After a successful first round of the Distributed Design Residency, we are once again teaming up with the Distributed Design Platform to support creative talents this year. From September 2023 to February 2024, we will be assisting makers and designers here at Happylab in bringing their projects to life. Following an Open Call, we have selected seven intriguing concepts. Our choices were based on criteria such as feasibility in the Makerspace, design, as well as the social and environmental impact of the work.
Our residents will gain access to the diverse array of machines at Happylab (3D printers, laser cutters, CNC milling machines, wood and metal workshops, etc.), receive training in the Makerspace, project-specific guidance, and studio spaces. The goal of the residency is to seamlessly integrate design and making, whether that involves realizing an idea, creating initial prototypes, or producing a small series.
Curious about the projects? Here's a sneak peek.
THE PROJECTS:
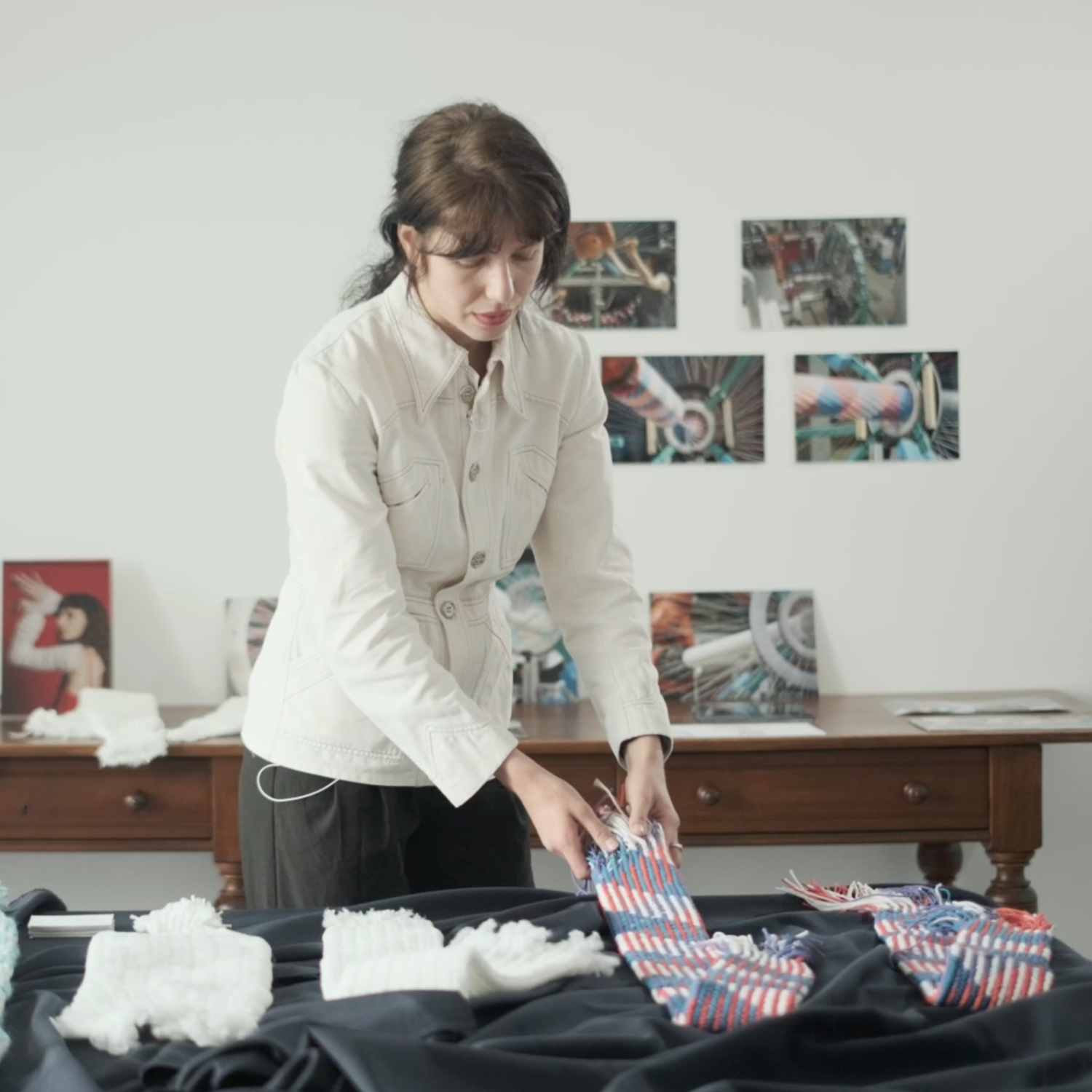
Design Braided Textiles - Katharina Halusa
The DESIGN BRAIDED TEXTILES project explores woven textiles as an alternative material for accessories and clothing. An innovative manufacturing process modernizes and reinterprets the craft of "braiding anew," infusing traditional weaving techniques with machine-assisted processes.
