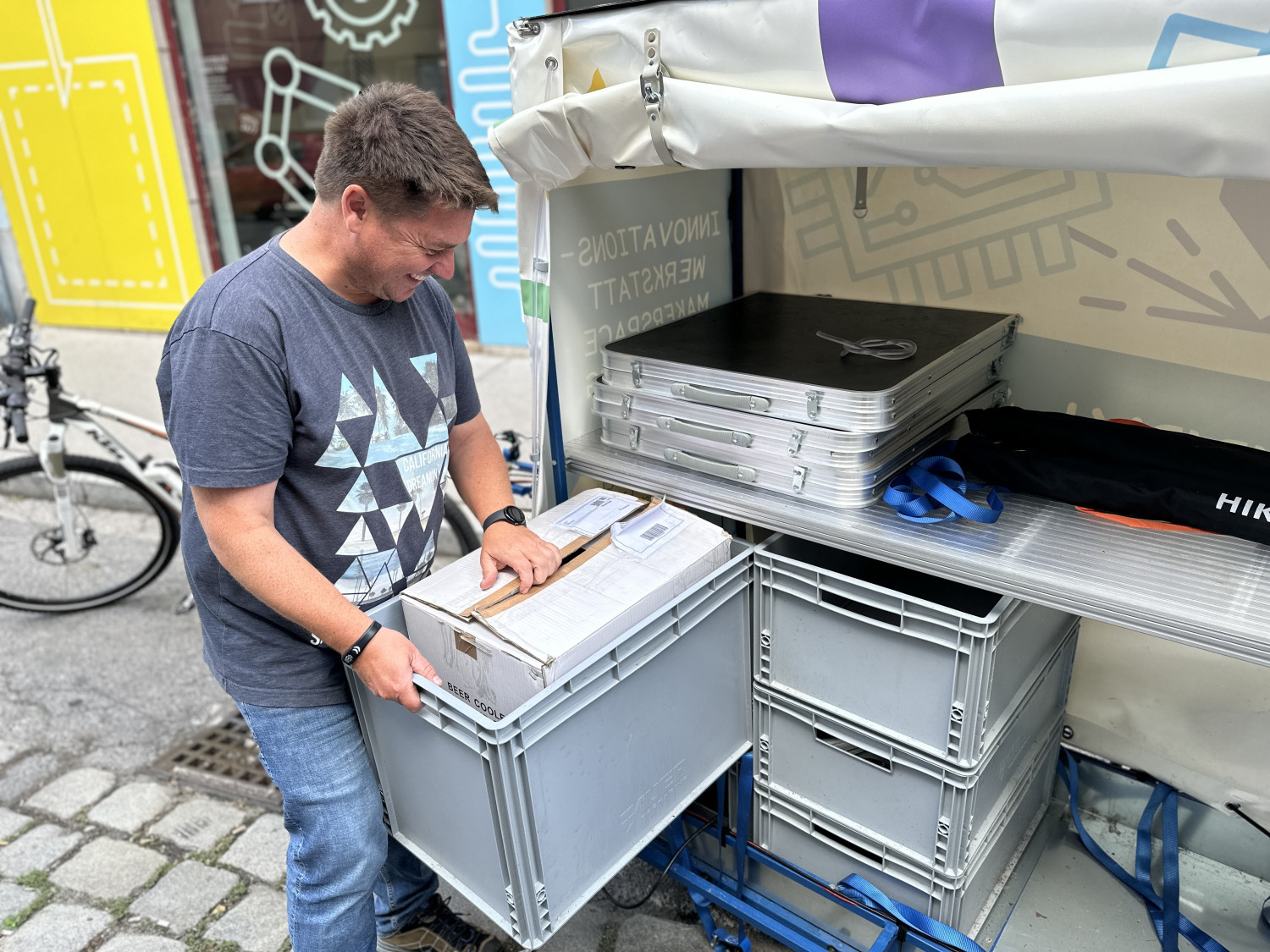
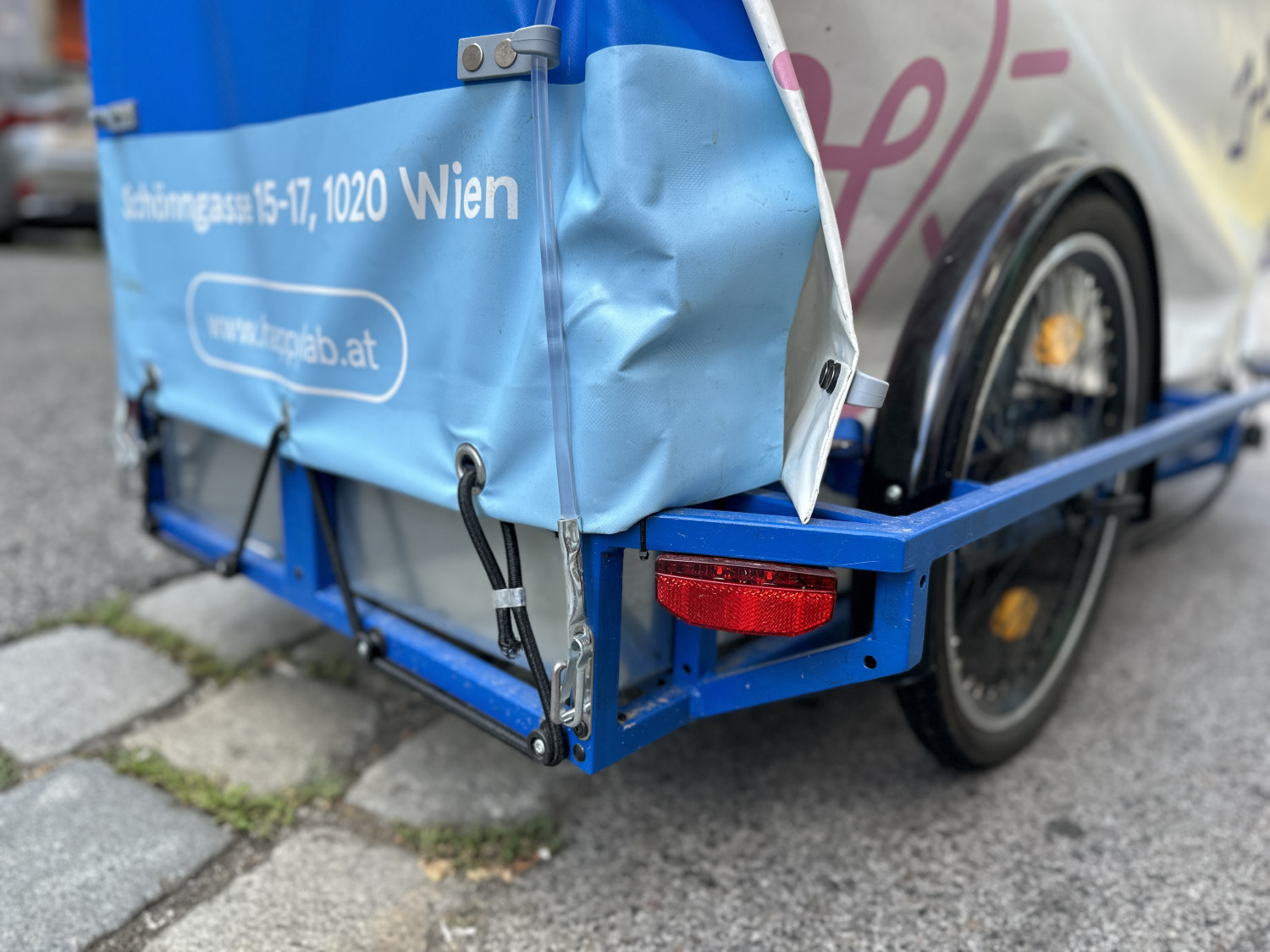
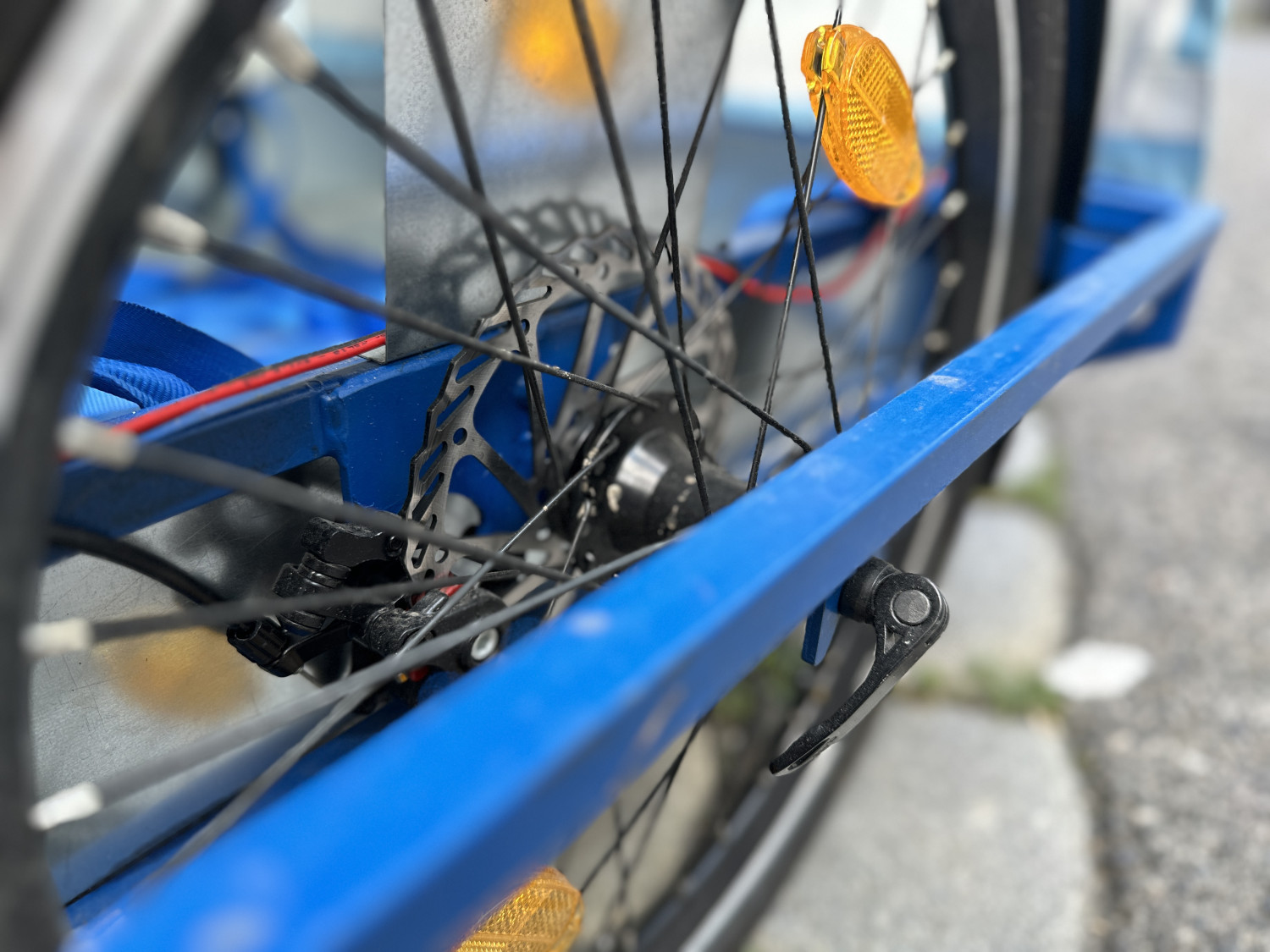
Interview with ROLAND UND GERHARD
How did you come up with the idea to build this bicycle trailer?
Roland: We thought it would be really cool to be able to transport a Mobile Maker Lab with a bicycle. Using a car would have involved ongoing costs, and the environmental aspect was also crucial for us.
We also wanted to take a different approach than many other Fablabs. Our trailer can be customized - depending on the workshop, we fill the integrated boxes as needed. On top, we've set up a small solar power station so that we have electricity available to operate various devices.
How did you plan the project?
Gerhard: We were able to build the trailer frame itself as a whole using the open-source plans from Carla Cargo. The rest - such as the structure, cover, and so on - we developed through learning by doing. We asked ourselves, "What do we want to do?" and then started measuring. We took the dimensions of standard boxes and based the construction on that.