In Katharina's master's project, BRAIDED TEXTILES in Fashion & Technology, textile braids were produced using a radial braiding machine. Now, she intends to create a smaller-scale braiding machine that enables the production of woven textiles and experimentation with various yarn materials. These textiles could find applications in accessories (such as bracelets or necklaces) and clothing.
"The DESIGN BRAIDED TEXTILES project aims to enable a new form of alternative fashion design, accessible to everyone, for a textile future that is sustainable and less harmful to people, the environment, and the climate," says Katharina.
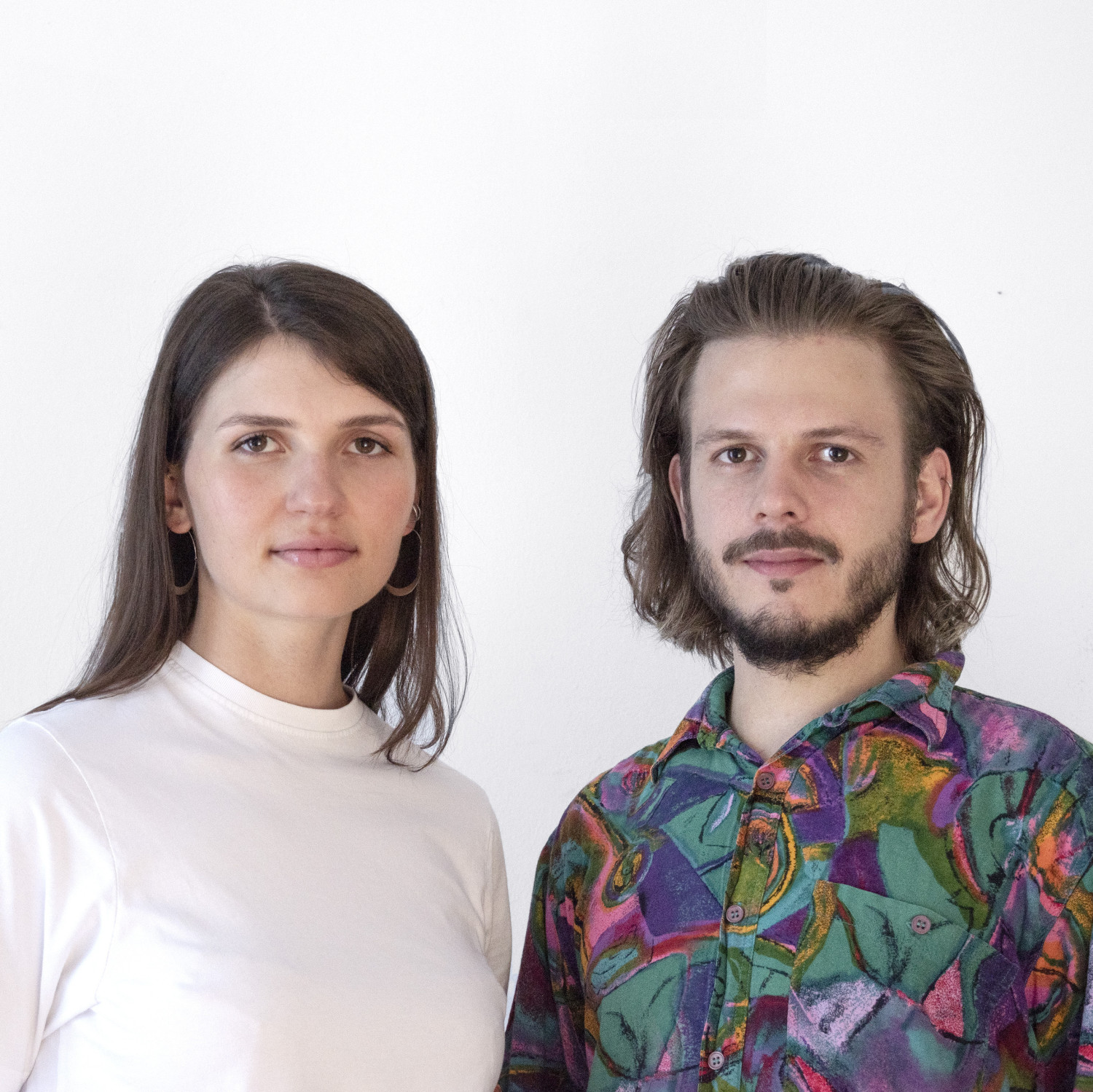
Handmade massproduction - Mariia Samahala & Mykhailo Zhuk
"Transitioning to slow consumption is incredibly important. Design should not only be durable but also permanently repairable and recyclable. To ensure all these qualities, we use industrially prefabricated and widely available parts in our designs," say Mariia (Masha) and Mykhailo (Misha). The architects live and work in Vienna and have experimented with furniture design during their studies.
Utilizing mass-produced parts significantly reduces production costs, saving both material and time. This approach can make high-quality, handmade, and long-lasting design pieces more affordable to a broader audience. A handmade design furniture piece becomes an assembly of mass-produced components. During the residency, they would like to create two prototypes and refine their designs to a point where producing a small series becomes feasible.
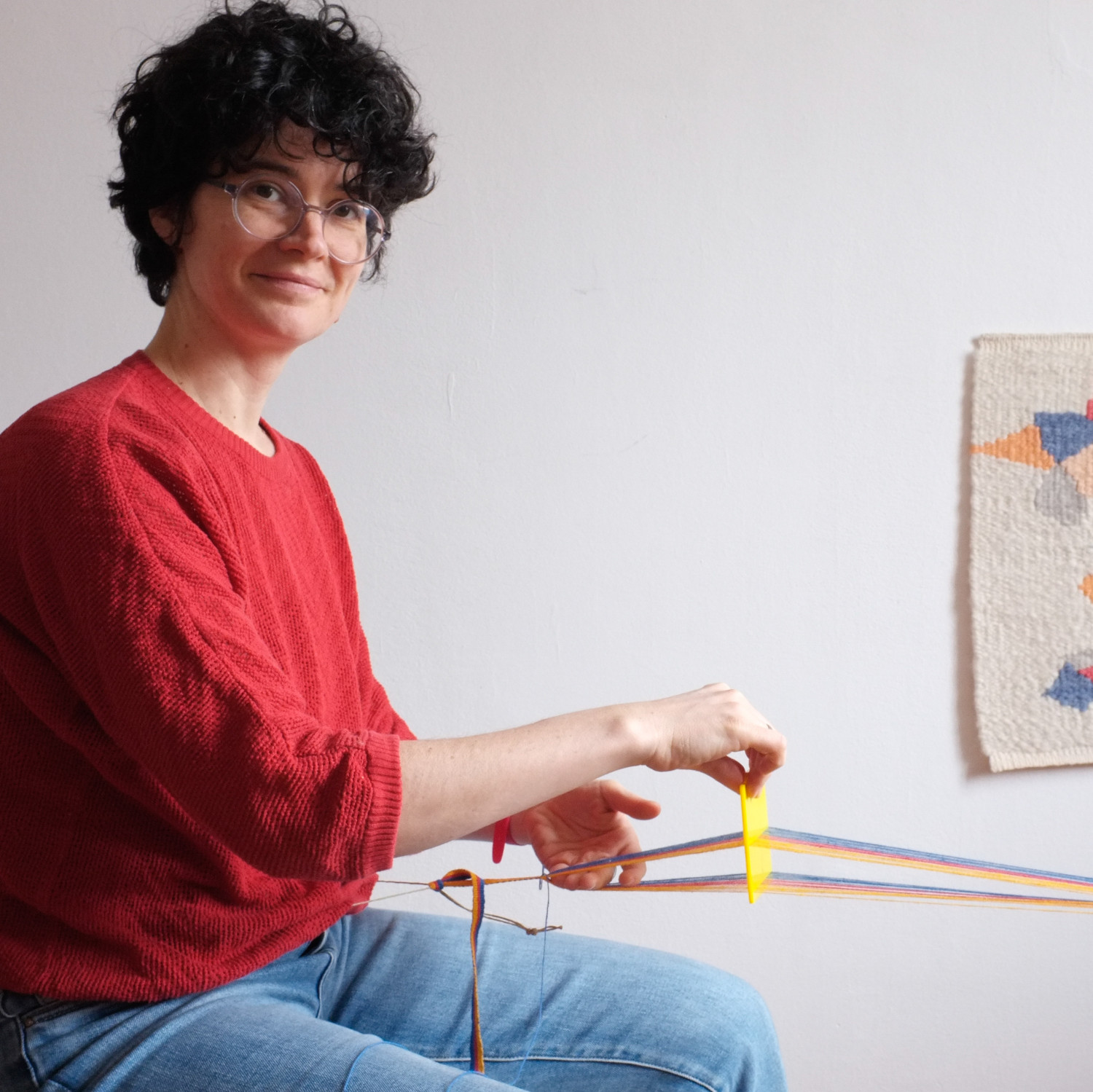
Weaving with Johann - Gundula Hickisch