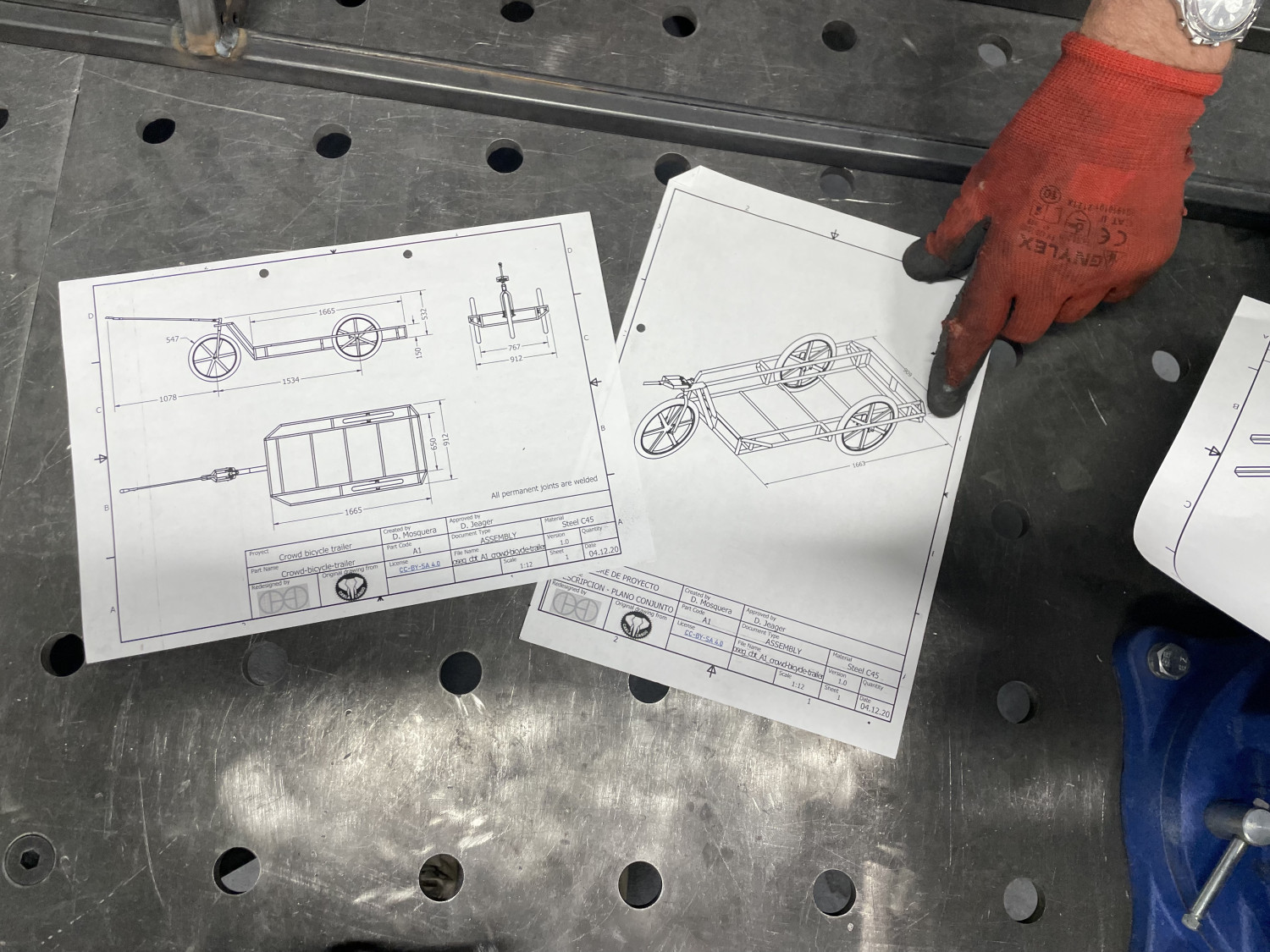
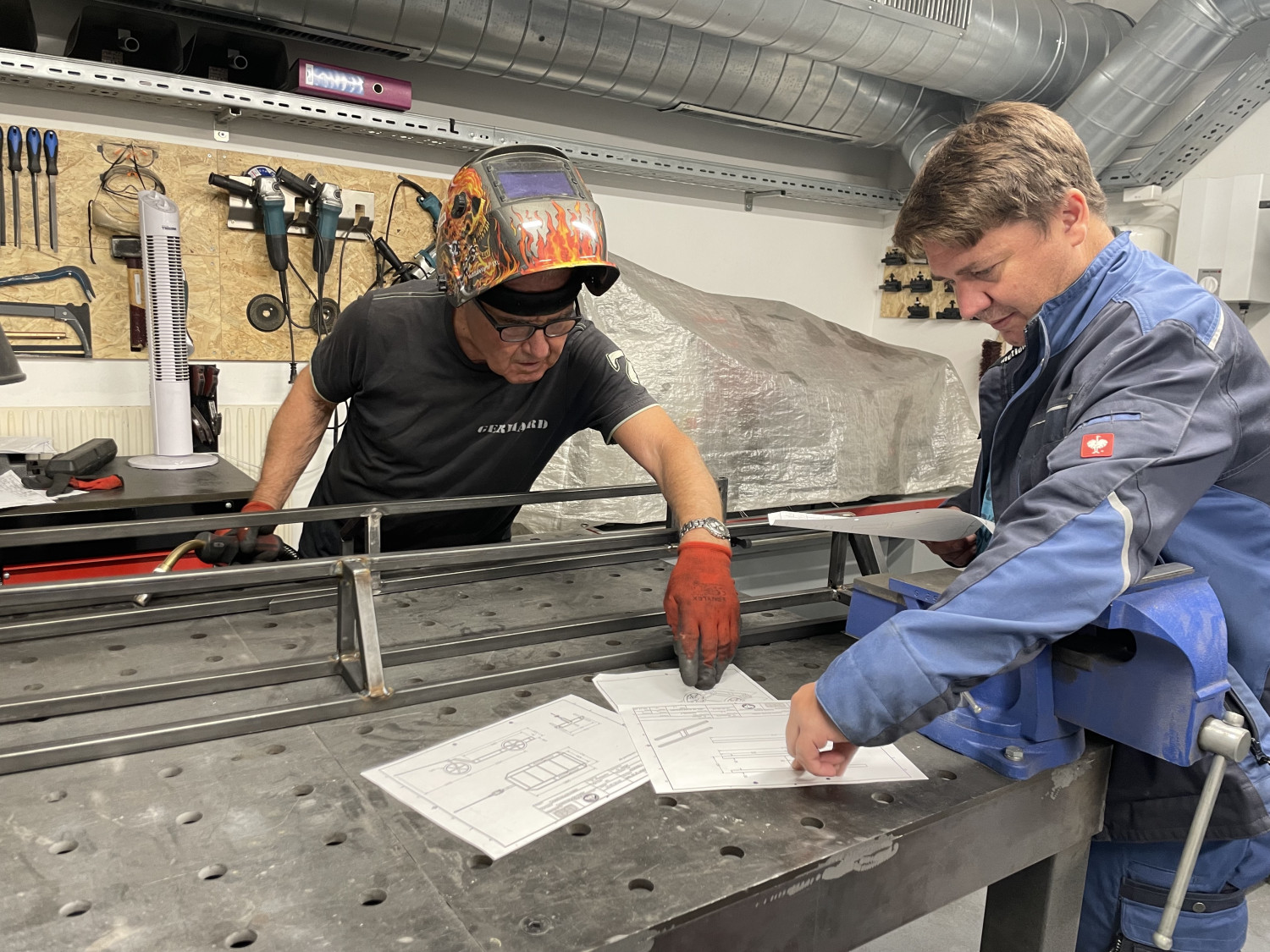
What materials and machines did you use for this project?
Roland: The frame is made of steel. We also used bicycle components, a hub motor plus controller, and a cover. We also looked at the materials we had available in the lab and upcycled some used materials.
Gerhard: We used various metalworking machines: a bandsaw to cut the steel pipes, a welding table and a MIG welding machine for welding. We used an angle grinder to smooth the welds, and various hand tools. We painted it in the finishing room, and at the electronics station, we soldered cables for the lights and control. We ordered the cover and the solar panel.
Were there any challenges?
Gerhard: Not too many, actually. The electronics sometimes acted up a bit, but we managed that well. And we did order some accessories incorrectly, but we learned a lot from those mistakes.