Coming from a background in art history, Gundula landed in the world of weaving a few years ago. Specifically, weaving on looms. She weaves, assists with loom setup, and shares her knowledge through courses and workshops for those interested in learning about the craft of weaving.
"As simple as possible, as stylish as possible. I want to develop and produce a beautiful and simple weaving device with accessories: plain, sustainable, and easy to use, made from plastic or wood," explains Gundula. She already produced a small series of Johann devices in Happylab last fall. Now she knows what works and has even more concrete ideas for refining Johann. And she aims to bring these ideas to life during the residency.
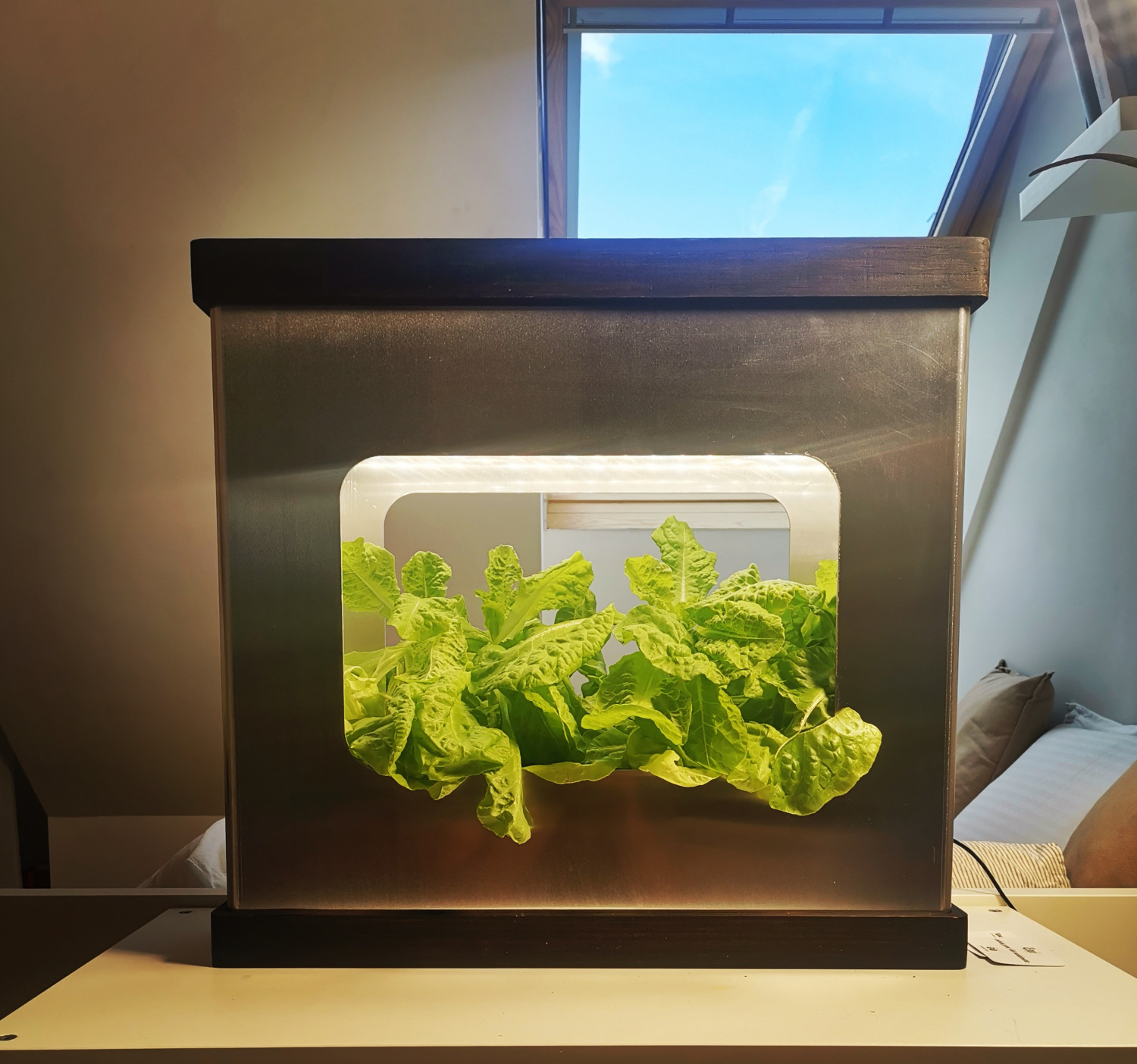
Eevi Gardens - Hans-Henning Börstinger & Vipul Khatana
With the Eevi Gardens project, Hans-Henning and Vipul aim to create innovative food solutions for urban populations. A smart indoor garden (Eevi) provides year-round access to fresh salads, herbs, microgreens, and vegetables, supplying users with wholesome nutrients through a sustainable product that eliminates packaging and supply chains.
"For its implementation, we've combined the time-tested technology of hydroponics – where plants root in mineralized water instead of soil – with state-of-the-art lighting technology. Our Eevi's are finely tuned to the plant's life cycles, supporting their natural potential from seed to harvest," explain Hans-Henning and Vipul. During the residency, they hope to gain insights for enhancing user-centric design. Furthermore, they plan to embed the concepts of Distributed Design and Circular Approach into their business plan.
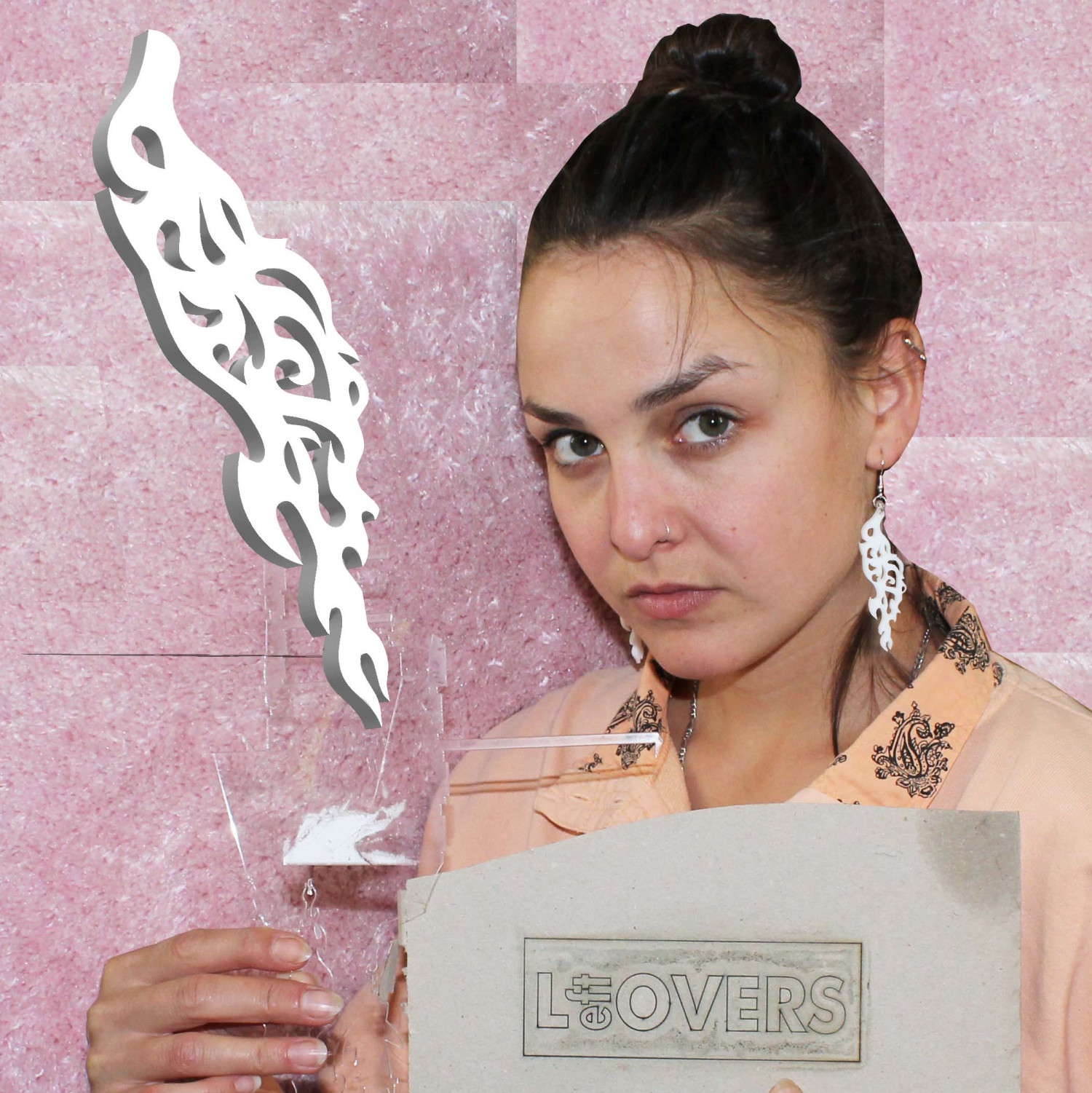
L(eft)OVERs - Nina McNab
Often, leftover cuttings from laser cutting go unused. However, even from small scraps, it's possible to salvage intricate shapes and elements, transforming them into jewelry collections.
Nina studied Textile Art and Design at the University of Art and Design Linz and works as a freelance artist. She already partially uses rescued or gifted cutoffs in her work. Throughout the residency, she will delve deeper into the possibilities of a circular approach and laser jewelry design. "Sharing the designs as open-source aims to enable everyone interested to make use of these cutoffs," says Nina. She also plans to develop a complete series of open-source drawings that cover other functional uses, such as small tools.