Roland: Although I was a bit uncertain about whether the brakes would work well. The trailer can have a full load of over 200 kg, and it has overrun brakes, which means it brakes as soon as it comes into contact with the towing vehicle. That was interesting the first time we went downhill. But it surprisingly worked quite well from the beginning.
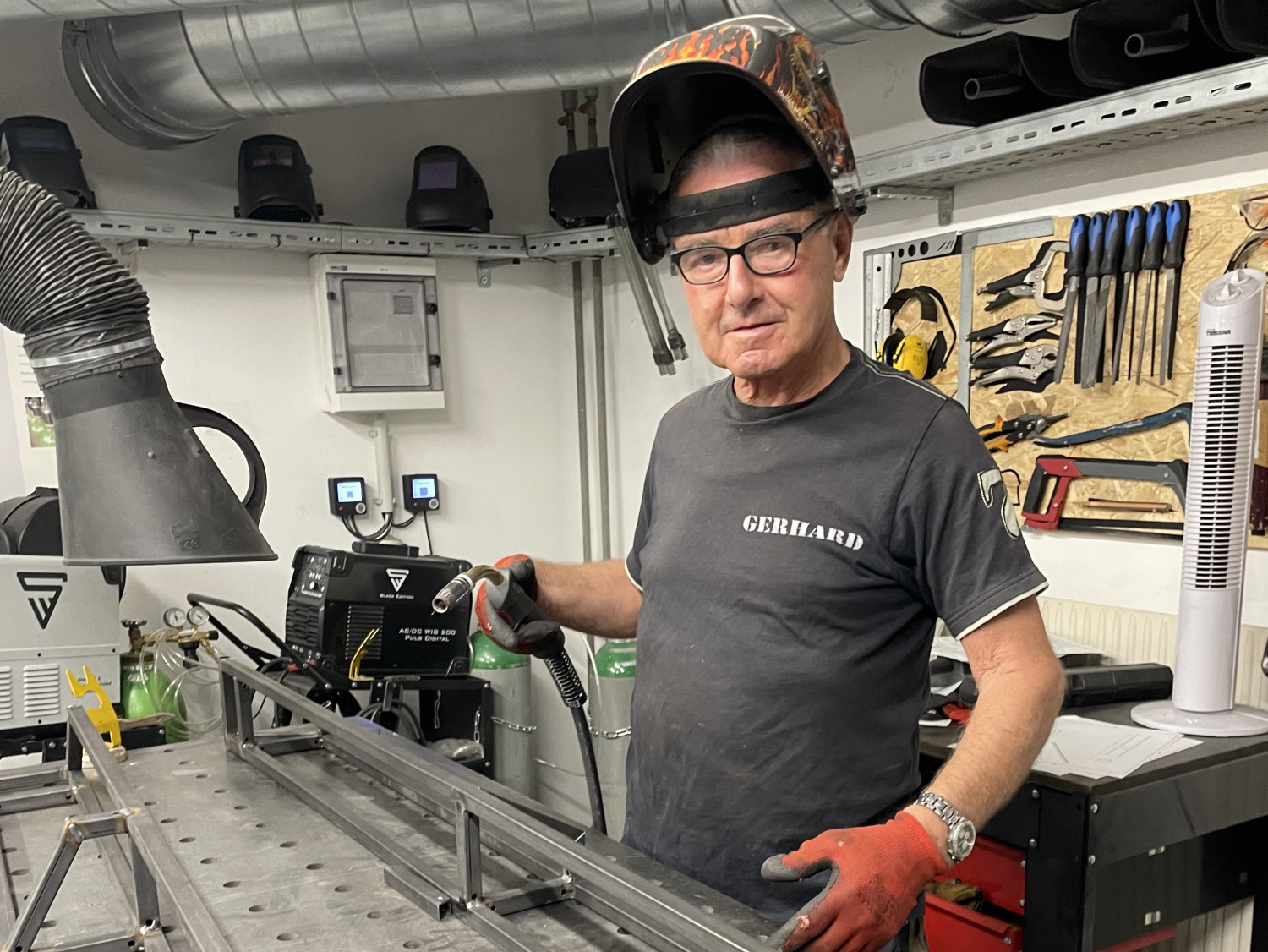
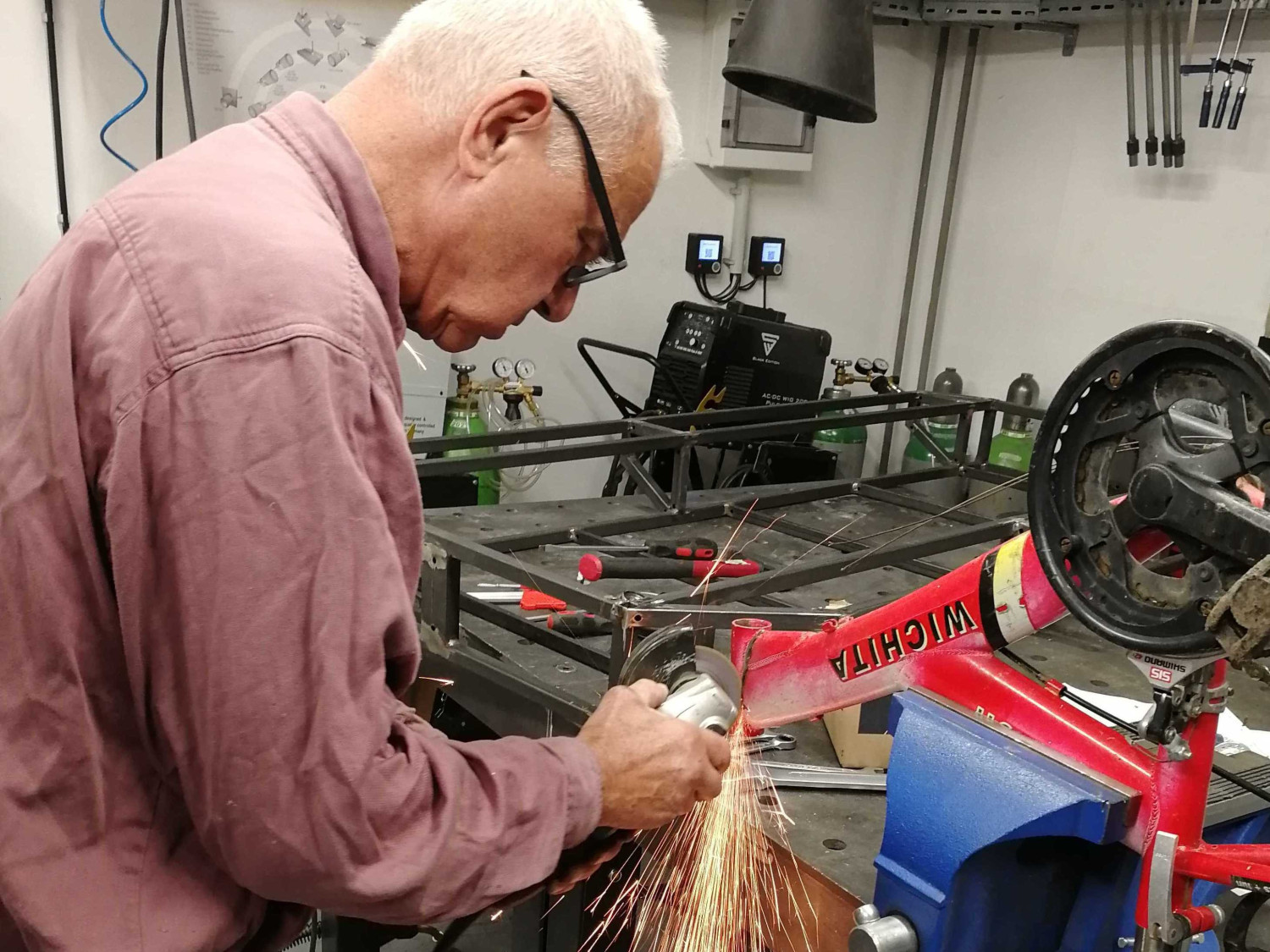
What's the plan for it now?
Roland: The first event was at our summer party on the Danube Island. We had everything from a grill to a drink cooler with us. That was the christening - in every sense of the word, because it was pouring rain.