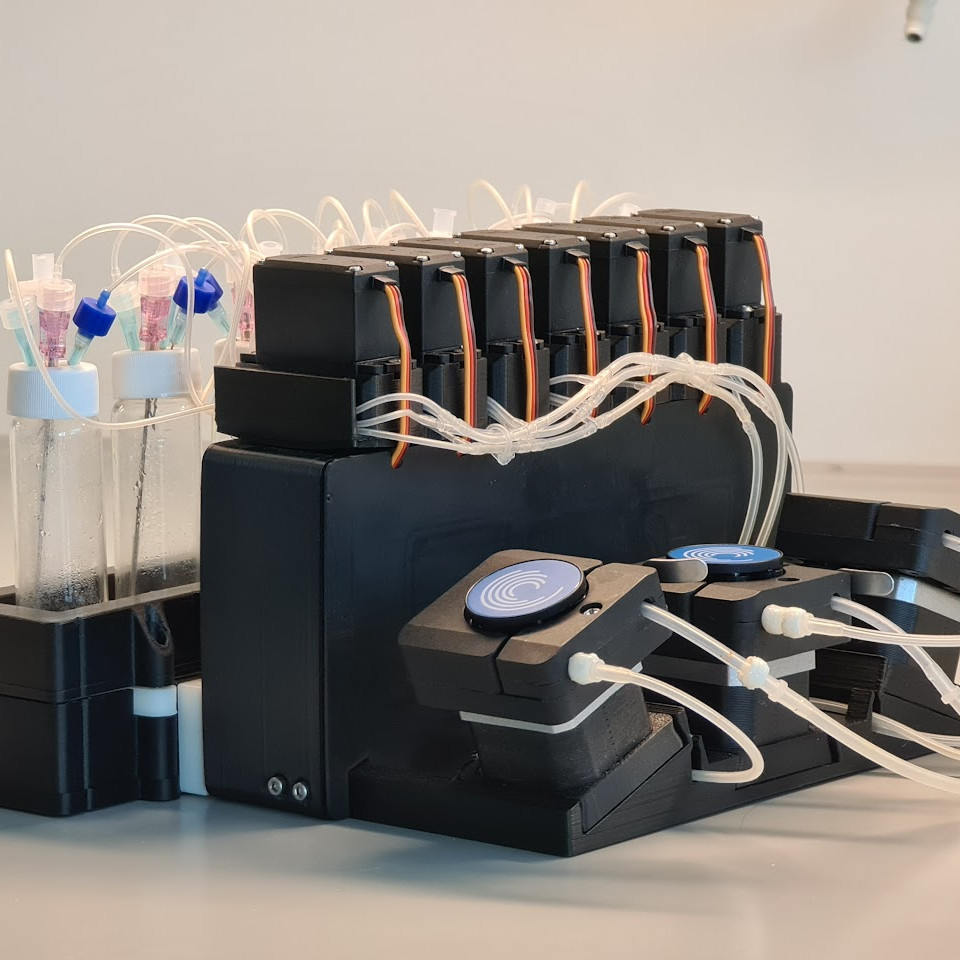
Replifactory - Catalin Rusnac
"Since my childhood, I've enjoyed building and repairing things. Later, I studied biotechnology and bioinformatics and realized that most biotechnological devices are inefficiently built and cost absurd amounts," Catalin shares.
With replifactory, Catalin has designed a 3D-printed laboratory device for cultivating bacteria. It enables a range of typical biological experiments, including acting as a morbidostat (maintaining a consistent stress level in the culture to adapt to challenges like antibiotics or metals). A morbidostat is a highly complex lab device that requires technical expertise for operation and maintenance due to inefficient existing designs.
Catalin has developed a version that is compact, easy to clean, and cost-effective to build. He now plans to further develop this version in the coming months.
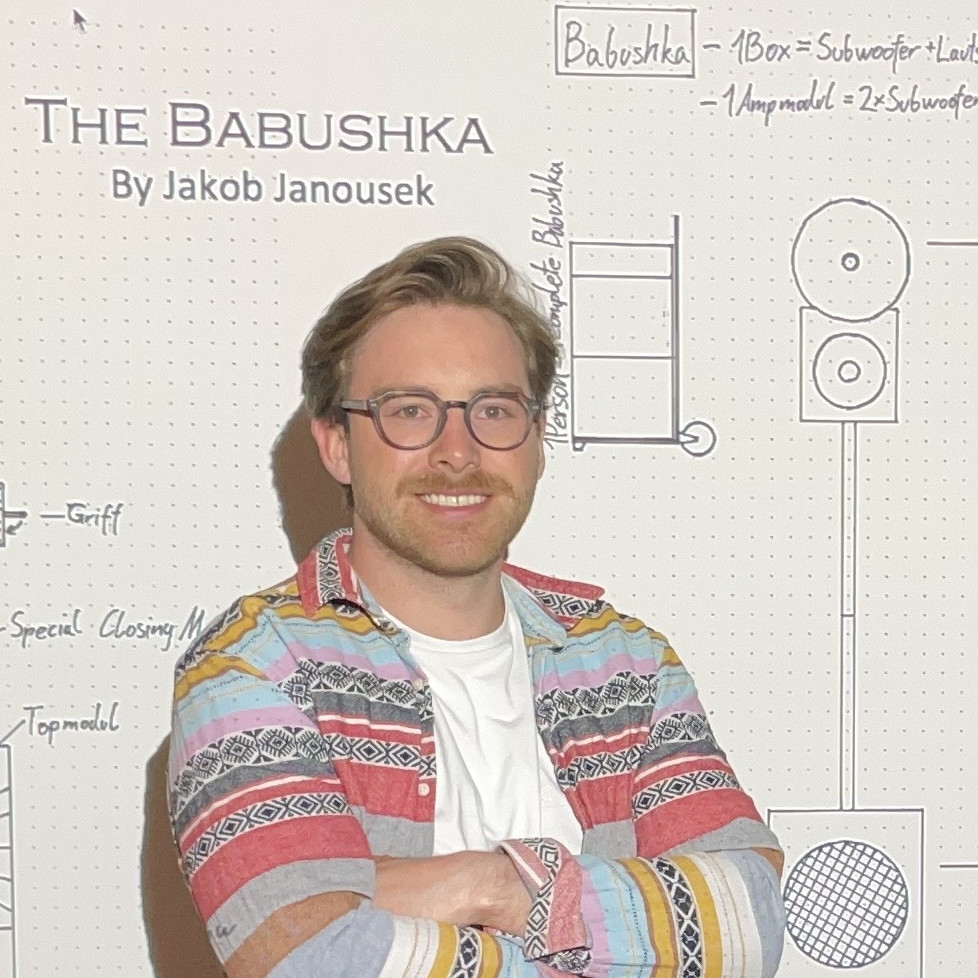
Baboushka - Jakob Janousek
„Ich bin ein Mensch mit sehr vielen Interessen. Am meisten und längsten beschäftige ich mich aber mit Lautsprechern. Seit meinen ersten richtigen Lautsprechern hat diese Leidenschaft einfach nicht abgerissen und nach einigen kleineren und mittleren Aufträgen will ich nun mein erstes, revolutionäres, Produkt entwickeln“, beschreibt Jakob seine Passion.
Bei Baboushka handelt es sich um ein komplettes PA (Public Adress)-System mit besonderem Augenmerk auf Transportabilität, Fidelity und Design. Das komplette System soll es möglich machen, dass eine Person die Lautsprecher mit maximal einer Lastenrodel transportieren und aufbauen kann. Mit einem speziellen System können im jeweiligen Subwoofer des 2.2 Systems die Tops samt benötigten Equipment verstaut werden. Außerdem soll das Top ein 3D-gedrucktes Horn bekommen, welches dem Ganzen ein einzigartiges Design verleiht.
All the works will be presented in a joint exhibition at Happylab in March 2024. Also, make sure to check out our social media channels to stay updated on the project's progress!