And for the future, we have various ideas. In the autumn, we're organizing workshops for young people with A1. For example, we'll be printing T-shirts. We're also in talks with "the cool tool" to make their workshops mobile. Additionally, we can offer various sessions with the Mobile Maker Lab in schools, youth centers, parks, or at events. Team-building events are also possible. In any case, we want to familiarize as many people as possible with the topics of making and digital production.
Gerhard: By the way - you can also pull the trailer without a bicycle and travel on foot because it has its own motor.
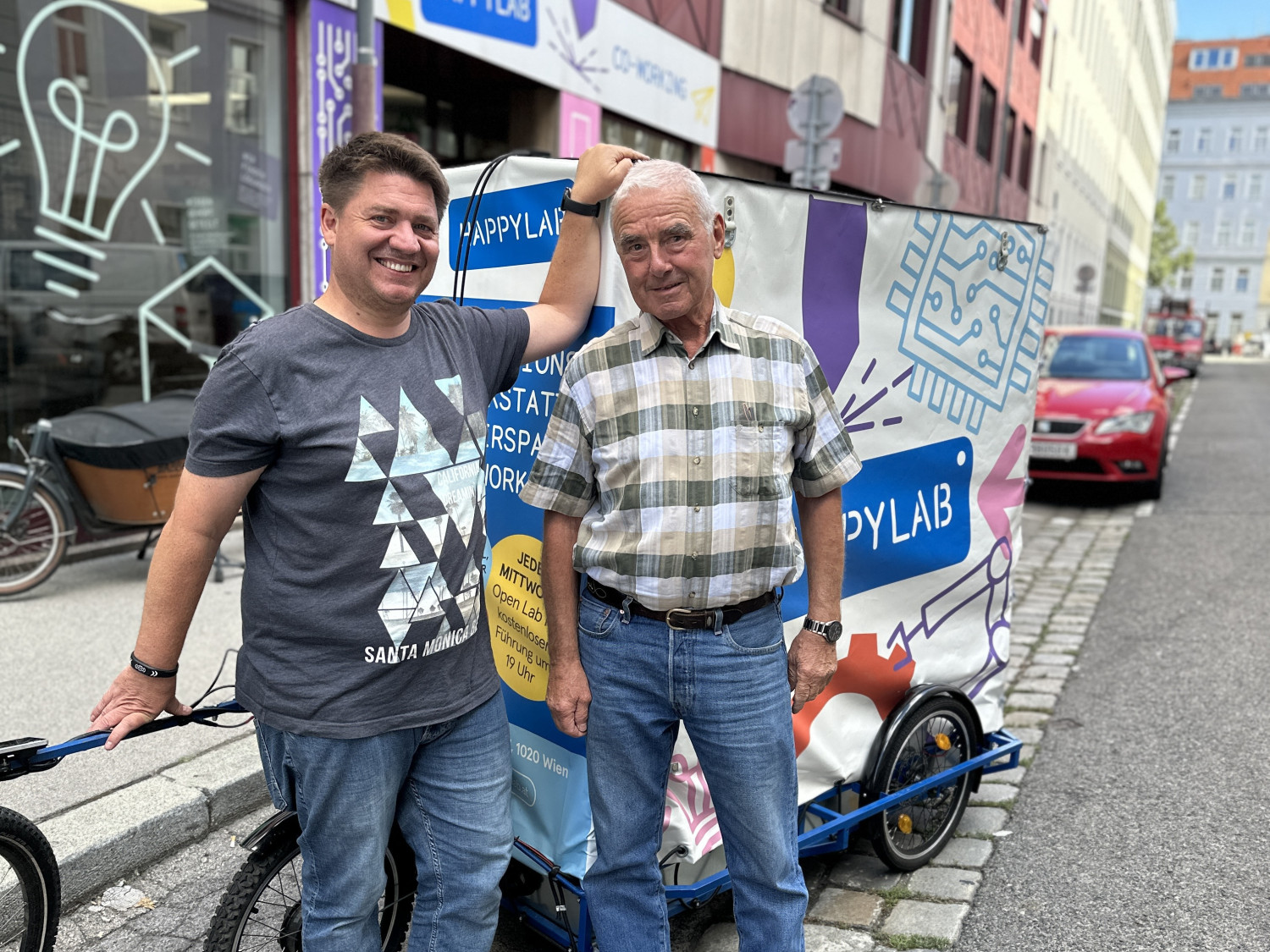